?
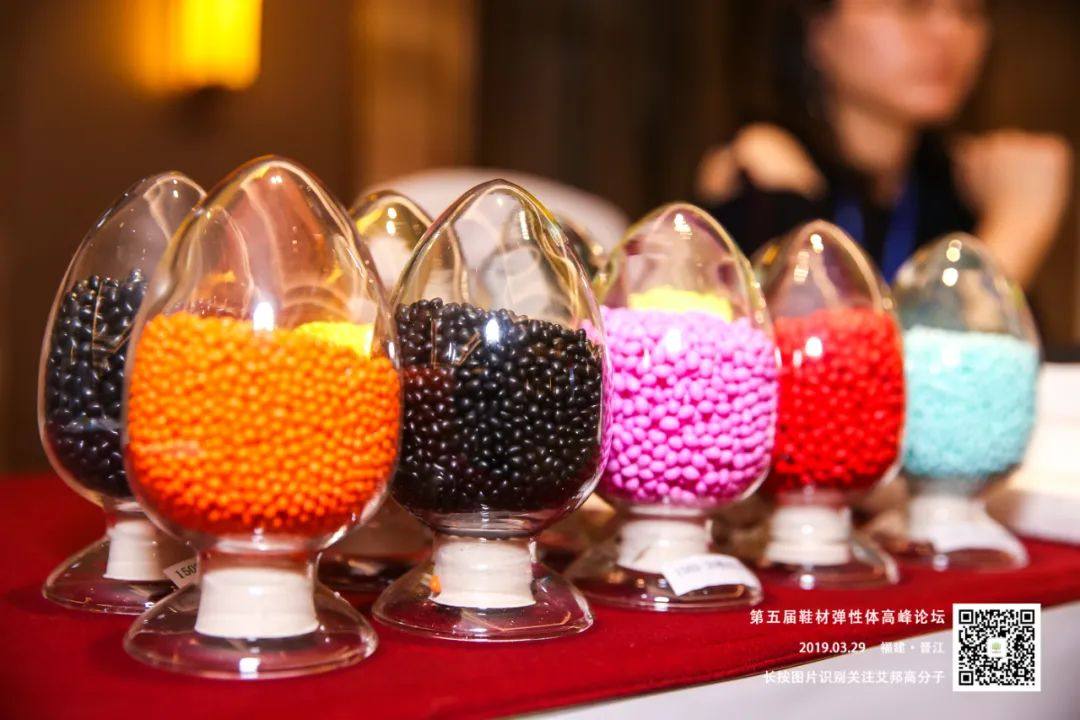
熱塑性聚氨酯(TPU)注塑成型時,干燥預(yù)熱后的TPU粒料從注塑機料斗輸送進加熱的料筒,呈熔融狀態(tài)時,經(jīng)螺桿(或柱塞)的推進作用及料筒前端的噴嘴注射進入溫度相對較低的閉合模具中,充滿模腔,并在受壓下冷卻固化,脫模后獲得與模型型腔相同的TPU產(chǎn)品。
從TPU注塑成型工藝看出,TPU注塑成型產(chǎn)品最重要的模塑條件是影響塑化流動和冷卻的溫度、壓力和時間。
針對TPU的特性,特別是其加工溫度波動范圍尤為狹窄的特點,要求注塑機必須具備精確的溫度調(diào)節(jié)和控制系統(tǒng),否則會因各種因素造成制品缺陷。如果我們把次廢品的成因涵蓋在四個主要因素當中,那就是原料、模具、注塑機及注射條件。
TPU成型產(chǎn)品,原則上都是依據(jù)標準規(guī)格要求制造的。但它的變化仍是相當廣泛并具有突發(fā)性。有時,在生產(chǎn)過程中會產(chǎn)生凹陷、氣泡、裂痕、變形等次廢品。因此就要從次廢品中來了解判斷問題所在并提出解決辦法,這是專業(yè)技術(shù)和實踐經(jīng)驗的積累。其實有時只需變更操作條件或原料、模具、機器方面稍做處理和調(diào)整,就可以解決問題。本文以螺桿式注塑機生產(chǎn)TPU制品為例,列舉了TPU注塑成型制品缺陷可能發(fā)生的問題及原因,并加以探討解決之道。
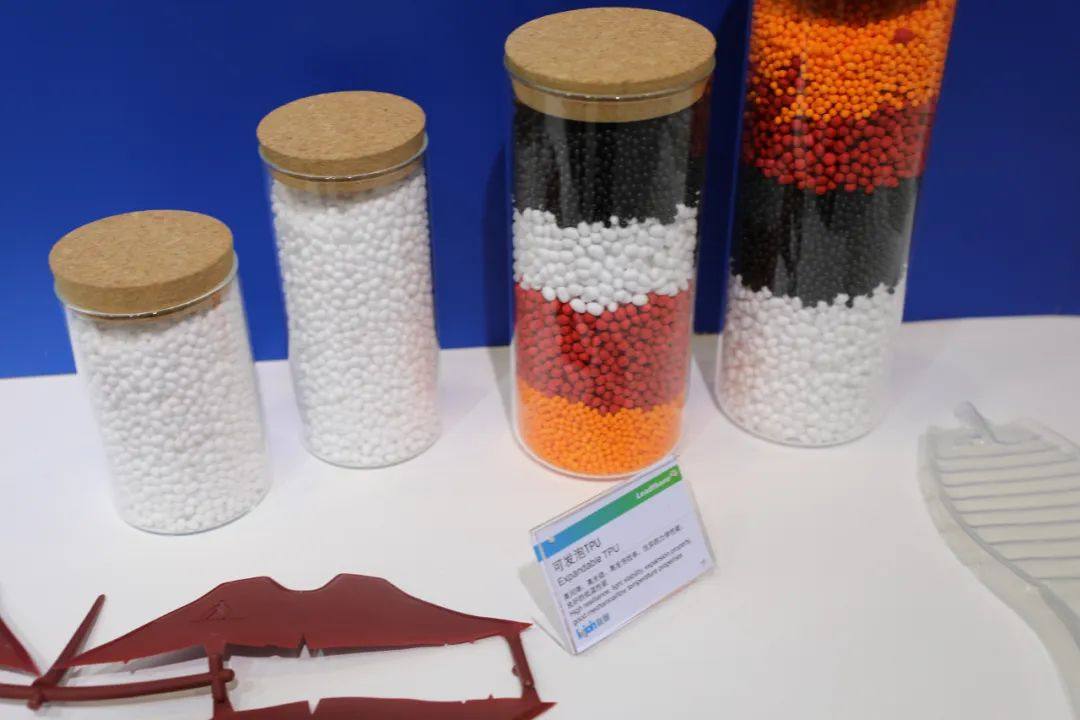
TPU制品表面的凹陷,會降低成品品質(zhì)及強度,同時也會影響產(chǎn)品外觀。凹陷的原因與使用的原料、成型技術(shù)及模具設(shè)計均有關(guān)系,如原料的縮水率、注射壓力、模具的設(shè)計及冷卻裝置等。
在注塑成型過程中,制品有時會出現(xiàn)有許多氣泡的制品,這會影響其強度及機械性能,對制品外觀亦大打折扣。通常制品因厚薄不均,或模具有突出肋時,物料在模具中冷卻速度不同,導致收縮不均,容易形成氣泡,所以對模具設(shè)計須特別留意。
另外原料干燥不充分,仍含有部分水份,在熔料時受熱分解成氣體,容易進入模腔內(nèi)形成氣泡。所以當制品出現(xiàn)氣泡時,可檢查下列幾個因素,并做處理。
裂痕是TPU制品的致命現(xiàn)象,通常表現(xiàn)為制品表面產(chǎn)生毛發(fā)狀的裂紋。當制品有尖銳棱角時,此部位常發(fā)生不易看出的細裂紋,這對制品來說是非常危險的。生產(chǎn)過程中發(fā)生裂痕的主要原因如下:
1.?脫模困難;
2.?過度充填;
3.?模具溫度過低;
要避免脫模不良所致的裂痕,模具成型空間須設(shè)有充分的脫模斜度,頂針的大小、位置、形式等要適當。頂出時,成品各部分的脫模阻力要均勻。
過度充填,是因施加過大的注射壓力或材料計量過多,使制品內(nèi)部應(yīng)力過大,脫模時造成裂痕,在此狀態(tài)下,模具配件的變型量也增大,致使更難脫模,助長裂痕(甚至破裂)的發(fā)生,此時應(yīng)降低注射壓力,防止過度充填。
澆口部位常易殘留過大的內(nèi)部應(yīng)力,澆口附近易脆化,特別是直接澆口的部分,易因內(nèi)部應(yīng)力而破裂。
TPU注塑制品出現(xiàn)翹曲、變形的原因是冷卻定型時間過短、模溫過高、不勻及流道系統(tǒng)不對稱等。因此在模具設(shè)計時要盡量避免以下各點:
1.?同一塑件中厚薄相差太大;
2.?存有過度銳角;
3.?緩沖區(qū)過短,使厚薄轉(zhuǎn)彎相差懸殊;
此外,還要注意要設(shè)置合適的頂針數(shù)量和設(shè)計合理的模腔冷卻流道。
表四為翹曲、變形可能產(chǎn)生的原因及處理方法
焦斑或黑紋是指制品有黑色斑點或黑色條紋的現(xiàn)象,其發(fā)生的主要原因是原料的熱穩(wěn)定性不良,由原料的熱分解所致。
有效防止焦斑或黑紋發(fā)生的對策是防止熔料筒內(nèi)的原料溫度過高,減慢注射速度。熔料筒內(nèi)壁或螺桿有傷痕或缺口,則會附著部分原料,此部分原料會因過熱導致熱分解。此外,止逆閥亦會因原料滯留而引起熱分解。所以,使用粘度高或容易分解的原料時要特別注意防止焦斑或黑紋的發(fā)生。
表五為焦斑或黑紋可能產(chǎn)生的原因及處理方法
6、制品有毛邊
毛邊是TPU制品常遇到的問題。當原料在模腔內(nèi)的壓力太大,其所產(chǎn)生的分模力大過鎖模力,從而迫開模具,使原料溢出形成毛邊。形成毛邊的原因可能有多種,如原料方面的問題,或是注塑機的問題,或是調(diào)校不當,甚至模具本身也有可能。所以,在判定毛邊產(chǎn)生的原因時,要從易到難進行。
-
檢查原料是否徹底焙干、是否混入雜物、是否混合不同種類的原料、原料粘度影響;
-
正確調(diào)校注塑機的壓力控制系統(tǒng)及注射速度的調(diào)整必須配合所采用的鎖模力;
-
模具某些部位是否有磨損、排氣孔是否阻塞、流道設(shè)計是否合理;
-
注塑機模板之間的平行度是否有偏差、模板拉桿受力分布是否均勻、螺桿止逆環(huán)和熔料筒是否磨損。
|
|
|
|
|
|
|
|
|
|
|
|
|
檢查轉(zhuǎn)換壓力位置,重新調(diào)校提早轉(zhuǎn)換
|
|
|
|
|
|
|
|
|
|
|
|
|
|
|
|
|
|
|
|
|
|
|
|
|
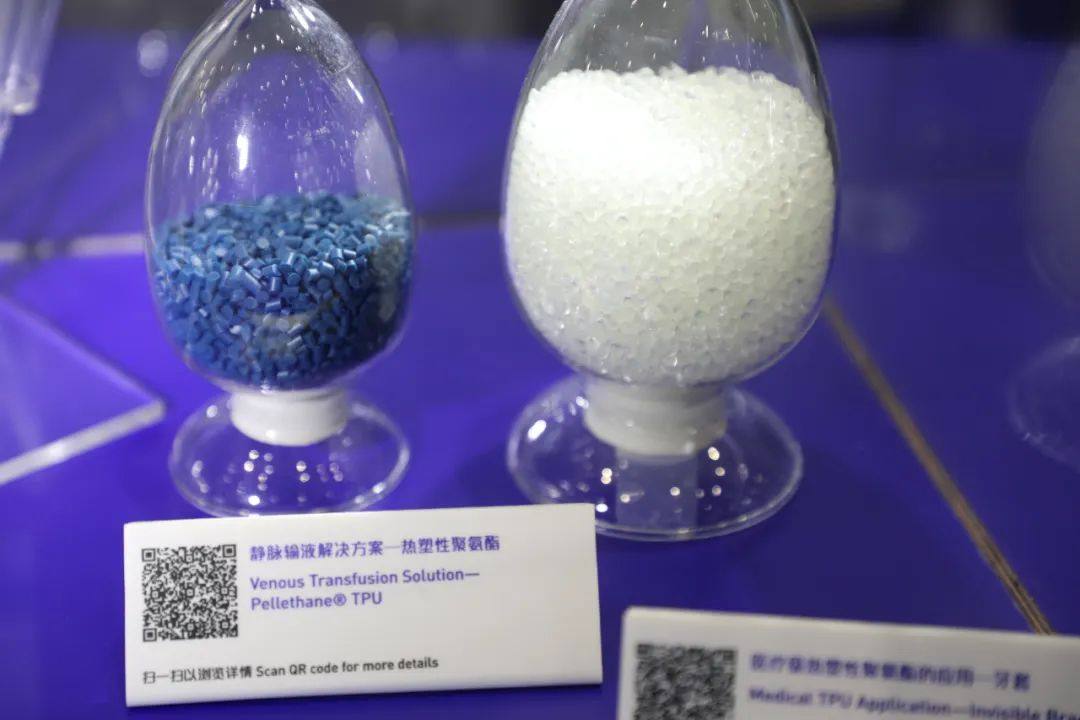
TPU在注塑成型發(fā)生制品粘模時,首先要考慮注射壓力或保壓壓力是否過高。因為,注射壓力太大會造成制品過度飽和,使原料填入其它空隙而使制品卡在模腔中造成脫模困難。其次,當熔料筒溫度過高時,會使原料受熱分解變質(zhì),在脫模過程中出現(xiàn)破碎或斷裂,造成粘模。至于模具方面的問題,如進料口不平衡,使制品冷卻的速率不一致,也會造成制品在脫模時發(fā)生粘模現(xiàn)象。
韌性是使材料斷裂所需要的能量。引起韌性降低的主要因素有:原料、回收料、溫度及模具等。而制品的韌性降低,將直接影響制品強度和機械性能。
表八為韌性降低可能產(chǎn)生的原因及處理方法
TPU制品充填不足是指熔融的材料未完全流遍成形窨的各角落之現(xiàn)象。充填不足的原因有成型條件設(shè)定不當、模具的設(shè)計制作不完善、成型品的肉厚壁薄等。在成型條件方面的對策是增高材料、模具溫度,增大注射壓力、注射速度及提高材料的流動性。模具方面可增大澆道或流道尺寸,或?qū)部谖恢谩⒋笮 ?shù)量等進行調(diào)整修改,使熔融材料流動順暢。再者,為了使成形空間內(nèi)的氣體順利疏散,可在適當位置設(shè)置排氣孔。
表九為充填不足可能產(chǎn)生的原因及處理方法
結(jié)合線是熔融材料二道或二道以上合流的部分所形成的細線,通常亦稱焊接線。結(jié)合線不僅影響制品的外觀,同時也不利于制品的強度。結(jié)合線發(fā)生的主要原因有:
1.制品形狀(模具構(gòu)造)所致材料的流動方式;
2.熔融材料合流性不良;
3.熔融材料合流處混入空氣、揮發(fā)物或難熔物等。
升高材料和模具溫度,可使結(jié)合線的程度減至最小。同時,改變澆口的位置、數(shù)量,使結(jié)合線的位置移往他處;或在熔合部設(shè)置排氣孔,迅速疏散此部位的空氣及揮發(fā)物;或在熔合部附近設(shè)材料溢流池,將結(jié)合線移至溢流池,再將其切除等都是有效地消除結(jié)合線的對策。
表十為結(jié)合線可能產(chǎn)生的原因及處理方法
TPU制品表面失去材料本來的光澤,形成層膜或模糊狀態(tài)等,皆可稱為表面光澤不良。
制品表面光澤不良,大都是由于模具成形表面研磨不良引起。當成形空間表面狀態(tài)良好時,提高材料和模具溫度可增強制品表面光澤。使用過多的難融劑或油脂性難融劑亦是表面光澤不良的原因。同時,材料吸濕或含有揮發(fā)物及異質(zhì)物混入污染也是造成制品表面光澤不良的原因。所以,要特別注意模具和材料方面的因素。
表十一為表面光澤不良可能產(chǎn)生的原因及處理方法
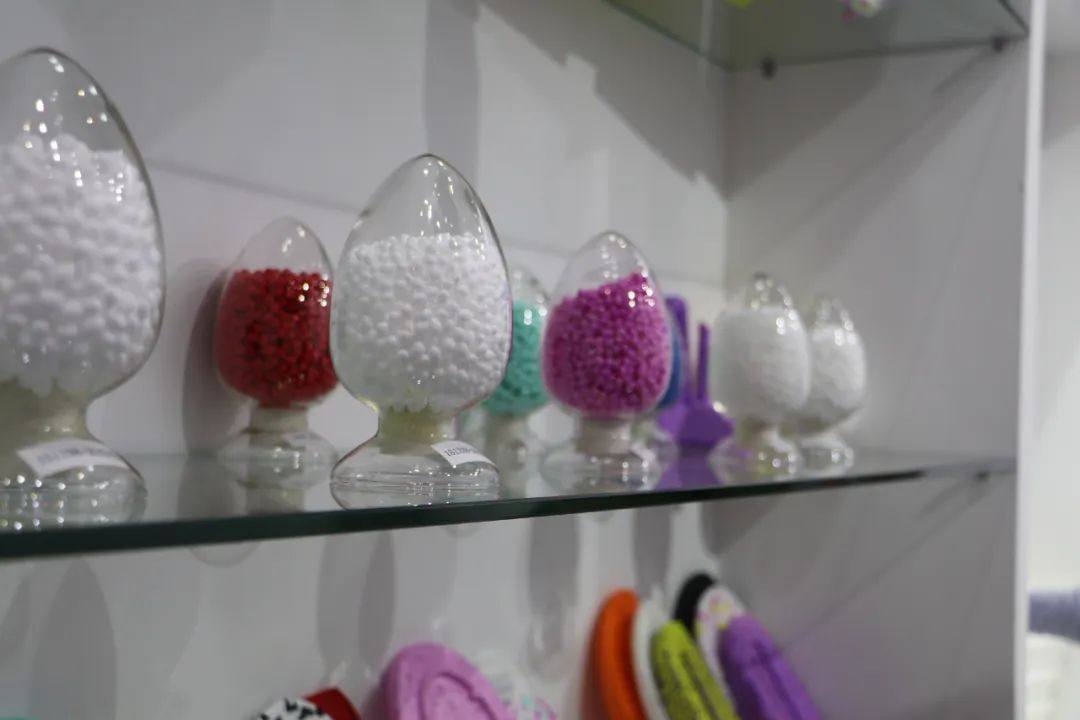
流痕是熔融材料流動的痕跡,以澆口為中心而呈現(xiàn)的條紋模樣。
流痕是最初流入成形空間內(nèi)的材料冷卻過快,而與其后流入的材料間形成界線所致。為了防止流痕,可提高材料溫度,改善材料流動性,調(diào)整注射速度。
殘留于射嘴前端的冷材料,若直接進入成形空間內(nèi),則會造成流痕。因此在澆道與流道的匯合處或流道與分流道的交接處設(shè)充分的滯料部位,可有效地防止流痕的發(fā)生。同時,也可通過增大澆口尺寸來防止流痕的發(fā)生。
表十三為螺桿打滑可能產(chǎn)生的原因及處理方法
表十四為螺桿無法轉(zhuǎn)動可能產(chǎn)生的原因及處理方法
表十五為注射嘴漏料可能產(chǎn)生的原因及處理方法
表十六為材料未熔盡可能產(chǎn)生的原因及處理方法

原文始發(fā)于微信公眾號(艾邦彈性體網(wǎng)):TPU注塑成型工藝與缺陷解決方法總結(jié)