近年來
隨著我國科技水平的提高
航空發動機技術取得了巨大的進步
陶瓷型芯是制造航空發動機的核心部件
由于陶瓷型芯內腔結構復雜
傳統方法往往難以進行加工
陶瓷型芯3D打印技術成為
陶瓷型芯加工的關鍵技術
為打破國外技術壟斷
北京工業大學3D打印中心
陳繼民教授團隊與康碩電氣
進行聯合技術攻關
自主研制大尺寸陶瓷型芯3D打印機
和高性能陶瓷成形材料
解決了我國陶瓷型芯3D打印發展的
“卡脖子”難題
下面和工小V一起
走近陳繼民教授團隊
和他們的陶瓷型芯3D打印技術
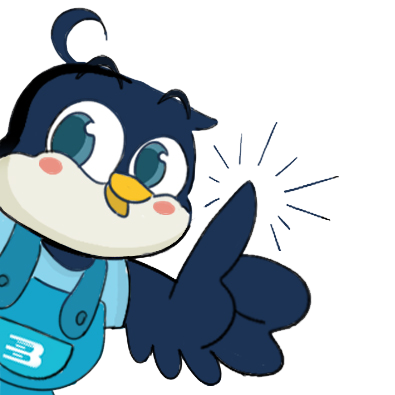
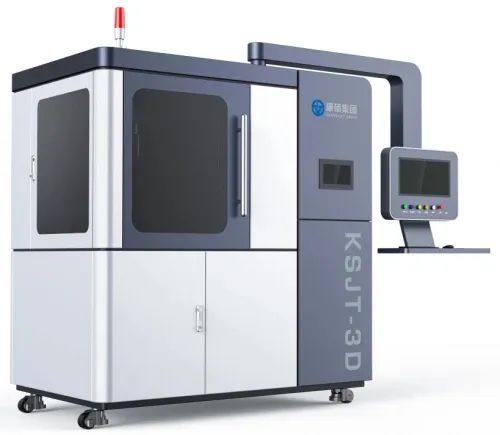
陳繼民教授團隊自主研發的陶瓷型芯3D打印設備,適用于精密鑄造、生物醫療等領域。目前,尚無同類型國產陶瓷型芯成形設備及配套陶瓷材料。項目中所開發的設備采用多項具有自主知識產權的專利技術,提出并實現了陶瓷3D打印新方式,填補了國內陶瓷3D打印的多項空白。研發的陶瓷打印材料、陶瓷型芯3D打印工藝,均處于國內領先水平。另外,項目開發的3D打印設備的主要性能指標,達到了國際先進水平,提高了國產陶瓷3D打印產品品質,為航空發動機陶瓷型芯的制造提供了技術支撐。
陶瓷型芯3D打印設備打印幅面大,打印零件燒結后產品致密接近100%理論密度,力學性能好,研制的打印材料滿足陶瓷型芯的要求,并可根據用戶需求進行定制開發。該設備采用的智能掃描算法,開發的分層掃描軟件,可進行無支撐結構制造。同時,此算法可大大縮短掃描時間,提高設備的打印速度。整套設備采用專利技術(一體化拓撲優化)設計方法,減輕了設備的重量,提高了運行速度,降低了生產成本。
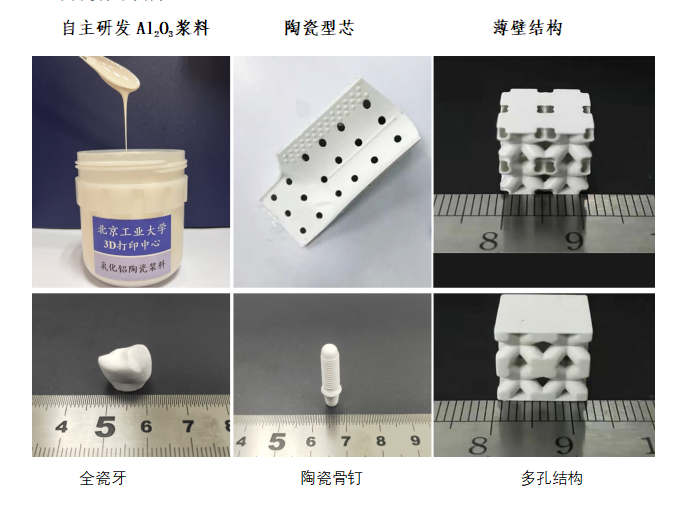
目前,陶瓷型芯3D打印設備已經投入工業化生產,填補了國內陶瓷3D打印的空白,為陶瓷3D打印的國產化鋪平了道路,實現了設備—材料—工藝閉環鏈條的自主可控。相關技術對3D打印陶瓷行業實現我國航空航天、生物醫療、機械電子領域關鍵零部件制造的國產化具有重大意義,將促進我國陶瓷3D打印工具軟件、裝備、材料與服務產業鏈的健全和健康發展,為打破國外技術壟斷,解決我國陶瓷型芯的“卡脖子”難題,具有積極的戰略意義。
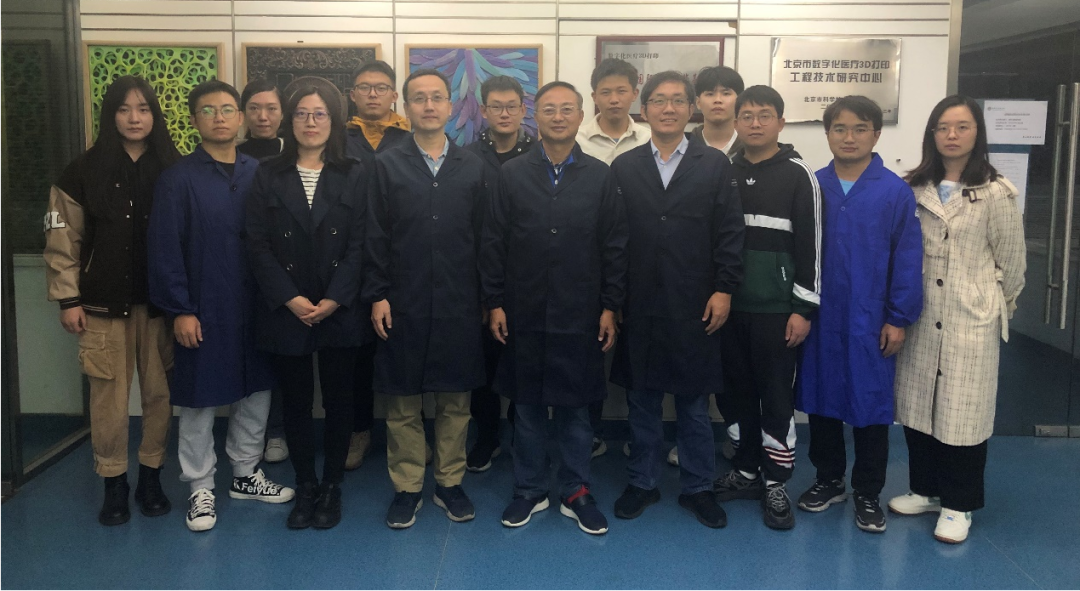
陳繼民教授團隊主要成員包括陳繼民教授、曾勇副研究員、王潛助理研究員和姚海華助理研究員等。團隊致力于3D打印技術的研究開發。十余年來一直開展3D打印裝備研制、打印材料以及工藝技術的開發等研究工作,多項成果成功應用于航空航天領域,解決了相關領域卡脖子難題,并在生物醫療等領域進行了應用。團隊總計發表SCI/EI論文100余篇,申請發明專利30余項,出版專著4部。獲北京市技術發明獎二等獎1項,中國發明協會發明創業成果二等獎1項,中國產學研合作創新獎1項,指導研究生參加各類科技競賽獲獎10余次。
攻堅克難,自主研發
潛心探索,識微見遠
科技強國,開啟新章
北工大人勇于擔當善于作為
助力實現高水平科技自立自強
以實際行動迎接黨的二十大勝利召開
原文始發于微信公眾號(北京工業大學):奮進新征程 | 北工大攻克陶瓷3D打印“卡脖子”難題
長按識別二維碼關注公眾號,點擊下方菜單欄左側“微信群”,申請加入交流群。
