陶瓷球生產(chǎn)工藝大體分為球坯制備、球坯燒結、機械加工三大部分。通常球坯是由高純度原材料粉體壓制成型,再對壓制體進行燒結,隨后進行精密加工。

1.球坯成型
(1)干壓成型技術
干壓成型技術是陶瓷球一種常見的制備成型技術,具有操作簡單,工藝環(huán)節(jié)少的特點,將粉料倒入一定形狀的模具中,借助于模塞外加壓力,便可將粉料壓制成一定形狀的坯體,是目前大多數(shù)陶瓷球生產(chǎn)廠家采用的成型方法之一。但對于一些要求高精準尺寸及高力學強度的軸承球而言,干壓成型工藝制品尺寸不夠精準、球坯制造的精度缺陷也極為明顯,且此法只能做一維方向加壓,導致產(chǎn)品結構和強度存在各向異性。
采用傳統(tǒng)工藝(干壓成型)制備的陶瓷(軸承球,密封球)球坯,根據(jù)球坯尺寸不同,加工余量大約在1-3mm左右,將球坯加工為成品球,需經(jīng)歷約35-45天的精細后加工以獲取所需尺寸的成品球。完成加工后除去外觀色差、針孔等不合格球,其成品率可能只剩下30-40%左右,或者更低。不可控的成品率將導致供貨量不穩(wěn)定及大量的投料浪費。
(2)等靜壓工藝
等靜壓成型又叫靜水壓成型,是利用液體介質的不可壓縮性和均勻傳遞壓力性的一種成型方法。該法將預壓好的粉料坯體放入彈性的塑料或橡皮膠套內,然后置于一個能承受高壓脹力的鋼筒中,然后用高壓泵將液體打入簡體。膠套內的粉料將在各個方向受到同等大小的壓力,從而壓制成一定形狀的坯體。采用等靜壓工藝制備的陶瓷球,表面質量好、無氣孔、密度均勻、力學性能穩(wěn)定,在耐腐蝕、耐磨損、耐沖刷等性能方面有顯著提高。
這種成型方法的優(yōu)勢有利于獲取性能優(yōu)異的陶瓷球制品及大大減少后續(xù)精細加工時間。較小的加工余量大大減少了后加工的時間,根據(jù)球坯尺寸不同,其后加工時間可降低至25-30天左右。成型后通過等靜壓工藝制取的毛坯球質量好,可大大提升陶瓷球的成品率。毛坯球加工后的合格率可保證在90%以上,還能減少研磨盤等砂輪的無效損耗(用來磨次品,不良品浪費耗材),大大降低砂輪等耗材的損耗。因此,盡管通過等靜壓工藝制備的毛坯球要比干壓成型貴30%以上,但依然能使高精密陶瓷球的綜合加工成本大幅降低,等靜壓成型的球坯相比于干壓成型的毛坯而言能降低約30%-40%制備成本。但等靜壓成型成型設備昂貴,且存在脫模問題,限制了將其應用于大規(guī)模的工業(yè)生產(chǎn)。
(3)“行星式 ”滾動法
“行星式”滾動法就是將造好粒的陶瓷粉體放入滾動筒內,滴加少量去離子水,顆粒隨滾動筒的轉動而在筒壁上滾動,最終形成小球。該制備方法優(yōu)點是簡單易行,投資較少;缺點是小球尺寸分布較大。
(4)直接熱解法
直接熱解法適合以金屬的碳酸鹽為原料制備的陶瓷小球。它不僅能充分利用原料,而且環(huán)保;方法簡單,適合工業(yè)大規(guī)模生產(chǎn)。該工藝關鍵步驟是煅燒,熱分解反應產(chǎn)生大量氣體,必須緩慢升溫。
(5)反相懸浮聚合法
懸浮聚合是指借機械攪拌和分散劑使單體呈液滴狀分散于懸浮介質中,進行聚合反應的方法。其體系一般由單體、油溶性引發(fā)劑、水、分散劑四部分組成。反相懸浮聚合是將水溶性單體在有機溶劑中分散成細液滴而進行的聚合。
2.燒結工藝
陶瓷素坯在燒結前是由許許多多單個的固體顆粒所組成的,坯體中存在大量氣孔,氣孔率一般為35%-60%(即素坯相對密度為40%-65%),具體數(shù)值取決于粉料自身特征和所使用的成型方法和技術。當對固態(tài)素坯進行高溫加熱時,素坯中的顆粒發(fā)生物質遷移,達到某一溫度后坯體發(fā)生收縮,晶粒長大,伴隨氣孔排除,最終在低于熔點的溫度下(一般在熔點的0.5-0.7倍)素坯變成致密的多晶陶瓷材料,這種過程稱為燒結。燒結是陶瓷坯體成型的最后一道工藝,陶瓷產(chǎn)品的性能優(yōu)劣很大一部分因素是由燒結來決定的。要燒結的致密度高、均勻,不僅前一道加工工序脫脂環(huán)節(jié)至關重要,還受粉體、添加劑、燒結溫度及時間、壓力及燒結氣氛等因素的影響。
(1)無壓燒結
一般采用常規(guī)加熱方式,在傳統(tǒng)電爐中進行,是目前陶瓷材料生產(chǎn)中最常采用的燒結方法。由于純的陶瓷材料有時很難燒結,所以性能允許的條件下,通常引入一些燒結助劑,以期形成部分低熔點的固溶體、玻璃相或其他液相,促進顆粒的重排和粘性流動,從而獲得致密的產(chǎn)品,同時也可以降低燒結溫度。
(2)熱壓燒結
熱壓燒結采用專門的熱壓機,將干燥粉料置于模具中。在高溫下單相或雙相施壓完成。溫度與壓力的交互作用使顆粒的粘性和塑性流動加強,有利于坯件的致密化,可獲得幾乎無孔隙的制品,同時燒結時間短,溫度低,晶粒長大受到抑制,產(chǎn)品性能得到提高。
(3)熱等靜壓燒結
熱等靜壓燒結是一般熱壓法的改進,可使物料受到各向同性的壓力,從而使陶瓷的結構更均勻。熱等靜壓工藝是一種以氬氣等惰性氣體為傳壓介質,將制品放置到密閉的容器中,在一定溫度和壓力的共同作用下,向制品施加各向同等的壓力,對制品進行壓制燒結處理的技術,由于熱等靜壓燒結技術對包套材料及技術要求較高,因此通常用于制造形狀簡單的產(chǎn)品且生產(chǎn)效率低。
3.精密加工
球坯燒結后需對陶瓷球的尺寸及表面精度進行精密加工,分為粗磨和精磨兩大步驟。粗磨可消除毛坯球表面的各種缺陷,包括燒結氧化層、氣孔和表面微小裂紋等。單是通過粗磨加工,既不能使陶瓷球達到與鋼球相同的幾何形狀精度,也不能達到與鋼球相同的表面質量特性。必須再通過精磨工序才可以把粗磨加工形成的粗糙表面以及過大的形狀偏差研磨掉。從根本上來講,影響研磨加工工藝的主要是磨料和磨料液膜。細磨及精磨大都采用碳化硅、碳化硼和人造金剛石粉作磨料。精研及超精研選用氧化鉻、碳化硼、人造金剛石粉或天然金剛石粉作磨料。含有磨料的磨料液膜由煤油、脂、機油、磨料的混合溶液構成。根據(jù)不同種類磨料液膜,可以提高磨料的作用,或減輕磨料的作用,以此影響研磨能力和表面粗糙度。
目前,工業(yè)或實驗用的精密研磨陶瓷球方法已有很多,但根據(jù)其原理大體可以分為以幾種。
(1)四軸球面研磨
四軸球體磨球機采用的是四軸球體研磨方式,在研磨機主體機構的結構對稱性和四研具對球體相對運動的等同性的基礎上,利用反轉法對球體研磨成型原理進行球體研磨。這種研磨方式能夠獲得較高的加工精度(對直徑為φ10mm的球,球度可達0.05μm)。但這一技術主要用于單顆高精度球的加工,加工效率低。
(2)同心圓盤研磨法
同心圓盤研磨法是工業(yè)上用來加工鋼球的方法,也是現(xiàn)在工業(yè)上精加工陶瓷球最廣泛使用的方法。陶瓷球坯在成對制造的圓盤中間得到研磨,它可進行球的大量研磨。其中,上圓盤是靜止的,下圓盤安裝在行星系齒輪上,從而陶瓷球的運動有自轉和繞軸旋轉兩種運動方式,球與球之間會產(chǎn)生不可避免的相互摩擦和擠壓以至于研磨的精度受到了不良的影響從而導致這種研磨裝置的精度不高,因此這種同心圓盤研磨設備僅適于用作粗磨。
(3) V形槽研磨法
加工過程中,自旋角θ的值僅取決于球坯和研磨盤導向槽的直徑,與研磨盤轉速無關。由于自旋角θ在研磨過程中保持不變,球坯與研磨盤的接觸點在球坯表面形成的研磨跡線是一組以球坯自轉軸為軸的圓。球和研磨盤的運動機理以及機床結構與粗磨加工時相似,但由兩塊研磨盤取代金剛石板和導球板。上研磨盤浮動且必須具有精確導向。下研磨盤被加工成V型槽使,磨盤為V形和平面。陶瓷球與磨盤為三點接觸。此方法使球自轉軸均勻地變化,快速地去掉多余的加工留量,以完成研磨加工。研磨盤的硬度、盤溝的截面形狀(同心溝槽)和研磨壓力的相互作用,使磨料在兩個工作面間滾動時,由磨粒銳角產(chǎn)生切削作用。其結果是形成細微且無方向的加工痕跡,其與鋼球研磨時的磨削機理相一致。該種研磨方法與鋼球研磨類似可在小型精研機上完成,應用方便,但研磨效率很低。
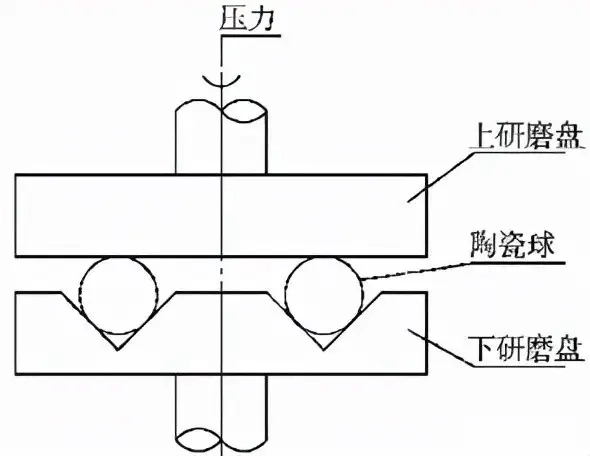
(4)自旋回轉角控制研磨法
自旋回轉角控制研磨法主要是改進傳統(tǒng)V形槽磨盤的運動狀態(tài)和裝置,使V形槽2個槽面的轉速可控,通過調整2個槽面的轉速,增大陶瓷球自旋回轉角,提高陶瓷球的加工效率。該方法所用機床的設計制造較復雜,不易實現(xiàn)陶瓷球的批量加工,但能明顯提高陶瓷球的加工效率,適用于大規(guī)格小批量陶瓷球的加工。
(5)錐形研磨方法
錐形研磨法基本原理與自旋回轉角控制研磨法相似。陶瓷球在研磨過程中具有較大的自旋角(達到47°),陶瓷球充分自旋,增大了陶瓷球的回轉滑動,從而使陶瓷球的加工效率大幅提高。該方法能夠大幅提高陶瓷球加工效率縮短加工時間,使用加工機床結構簡單、易于制造,但僅適合小批量加工,在大規(guī)格小批量陶瓷球加工中有優(yōu)勢。
(6)磁懸浮研磨法
磁懸浮研磨法是一項新的先進陶瓷精加工技術。磁懸浮研磨法是利用磁場力研磨的原理,性價比較高,這種方法目前僅處于實驗室研究階段,每批只能磨幾十粒陶瓷球,用于批量生產(chǎn)受到限制,需要進一步改進以提高產(chǎn)量。
來源:前沿材料