CVD是Chemical Vapor Deposition的簡稱,是指高溫下的氣相反應。
例如,金屬鹵化物、有機金屬、碳氫化合物等的熱分解,氫還原或使它的混合氣體在高溫下發生化學反應以析出金屬、氧化物、碳化物等無機材料的方法,這種技術zui初是作為涂層的手段而開發的。
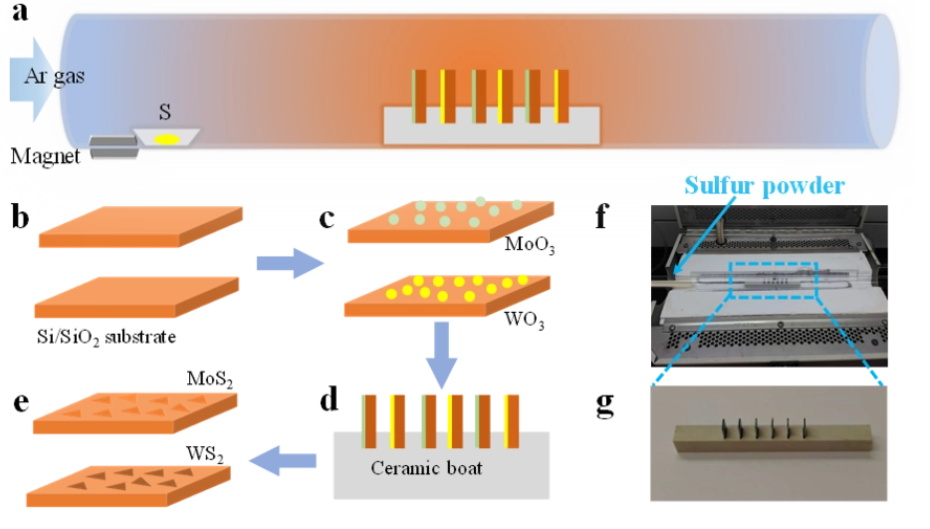
CVD工藝的技術特征:
-
-
析出物質的形態在單晶、多晶、晶須、粉末、薄膜等多種。
-
不僅可以在基片上進行涂層,而且可以在粉體表面涂層等等。特別是在低溫下可以合成高熔點物質,在節能方面做出了貢獻,作為一種新技術是大有前途的。
在涂層技術的發展中,高溫和中溫CVD涂層技術是基本的,在多層或納米涂層中,可通過添加不同金屬和涂層微觀結構改性來改變涂層性能。
由于CVD為高溫工藝,可增強所有擴散及冶金工藝,因此所有涂層特性取決于基體材料。CVD涂層工藝成功應用的第三個關鍵因素是必須得有工業化的生產設備及生產工藝。這包括在很短響應時間內實現自動工藝控制(如納米結構)以及可精確控制前驅物質的各源。
含鉻和釩的硬質合金有很高的硬度及一定的韌性,其熱膨脹系數接近鋼。使用這些材料沉積擴散涂層可獲得非常好的結合力。
工業CVD工藝在中溫下,在油淬的碳鋼制零部件上沉積硬質涂層,某些情況下會產生不一致的結合力。通過含Cr或V的擴散過渡層,工藝和結合力可得到很好的控制。圖1展示了結合力較差的涂層(見圖1a)和通過Cr擴散涂層獲得的結合力較好的涂層(見圖1b)。
圖1 MT-TiCN在碳鋼零件上獲得的較差結合力和通過擴散涂層而改進的結合力
這些復合涂層的實現需要額外的前驅物質及設施用于沉積工藝。在上例中,需要額外的發生器來產生揮發性的含Cr化合物——CrClx[2]。在此發生器中,不同的金屬(粒狀或碎屑狀)與氯氣或氯化氫進行反應。而此發生器的使用不應將最終的Cr或V殘留物帶入到后序的涂層中(如氧化鋁)。
使用帶內部金屬氯化物發生器的同一CVD設備,可沉積帶摻雜的CVD涂層,通過加入一定量的一種或幾種合金(如鉻、釩、鎢或鉈)來改善TiN,TiC或Ti(C,N)涂層性能。
形成的涂層一般為(Ti100-a-b-cCraVbWc)CxNyOz,其中x+y+z=1,其機械性能(如硬度及韌性)與TiN,TiC和Ti(C,N)類似,但由于合金元素的存在,其抗腐蝕性能也得到改善。
從早期的研究[3]可知,在中溫Ti(C,N)中添加硼可改變Ti(C,N)典型的柱狀結構,獲得相當高的硬度。在實際應用中,由于其較高的內部應力及脆性,這種涂層僅限于非常薄的涂層。
因此,通過改變多層CVD涂層的結構,從微米級到納米級,從而改善涂層性能的研究已經展開。在短暫時間內實現精確控制三氯化硼的流量可獲得此納米涂層。
單一涂層厚度從30nm到60nm的可重復多層涂層已經可進行沉積,在保持納米結構情況下,總涂層厚度最高可達到10μm。CVD沉積的納米涂層SEM掃描電鏡照片見圖2。
沉積非常厚的涂層時,通常晶粒會變得粗大,表面會變得粗糙。這會降低刀具的使用壽命,涂層后拋光處理成本會有所增加。通過摻雜硼來改變結構,可獲得非常光滑和光亮的表面。圖3和圖4展示了單純沉積MT-TiCN涂層和通過改變多層涂層結構而改進結構和表面形貌的對比(總涂層厚度最厚60μm)。
圖4 MT-TiCN多層涂層斷面及表面形貌
除了硼,還研究了硫和氧對晶粒細化的影響。圖5顯示硫僅有稍微的影響,氧和硼可產生顯著的晶粒細化效果及表面光滑效果。
高溫改性氧化鋁應該是防護涂層中應用最成功的抗氧化材料。常見的應用是在硬質合金切削刀片上的氧化鋁涂層。
不同金屬基體材料和真正陶瓷涂層之間良好的結合力僅能通過使用過渡層來獲得,此過渡層可實現以下功能:
催化效應在實際應用中至關重要。含高Co和Cr的合金可用作醫療植入部件材料,這些合金展示了良好的生物兼容性和高機械強度,但是,摩擦性能并不理想,微小的磨損毛刺會產生有害的金屬離子。
另一方面,塊狀氧化鋁植入件已在醫療領域廣泛應用,但在抗沖擊強度和復雜外形成形方面仍有一定的局限性。
在Ti(C,N)和常規氧化鋁涂層沉積過渡層可獲得較好的機械性能和涂層表面形貌,但Ti(C,N)-Al2O3過渡層易于結合失效。
如圖6所示,可重復生產的涂層僅能在齒狀過渡層上獲得,齒狀過渡層能增大內部擴散面積并作為諸如機械互鎖增加結合力。
圖6 Co基合金上多層涂層(可看到齒狀過渡層)的Al2O3掃描電鏡照片
相對于上述涂層系統,一些難熔合金(如鈮、鉭)能直接在其表面沉積氧化鋁硬質涂層(見圖7)。這為在含鈦過渡層為最薄弱環節的抗氧化性高溫應用領域開啟了新的應用。和硬質合金刀片的氧化鋁涂層類似,此類涂層也需要對表面進行一定的特殊改性來獲得理想的氧化鋁結構(α或κ)。
當有合適的工業涂層設備時,上述所有工藝才能實現成功穩定的生產。總之設備的使用者要求:
針對化學和熱處理工藝過程,CVD設備設計的關鍵因素如下:
物質平衡:熱動力學決定了反應發生的條件。不同的涂層工藝,需要有一定量的前驅物。
顯然,在一個有數平方米表面的大型成型模具上涂層和在一個有數平方米內表面的過濾器上涂層是不同的。前驅物,室溫下的液體可使用現代化的液體質量流量計而達到幾乎無限的體積量。
特別是低氣相壓的氯化物不僅需要較高的反應器溫度,而且必須工作在可控負壓下以獲得足夠高的金屬氯化物濃度(見圖8)。
圖8 使用氯氣作為氯化反應物的NbCl5發生器,工作在獨立壓力下的可控沉積工藝
進入系統的前驅物數量也決定了副產品的量或過多的前驅物。傳質可控CVD反應會與過多的前驅物一同工作以便在整個反應器內維持理想的涂層均勻性。
這會產生廢物管理,即副產品的處理,應不致使下游的泵系統和壓力調節裝置堵塞。通常的方式是使用高效的冷凝捕捉器(見圖9)。
動力學:確保整個反應器內涂層均勻性的最有效方法是改變停留時間(即物質經過經加熱的沉積區的停留時間)。
例如,短的停留時間可通過縮短反應器內距離實現,如帶中央旋轉進氣系統在管狀反應器內,其停留時間可縮短5個因子。或在低壓下進行沉積工藝,不同的真空系統,停留時間可減少10-1000個因子。
低壓的額外優點是氣體分子的自由程在低壓下會增加,從而可提高盲孔和小開孔內涂層的均勻性以及更復雜刀具形狀涂層的能力。
熱平衡:溫度的均勻性也非常重要。反應器和需要涂層的零件的控制溫度通常是已知和可控的,主要的影響是工藝氣體的溫度很難測量,理想狀態下,進入的氣體直至未排放反應物仍保持低溫,僅在距需要涂層的零件很短的距離內達到其反應溫度。
顯然,新一代的CVD工藝需要通過精確的多樣性工藝控制系統在較短的響應時間內進行管理。
CVD設備不同應用(如擴散涂層,摻雜元素,多層涂層系統到納米涂層)已經實現,設備革新和涂層參數控制的重要性已經顯現,以便沉積所需厚度和性能的涂層。工藝開發、過程控制和符合工業要求的工業化設備需要大規模的投資及工程資源。
原文始發于微信公眾號(光伏產業通):CVD工藝及設備技術