隨著節能減排要求的提高以及汽車電動化的加速,汽車輕量化成為汽車行業的發展潮流,推動著包括高強度鋼、鋁合金、工程塑料以及復合材料等在內的輕量化材料在汽車領域的應用。連續纖維增強熱塑性復合材料(CFRTP)作為一種高強度、高剛性、高韌性、可回收的新型熱塑性復合材料,與鋼、鋁合金相比,可以有相當的強度、重量更輕、能量吸收能力更高;與熱固性復合材料相比,更易于加工,且環保可回收,在汽車輕量化設計中具有巨大的應用潛力,可替代部分金屬材料和高端聚合物材料,應用于座椅靠背、前端模塊、車門內板、保險杠等車身結構件、半結構件上。
名稱 | OEM | 原材料 | 效益 |
座椅底板 | 通用歐寶Astra OPC | 巴斯夫?Ultramid? | 生產出的座椅底板減輕了45%的重量 |
獨立后排座椅外殼 | 奧迪A8 | 朗盛?Tepex? Dynalite | 與鋼板相比,重量減輕45% |
座椅靠背骨架 | 上汽概念車 | 巴斯夫?Ultracom? | 重量與傳統座椅相比減輕達20%,輕薄設計更為第二排乘客增加2.5厘米的膝部空間 |
越野車后排座椅 | | 朗盛?Tepex? Dynalite | 質量比類似鋼結構輕40%以上,同時可承受加速載荷的撞擊 |
前端模塊 | 大眾Atlas和Teramont | 朗盛?Tepex? Dynalite | 比用鋼板制成的嵌件約輕50%,CFRT嵌件區域可以承受更高的應力 |
輕量化A柱 | 保時捷 | 朗盛?Tepex? Dynalite | 重量減輕了5kg |
SUV前端支撐 | 梅賽德斯—奔馳GLE SUV | 朗盛?Tepex? Dynalite | |
車門基板 | 福克斯 | 金發科技 | 與鋼材及長纖維PP門系統相比,熱塑性復合材料門系統相對減重大于30% |
發動機底盤 | | 朗盛?Tepex? Dynalite | 重量比同等的鋼材組件輕了60%以上,比相應的鋁部件輕20%以上 |
懸架控制臂 | PSA標致 | | 重量減輕了50% |
剎車踏板 | 保時捷、賓利歐陸GT | 朗盛?Tepex? Dynalite | 重量僅有傳統鋼制踏板的一半左右 |
側門防撞梁 | PSA標致雪鐵龍 | 杜邦?Vizilon? | 與超高強度鋼(UHHS)相比,重量減少40%,能吸收更多的沖擊能量 |
消聲器隔熱罩 | 寶馬i8 | 朗盛?Tepex? Dynalite | 確保部件在高溫環境中不發生變形或失效,提高部件在冰凍溫度下的強度和抗沖擊性能 |
車輪觳插片 | 蔚來ES8 和ES6 | 科思創?Maezio? | 外觀優質,穩定性好 |
除了上述應用外,隨著技術的發展成熟,連續纖維增強熱塑性復合材料正越來越多地被用作汽車輕量化設計中金屬的替代品。下面我們來看看,近期連續纖維增強熱塑性復合材料在汽車上的創新應用。
一、寶馬ix前圍板和后窗框架部件
早在2010年,寶馬集團就在JEC World展會期間公布了其首款大量采用復合材料的電動乘用車,而在后面的i3、i8、7系設計中同樣大量采用了碳纖維復合材料。寶馬iX則是寶馬集團在大量采用復合材料的全電動設計方面取得的又一進展,在iX中,寶馬集團整合了7系的Carbon Core與之前寶馬i 系的全碳纖維的車身結構,它采用了多材料的車身結構,寶馬集團將這種車身結構稱作Carbon Cage。側框架、雨水槽、車頂框架、前圍板和后窗框架的 CFRP 部件組合形成一個“Carbon Cage ”,在加固車身的同時,減輕重量并提高車輛的靈活性。而前圍板和后窗框架部件采用全新方法由連續纖維增強熱塑性塑料 (CFRTP) 制成。
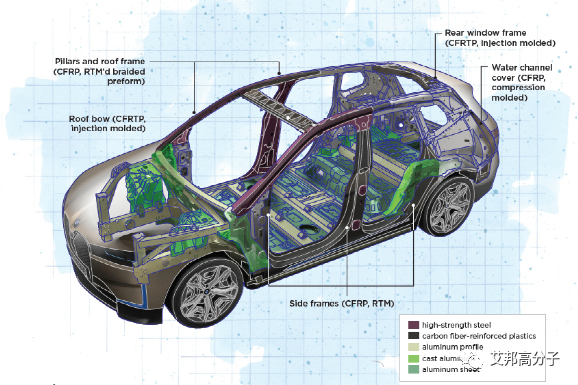
這種CFRP-CFRTP的混合結構與同樣的鋼制部件相比,在提高剛性的同時還減輕了5 kg的重量,同時實現了寶馬想要的簡約外觀,從而增加了乘員艙的寬敞感。
二、奔馳S級轎車駕駛輔助系統電池支架
在梅賽德斯-奔馳 S 級轎車的高級自動化駕駛輔助系統結構件中,采用朗盛Tepex? 連續纖維增強熱塑性復合材料制造電池支架,為該系統的“智能駕駛”供電。據介紹,這款弓形支架由德國洛恩的Poeppelmann Kunststoff-Technik 公司制造,它的基材為聚丙烯基 Tepex? dynalite 104-RGUD600(4)/47%,制造方法是將復合材料的成型(懸垂)與注射成型相結合的兩步法工藝。采用復合材料可以使成品可比金屬造的減重 40%,注塑成型步驟還可實現集成功能,不僅使安裝支架變得更加容易,而且還可減少了傳送運輸工作。這些加工工藝有助于降低制造成本。且復合材料對車身和電池的金屬部件是電絕緣的,大大降低了短路的風險。而由金屬制成的組件需要額外的措施來防止短路。三、梅賽德斯-奔馳S級轎車上的負載艙
朗盛Tepex dynalite連續纖維增強熱塑性復合材料的一項新應用是制造安裝在梅賽德斯-奔馳S級轎車上的負載艙,用于容納 48V 車載電源電池。這種復合材料部件能夠承受高機械應力,并且比同類金屬板部件輕30%左右,可以防止電池在發生碰撞時穿透或損壞凹槽壁,同時確保負載艙的密封性。
該部件采用混合成型工藝,坯料由基于聚酰胺6的Tepex dynalite 102-RG600(2)制成,并用兩層連續玻璃纖維織物增強。朗盛的 Durethan 聚酰胺6用于注塑緊固件和加強筋。除了S轎車外,Tepex dynalite還應用于梅賽德斯-奔馳 C 級轎車的負載艙,用于容納車載電源電池。輕質結構材料比金屬輕得多,未來將在電動汽車安全裝置、完整的電池系統外殼或引擎下可用的裝載空間組件方面有巨大應用潛力。四、東風汽車輕型卡車工具箱
SABIC與中國主要貨車制造商東風汽車合作,開發出一種用于生產堅固而且輕量化的車載工具箱新型復合塑料混合解決方案。該應用混合了SABIC的 STAMAX? 長玻纖聚丙烯樹脂和一種連續玻纖復合層壓嵌件,采用雙色注塑工藝生產。與類似設計的鋼制零件相比,采用該方案生產的成品零件重量減輕了30%,并有效提高了東風汽車的生產效率。SABIC的混合解決方案結合了 STAMAX 樹脂與熱成型復合嵌件,這款嵌件由連續玻纖增強熱塑性復合材料生產商江蘇奇一科技生產的單向玻纖增強聚丙烯帶制成。層壓嵌件在放置入模具之前需進行預熱,并在一次操作中與 STAMAX 樹脂一同進行雙色注塑成型。這一嵌件可提高零件關鍵區域的剛度和強度,從而實現薄壁幾何設計,以此減輕零件重量。采用塑料復合解決方案生產的卡車工具箱重量減輕了約 30%(4-6kg),同時保證了應用所需的剛度、韌性和強度。綜上,高性能、低密度的連續纖維增強熱塑性復合材料已成為汽車輕量化中極具潛力的材料之一,在汽車半結構、結構件上廣泛應用。從材料上看,國外連續纖維復合材料產業日趨完善,應用相對成熟,而國內相關企業的產品也逐步得到汽車制造商的認可。從工藝上來看,大批量自動化,以及多工藝材料的復合生產技術,符合未來汽車行業輕量化與集成化設計的發展趨勢。原文始發于微信公眾號(艾邦高分子):盤點連續纖維增強熱塑性復合材料在汽車上的應用