陶瓷基板具有熱導率高、耐熱性好、機械強度高、熱膨脹系數低等優勢,是功率半導體器件封裝常用的散熱材料。根據封裝結構和應用要求,陶瓷基板可分為平面陶瓷基板和三維陶瓷基板兩大類。今天小編主要講述一下8種平面電子陶瓷基板的分類和制作技術,包括一些新型技術。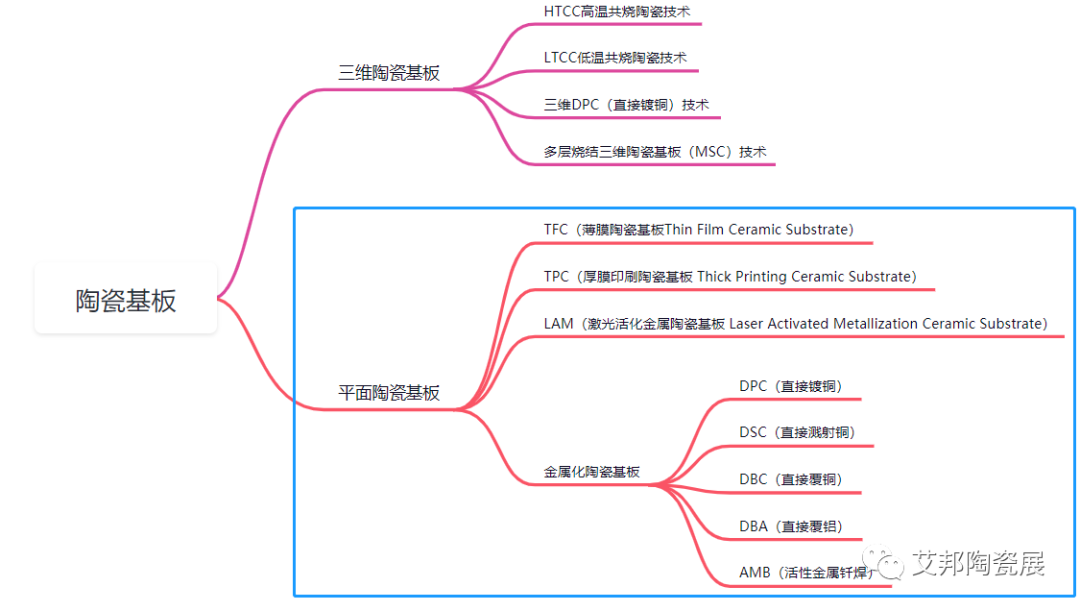
根據制備原理與工藝不同,平面陶瓷基板可分為薄膜陶瓷基板(Thin Film Ceramic Substrate,TFC)、厚膜印刷陶瓷基板(Thick Printing Ceramic Substrate,TPC)、直接鍵合銅陶瓷基板(Direct Bonded Copper Ceramic Substrate,DBC)、直接敷鋁陶瓷基板(Direct Bonded Aluminum,DBA)、活性金屬焊接陶瓷基板(Active Metal Brazing Ceramic Substrate,AMB)、直接電鍍銅陶瓷基板(Direct Plated Copper Ceramic Substrate,DPC)、直接濺射銅陶瓷基板(Direct Sputtering Ceramic,DSC)和激光活化金屬陶瓷基板(Laser Activated Metallization Ceramic Substrate,LAM)等。薄膜陶瓷基板一般采用濺射工藝直接在陶瓷基片表面沉積金屬層。如果輔助光刻、顯影、刻蝕等工藝,還可將金屬層圖形化制備成線路,由于濺射鍍膜沉積速度低(一般低于1μm/h),如下圖:因此TFC基板表面金屬層厚度較小(一般小于1μm),可制備高圖形精度(線寬/線距小于10μm)陶瓷基板,主要應用于激光與光通信領域小電流器件封裝。通過絲網印刷將金屬漿料涂覆在陶瓷基片上,干燥后經高溫燒結(溫度一般在850°C~900°C)制備TPC基板,其工藝流程如下圖所示。根據金屬漿料粘度和絲網網孔尺寸不同,制備的金屬線路層厚度一般為10μm~20μm(提高金屬層厚度可通過多次絲網印刷實現)。TFC基板制備工藝簡單,對加工設備和環境要求低,具有生產效率高、制造成本低等優點。但是,由于絲網印刷工藝限制,TFC基板無法獲得高精度線路(最小線寬/線距一般大于100μm)。此外,為了降低燒結溫度,提高金屬層與陶瓷基片結合強度,通常在金屬漿料中添加少量玻璃相,這將降低金屬層電導率和熱導率。因此TPC基板僅在對線路精度要求不高的電子器件(如汽車電子)封裝中得到應用。DBC陶瓷基板制備首先在銅箔(Cu)和陶瓷基片(Al2O3或AlN)間引入氧元素,然后在1065°C形成Cu/O共晶相(金屬銅熔點為1083°C),進而與陶瓷基片和銅箔發生反應生成CuAlO2或Cu(AlO2)2,實現銅箔與陶瓷間共晶鍵合,其制備工藝和產品分別如下圖所示。由于陶瓷和銅具有良好的導熱性,且銅箔與陶瓷間共晶鍵合強度高,因此DBC基板具有較高的熱穩定性,已廣泛應用于電子電力模塊(IGBT)、激光器(LD)、聚太陽能組件、半導體制冷器、LED器件等封裝散熱中。DBC基板銅箔厚度較大(一般為100μm~600μm),可滿足高溫、大電流等極端環境下器件封裝應用需求(為降低基板應力與翹曲,一般采用Cu-Al2O3-Cu的三明治結構,且上下銅層厚度相同)。雖然DBC基板在實際應用中有諸多優勢,但在制備過程中要嚴格控制共晶溫度及氧含量,對設備和工藝控制要求較高,生產成本也較高。此外,由于厚銅刻蝕限制,無法制備出高精度線路層。在DBC基板制備過程中,氧化時間和氧化溫度是最重要的兩個參數。銅箔經預氧化后,鍵合界面能形成足夠CuxOy相潤濕Al2O3陶瓷與銅箔,具有較高的結合強度;若銅箔未經過預氧化處理,CuxOy潤濕性較差,鍵合界面會殘留大量空洞和缺陷,降低結合強度及熱導率。對于采用AlN陶瓷制備DBC基板,還需對陶瓷基片進行預氧化,先生成Al2O3薄膜,再與銅箔發生共晶反應。直接敷鋁陶瓷基板(DBA)是基于DBC工藝技術發展起來的新型金屬敷接陶瓷基板,是鋁與陶瓷層鍵合而形成的基板,其結構與DBC 相似,也可以像PCB基板一樣蝕刻出各式各樣的圖形。圖?敷鋁基板技術,(a)液鋁敷接法,(b)金屬過渡法敷鋁基板技術有液鋁敷接法和金屬過渡法。金屬鋁在空氣中極易氧化,在鋁液表面生成一層致密的氧化鋁膜,大大降低了鋁液與陶瓷的潤濕性,影響陶瓷基板敷鋁過程及敷接強度,因此改善鋁與陶瓷的潤濕性是制備DBA陶瓷基板的必要條件。可通過去除鋁表面氧化層,或采用一定的措施隔絕氧氣,通過在陶瓷表面形成一層金屬過渡層,通過Al-金屬共晶液相,解決鋁與陶瓷界面潤濕性不佳的問題。圖?10kV/54A SiC MOSFET 模塊,來源:CPES通過DBA技術可以提高整個系統的散熱效率、可靠性和節省成本。DBA直接敷鋁基板將在高壓輸變電、智能電網、儲能系統、超級充電站、軌交等半導體器件、高壓光伏發電等應用領域極具市場前景。AMB陶瓷基板利用含少量活性元素的活性金屬焊料實現銅箔與陶瓷基片間的焊接,其工藝流程如下圖所示。活性焊料通過在普通金屬焊料中添加Ti、Zr、Hf、V、Nb或Ta等稀土元素制備,由于稀土元素具有高活性,可提高焊料熔化后對陶瓷的潤濕性,使陶瓷表面無需金屬化就可與金屬實現焊接。AMB基板制備技術是DBC基板工藝的改進(DBC基板制備中銅箔與陶瓷在高溫下直接鍵合,而AMB基板采用活性焊料實現銅箔與陶瓷基片間鍵合),通過選用活性焊料可降低鍵合溫度(低于800°C),進而降低陶瓷基板內部熱應力。此外,AMB基板依靠活性焊料與陶瓷發生化學反應實現鍵合,因此結合強度高,可靠性好。由于氮化硅Si3N4與銅之間不會形成Cu-Si-O化合物,無法使用DBC工藝,AMB工藝實現了氮化硅與銅的結合,在第三代半導體碳化硅功率器件和高導熱性、高可靠性、高功率等要求的IGBT模塊等方面極具潛力。DPC陶瓷基板制備工藝如圖所示。首先利用激光在陶瓷基片上制備通孔(孔徑一般為60μm~120μm),隨后利用超聲波清洗陶瓷基片;采用磁控濺射技術在陶瓷基片表面沉積金屬種子層(Ti/Cu靶材),接著通過光刻、顯影完成線路層制作;采用電鍍填空和增厚金屬線路層,并通過表面處理提高基板可焊性與抗氧化性,最后去干膜、刻蝕種子層完成基板制備。DPC陶瓷基板制備前端采用了半導體微加工技術(濺射鍍膜、光刻、顯影等),后端則采用了印刷線路板(PCB)制備技術(圖形電鍍、填孔、表面研磨、刻蝕、表面處理等),因此具有圖形精度高、可垂直互連、生產成本低等技術優勢,可普遍應用于大功率 LED 照明、汽車大燈等大功率 LED 領域、半導體激光器、電力電子功率器件、微波、光通訊、VCSEL、射頻器件等應用領域,市場空間很大。DSC(Direct Sputtering Ceramic)技術是指使用高離化、高沉積效率的新型持續高功率磁控濺射技術(C-HPMS)直接在陶瓷基板表面沉積一定厚度的金屬導電層的新型金屬化工藝。一種DSC陶瓷金屬化技術及其制備的陶瓷封裝基板,專利公布號:CN115028477A根據專利《一種DSC陶瓷金屬化技術及其制備的陶瓷封裝基板》(專利公布號CN115028477A),步驟包括:采用高離化率磁控濺射技術在陶瓷基板表面沉積金屬過渡層,采用持續高功率磁控濺射技術在金屬過渡層表面沉積金屬導電層,使用真空鍍膜技術在金屬導電層表面沉積表面功能層和/或表面保護層。相對DPC技術,采用DSC技術制備陶瓷封裝基板具有以下技術優勢:1)采用DSC技術制備的金屬導電層與陶瓷基板之間結合強度大幅度提高;LAM基板制備利用特定波長的激光束選擇性加熱活化陶瓷基片表面,隨后通過電鍍/化學鍍完成線路層制備,工藝流程如圖所示。圖 (a)LAM基板工藝流程;(b)LAM基板加工示意圖;(c)LAM基板產品(1)無需采用光刻、顯影、刻蝕等微加工工藝,通過激光直寫制備線路層,且線寬由激光光斑決定,精度高(可低至10μm~20μm),如圖5(b)所示;(2)可在三維結構陶瓷表面制備線路層,突破了傳統平面陶瓷基板金屬化的限制,如圖5(c)所示;(3)金屬層與陶瓷基片結合強度高,線路層表面平整,粗糙度在納米級別。從上可以看出,雖然LAM技術可在平面陶瓷基板或立體陶瓷結構上加工線路層,但其線路層由激光束“畫”出來,難以大批量生產,導致價格極高,目前主要應用在航空航天領域異型陶瓷散熱件加工。原文始發于微信公眾號(艾邦陶瓷展):電子封裝平面陶瓷基板的分類和制作技術