在 20 世紀 60 年代后期以及整個 1970 年代和 1980 年代,熱塑性膠帶被用于制造各種復合材料部件和結構,特別是在軍事和國防應用中。?不難看出熱塑性膠帶的吸引力。作為 UD帶,它們可以應用于許多受力結構,它們是可熔融加工的,并且可以通過壓模成型(即熱壓罐外)或壓縮成型(圖 1 和圖 2)輕松快速地進行固結。它們提供了熱固性材料無法比擬的韌性,而且與熱固性預浸料不同,它們可以在室溫下無限期儲存。?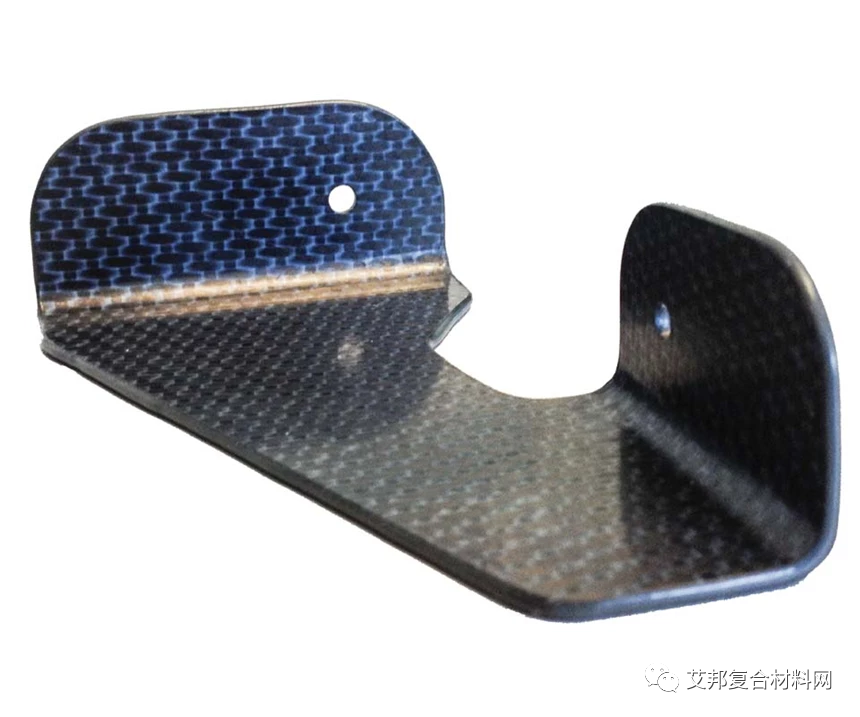
圖 1:CFRTP:從支架到大零件?
該夾子由 TenCate 提供的編織碳纖維熱塑性材料模壓而成,象征著該材料在航空航天應用中的潛力。現在正在努力將增強熱塑性塑料用于大型、重載的航空結構。
資料來源:TenCate Advanced Composites
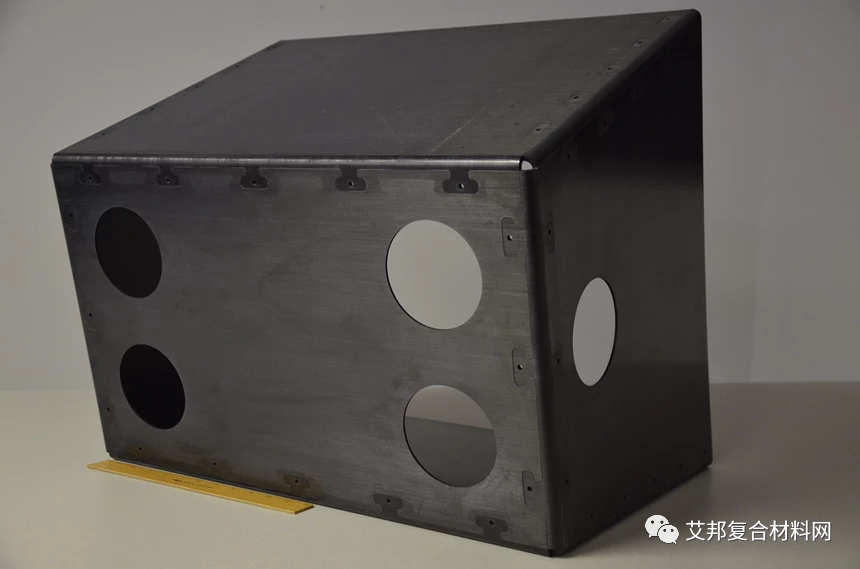
圖 2:可行的工藝:沖壓成型/模壓成型大多數用熱塑性膠帶制成的零件都是使用沖壓成型或壓縮成型制造的,這提供了相對較短的循環時間。此外,熱塑性塑料可以焊接,從而簡化并加快組裝速度。航空航天應用中最常用的熱塑性塑料是 PEEK 和 PEKK。?
資料來源:Tri-Mack 塑料
然而,隨著 20世紀90 年代國防開支的減少,尤其是在美國,人們對熱塑性膠帶的興趣和應用也隨之減少。杜邦(DuPont)、菲利普斯石油(Phillips Petroleum)、埃克森美孚(Exxon Mobil)、巴斯夫(BASF)和帝國化學工業 (ICI) 等曾在熱塑性塑料膠帶開發方面投入巨資的供應商退出了該業務。這并不是說熱塑性塑料膠帶的開發停止了,而是在熱固性復合材料(包括熱固性膠帶)的開發正在加速的時候,熱塑性材料帶的發展明顯放緩。這最終導致后者在波音 787、空客 A350 XWB 和其他商用飛機的大型航空結構中得到應用。快進到 2018 年。商業航空航天界正在展望未來,下一個預計將消耗大量復合材料的大型飛機項目很可能是波音公司的新中型?(MOM-middle of the market) 飛機,旨在取代其 757。波音 737 和空中客車 A320 的重新設計也即將到來,這些窄體飛機是全球商業航空業的支柱。?在 787 和 A350 XWB 上使用復合材料的材料和工藝經濟性與 MOM、737 和 A320 不同。最大的區別是速度。尤其是 737 和 A320,它們是商業航空領域目前最接近商品的產品,這意味著它們的制造速度越快,原始設備制造商的利潤就越高。737 和 A320(以及任何替代它們的機型)的目標產量是每月 60 架或更多,即每天兩架飛機。在熱壓罐中固化的熱固性復合材料目前不太適合這種高容量需求。這就是熱塑性膠帶重返制造業的原因,它們具有熱固性材料無法比擬的循環時間、材料儲存、韌性和可回收性優勢。?如今,它們已被用于制造更小的零件和子結構,包括用于將機身蒙皮連接到桁條和框架的角片和支架。它們被用于小型飛機的許多結構,包括尾翼、機翼和公務機的其他部件。此外,由于熱塑性塑料的韌性和耐腐蝕性,石油和天然氣行業已經接受了熱塑性材料,汽車行業也被其對大批量制造和可回收性的適應性而被吸引。那些在商用機身中使用熱塑性塑料的人面臨的最大問題是,它們在高負載飛機結構中是否可行?熱塑性塑料專家 TenCate Advanced Composites USA Inc.(美國加利福尼亞州摩根希爾)的首席技術官 Scott Unger 在熱塑性塑料領域工作了 30 多年,他說:“熱塑性塑料的增長正處于拐點。擺脫熱壓罐、降低成本和簡化零件組裝的能力是重要的驅動因素。”
就本文而言,熱塑性膠帶由寬度達 12 英寸/305 毫米單向排列的碳纖維絲束組成,預浸有熱塑性樹脂。在航空航天和其他高性能應用中最常用的樹脂是以下高性能熱塑性塑料:聚醚醚酮 (PEEK)、聚醚酮酮 (PEKK)、聚芳醚酮 (PAEK)、聚醚酰亞胺 (PEI) 和聚苯硫醚 (PPS)。一些制造商提供預浸有商品熱塑性樹脂的膠帶,例如聚酰胺 (PA)、聚丙烯 (PP) 等,但這些通常被認為不適用于大型航空結構。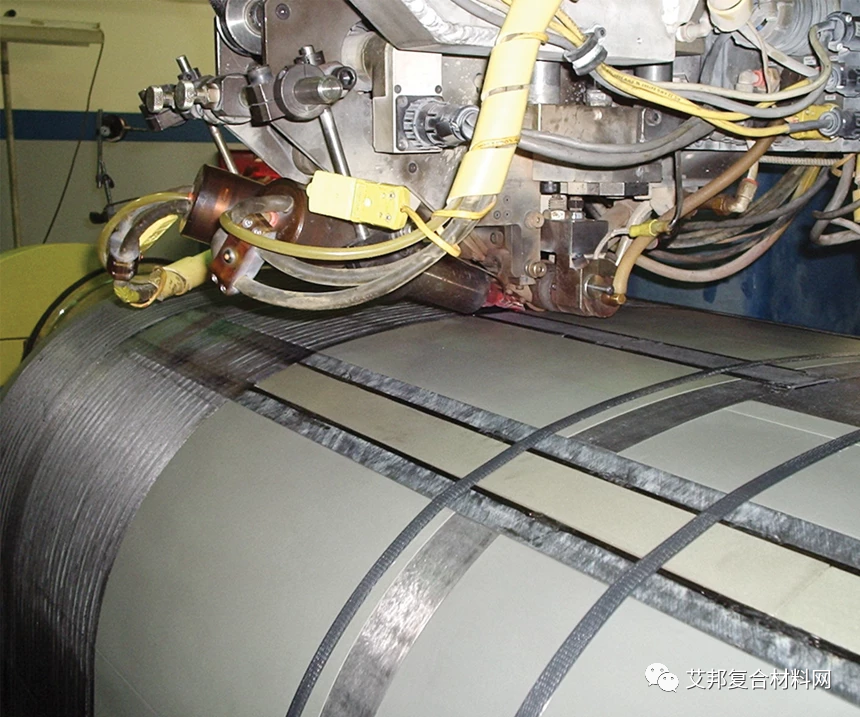
熱塑性膠帶:曾經和未來的航空材料?
此處顯示的熱塑性膠帶在預浸后纏繞在卷軸上,早在20世紀70 年代和 80 年代,就廣泛用于復合材料制造,尤其是軍用飛機應用。但隨后它們的應用停滯延遲了材料的開發,使它們落后于熱固性膠帶。然而,熱塑性塑料的吸引力,特別是對潛在的高壓釜外航空航天應用的吸引力,重新點燃了人們的興趣和產品開發。
資料來源:Barrday Composite Solutions
對于航空航天工業,最有前途的材料是 PEEK 和 PEKK。“總的來說,這兩種聚合物都具有出色的高溫性能、良好的韌性和耐化學溶劑性,以及低吸濕性,”預浸料供應商 Barrday Corp.(美國馬薩諸塞州米爾伯里)熱塑性塑料產品經理 Mike Buck 說。“PEKK 還提供更高的 Tg,以提高耐溫性,并降低了加工的熔體溫度。”航空航天制造商 GKN Aerospace Fokker(荷蘭 Hoogeveen)的研發總監 Arnt Offringa 表示,PEKK 能夠提供與 PEEK 相當的性能,但在較低的熔融溫度下加工,使其成為未來商業機身應用增長的首選。熱塑性樹脂通常通過基于溶劑或基于水的粉末施加到纖維上。使用的預浸料方法會影響纖維的界面特性,水基工藝比溶劑基工藝產生更光滑的表面。大多數熱塑性膠帶的纖維體積分數在 40-60% 之間,航空級材料在 50-60% 范圍內。“如果機械性能是主要關注點,并且生產過程具有較長的循環時間和足夠的壓力和溫度靈活性,那么 60% 的纖維體積很重要,”Buck 說。“更高速度或更低壓力的工藝,如 AFP/ATL、非熱壓罐/烘箱加工等,將受益于更高的樹脂含量。”熱塑性膠帶可以被切割成更窄的膠帶或絲束,也可以像熱固性預浸料一樣被切割成規定的形狀來制作坯料,熱塑性塑料膠帶不像熱固性膠帶那樣有襯紙(背襯)。熱塑性塑料的使用大大改變了制造成品零件的制造步驟。最重要的區別在于,熱塑性塑料本質上在室溫下是固體,必須加熱到熔化溫度才能成型。如前所述,PEKK 的 Tg 高于PEEK(160°C 與 140°C);PEEK 的熔體溫度高于 PEKK(390°C 與 340°C)。Solvay Composite Materials(美國佐治亞州阿爾法利塔)復合材料研究和創新小組技術研究員 Jim Pratte 表示,材料的使用取決于應用,并指出 PEKK 是一種共聚物,可以針對不同的溫度和結晶度進行定制, 而 PEEK 擁有廣泛的數據庫,并且結晶速度更快。這樣的溫度要求立即使這些材料超過固化環氧樹脂或任何其他熱固性材料所需的溫度。如今,用熱塑性塑料帶制造零件最常用的工藝是壓模成形,將膠帶切割成規定的形狀,然后堆疊,再放入預熱爐中軟化和預固結,再將該疊層轉移到成型壓力機,該壓力機通常由匹配的金屬工具組成,可在高壓 (250-500 psi) 下完全固結和冷卻膠帶。“總的來說,我發現與加工熱固性材料相比,熱塑性塑料的加工通常需要'逆向'的思維過程,”Buck 說。“例如,對于熱塑性塑料,通常不想在模具中固化零件,而是形成預熱、預加固的層壓板,然后使用工具冷卻預熱的零件。”原位固結(圖 3)不太常見,且仍在開發中,其中通過自動纖維放置 (AFP) 或自動鋪帶 (ATL) 將切帶(絲束)放置在工具上。在該系統中,帶頭處的高強度激光、熱氣體或火焰將樹脂加熱至熔化溫度以軟化樹脂,同時末端執行器施加壓力以加固層。最終,這樣的系統將在原地進行全面整合,但仍在開發中以供示范。目前,需要進一步固結(高壓滅菌或類似處理)以達到孔隙率目標。
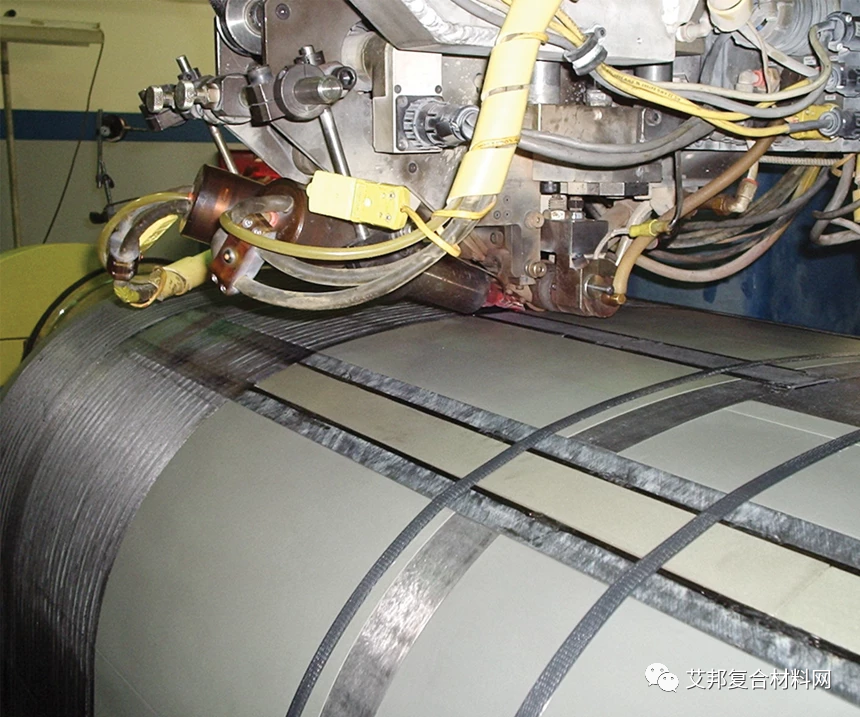
使用熱塑性膠帶的一種有前途的工藝是通過自動膠帶鋪設 (ATL) 或自動纖維鋪放 (AFP) 進行原位固結。在此過程中,預浸漬熱塑性膠帶或絲束在膠帶頭處被加熱至熔點 (>300°C),放置在工具上,然后立即由末端執行器加固。雖然此時需要一個額外的高壓固結步驟來實現孔隙率目標,但最終,該過程有望在一個步驟中提供 100% 的固結。
Porcher Industries(法國 Eclose-Badinières,法國)的全球和國防業務部門負責人 Pierre-Yves Quéfélec 專門從事熱塑性膠帶的 AFP,他說該公司與機械制造商 Coriolis Composites(法國 Queven)合作,目標是孔隙率 <0.5%。“這仍然需要熱壓罐,”他說,“但我們已經開始通過烘箱固化達到這一水平,具體取決于 AFP 的質量。熱塑性塑料的高粘度是一個挑戰,浸漬的均勻性和一致性也是一個挑戰。”雖然目前尚未被廣泛使用,但實現 <0.5% 孔隙率目標的最有前途的工藝可能是連續壓縮成型(CCM-Continuous Compression Molding,見圖 4)。在這里,連續的膠帶通過成型工具,加熱和成型材料,并有效地形成一系列形狀,包括 T、C、H、帽形和歐米茄型材等。該工藝對于商用飛機的縱梁和框架的制造具有特別的前景。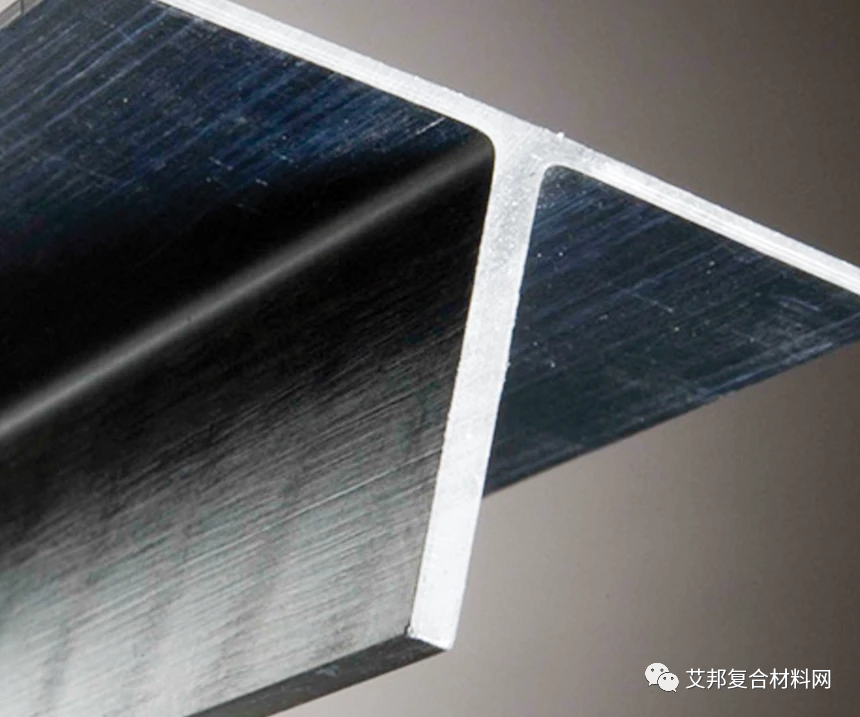
連續壓縮成型 (CCM) 并未廣泛使用,但被認為是一種高度可行的航空結構制造工藝,其中熱塑性帶材連續通過一系列成型工具,以制造復合型材,如圖所示。CCM 被視為制造飛機機身縱梁和框架的理想選擇。?
資料來源:xperion
如前所述,熱壓罐固化是一種選擇,對某些人來說是必要的,以確保最小的孔隙率。Offringa 指出,Fokker 更喜歡熱壓罐,因為它有助于樹脂流經纖維,并有助于保持過程控制和一致的零件質量。在熱壓罐中固化熱塑性部件所需的時間通常為 3-4 小時,明顯少于固化和固化熱固性材料所需的時間。Solvay 的 Pratte 表示,對于目前使用的大多數熱塑性塑料工藝而言,實現孔隙率目標并不困難。“時間和溫度消除了大部分空隙,”他說。唯一困難的過程是原位 ATL/AFP,因為時間尺度——在溫度下施加壓力和鞏固膠帶所花費的時間——是有限的。“這里的關鍵點與其說是孔隙率,不如說是膠帶中聚合物纖維的浸漬。你可能在膠帶中有一些孔隙,但你不能有干纖維,因為原位工藝時間尺度和條件無法彌補這一點。”
一般來說,熱塑性塑料,尤其是 PEEK 和 PEKK,很難讓人不喜歡。如前所述,它們具有與環氧樹脂相似的機械性能特征,但通常比環氧樹脂更堅韌。此外,它們也不會放熱,并且非常耐腐蝕、耐磨和防火。熱塑性塑料還避免了熱固性預浸料的存儲和出庫時間限制——考慮到冷凍機投資的費用,以及管理預浸料有效期以確定何時使用哪卷預浸料的任務,這不是一件小事。事實上,處理/回收過期材料的成本會大大增加使用熱固性預浸料制造零件的成本。此外,由于熱塑性復合材料不會固化和交聯,Buck 指出,“熱塑性復合材料可以重新熔化/重新加工”。這使得它們相對容易回收。索爾維的 Pratte 指出。“回收是汽車行業的一大推動力,因為汽車的回收量要大得多,而且經濟上更具挑戰性,”。“如果你不能回收材料,那將成為采用的障礙。”?盡管這對汽車制造商尤為重要,但隨著飛機原始設備制造商(OEM)也在考慮生命周期管理 (LCM-Lifecycle Managemen) 和產品報廢問題,回收也成為航空復合材料制造中越來越重要的考慮因素。熱塑性塑料還能夠以熱固性材料無法實現的方式實現部件粘合。它們具有將零件焊接/融合在一起的潛力,這可能會在某些應用中消除對粘合劑的需求。”GKN Aerospace Fokker 以使用熱塑性塑料焊接而聞名,Offringa 表示需要開發多種焊接技術,包括電阻焊接、感應焊接和傳導焊接。Porcher 的 Quéfélec 指出 AFP/ATL 是一種連續焊接的形式,據報道,他的許多客戶都希望使用焊接將較小的熱塑性塑料部件連接到較大的結構中。隨著復合材料在航空航天和汽車領域的使用增加,對自動化的需求將會增加。這也是熱塑性膠帶的真正機會。“在我看來,這是熱塑性塑料大放異彩的領域,”Buck說。
盡管熱塑性膠帶具有所有優點,但它缺乏熱固性膠帶的成熟度,因此存在一些挑戰。分切和格式化熱固性和熱塑性膠帶的Web Industries(美國馬薩諸塞州馬爾堡)看到了這些挑戰。Web 的研究和技術總監 Grand Hou 說,熱塑性樹脂由于其韌性,更難切開并滿足公差要求。他說,這種材料也有彈性,因此與熱固性材料相比,它需要不同的纏繞方式和不同的纏繞控制。?Web 業務開發經理 Jim Powers 指出,熱固性膠帶的寬度可達 60 英寸/1,524 毫米,可以無缺陷地延伸數千英尺,而熱塑性膠帶通常最寬為 12 英寸/301毫米,在 700 英尺/17.78米內就有30個缺陷。“熱固性材料經歷了相同的發展曲線,”Hou說。“我們可能比我們意識到的更接近[重大質量改進]。一旦有一個使用熱塑性復合材料的大型項目,你就會看到質量的巨大提高。”樹脂帶來的另一個挑戰是它的應用。熱固性膠帶通常使用薄膜形式的樹脂進行預浸漬,這使得預浸機能夠精確、均勻地涂抹樹脂,厚度變化最小。相比之下,熱塑性塑料依賴于基于粉末的應用工藝,這種工藝更難控制,并且會產生富含樹脂和干燥的區域。這種不均勻性會導致層間孔隙率問題。Web 的 Powers 表示,溶劑型樹脂往往具有更粗糙的表面并產生更多間隙,而水基系統往往更平坦,厚度變化最小且表面更光滑。“較粗糙的溶劑型材料提供更大的表面積,”他指出,“但從纏繞的角度來看,水基系統運行速度更快,并提供更好的材料卷。”另一個變量是,在室溫下,熱塑性膠帶的特點是不尋常的邊界,這會產生一種堅硬的、偶爾不均勻的膠帶,容易產生縫隙和裂縫。膠帶的厚度也會導致材料波紋,這可能會導致膠帶寬度不一致。這會在膠帶分切過程中導致后續問題,這依賴于一致的膠帶寬度以保持在規格范圍內。此外,與熱固性預浸料不同,后者在室溫下具有粘性,有助于在鋪層過程中層與層之間的粘合。而熱塑性塑料是干燥且無粘著性的,需要額外的方法來消除層間滑動,例如點焊。?然而,自動化可能是熱塑性膠帶的粘性不一定是問題的一個領域。Solvay 的 Pratte 說:“人們過去常常抱怨手糊板又硬又板,但在自動化設備中,太硬的板是一種優勢。”?航空航天熱塑性塑料復合材料制造商 ATC Manufacturing(美國愛達荷州波斯特福爾斯)的業務發展總監 David Leach 承認,熱塑性膠帶“通常不如熱固性材料穩定,這當然是我們希望看到改進的領域”。Leach 還指出,不均勻的樹脂應用會產生樹脂豐富的區域,這既有益又有害。他還回應了 Web 的觀點,即熱塑性膠帶中缺陷之間的長度相對較短,并且分切膠帶的寬度不太一致。Leach 說,隨著自動化程度的提高,這種一致性將是強制性的。TenCate 的 Unger 說,高膠帶完整性對于促進熱塑性塑料的使用和彌補制造過程中的限制至關重要。特別是,Unger 指出 AFP/ATL,由于其逐層處理,引入了層間孔隙率的可能性。作為膠帶完整性的證明,Unger 引用了 TenCate 熱塑性膠帶的顯微照片(圖 5),該照片顯示了均勻的層厚度和樹脂均勻性。他說,關鍵是高質量的膠帶,空隙率低,是高質量復合材料快速、自動化加工的推動力。具有大量空隙的膠帶將需要更長的固結周期才能生產出高質量的零件。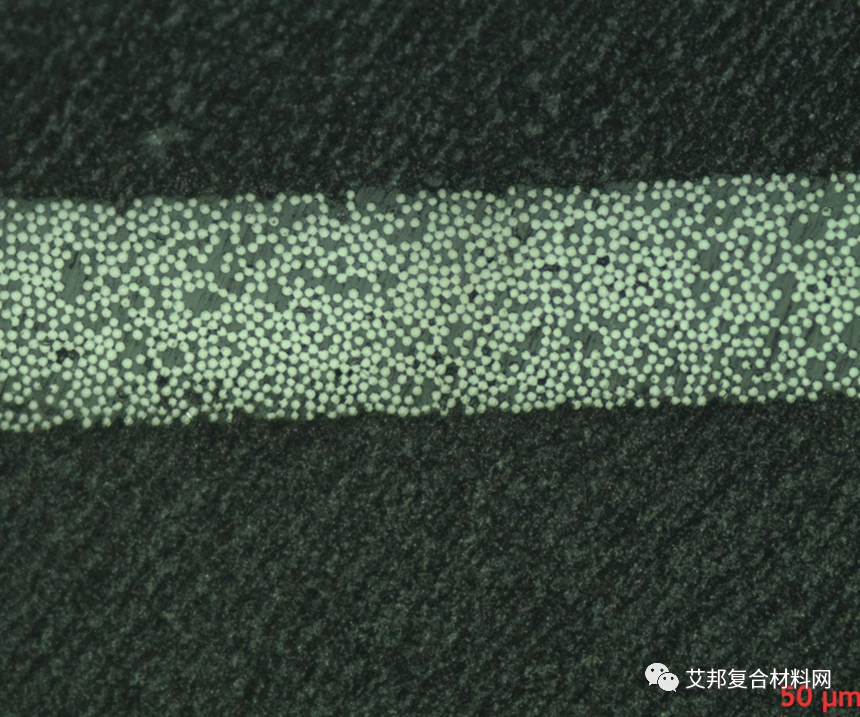
圖 5:加工原則:質量產生質量
這張 TenCate 熱塑性膠帶的顯微照片展示了膠帶產品的均勻性和同質性。膠帶的質量越高,制造商就越容易生產出高質量的零件。然而,使用較低質量的膠帶需要更穩健且可能更耗時的過程才能實現良好的整合。
資料來源:TenCate Advanced Composites
最后,還有成本問題。PEEK 和 PEKK 目前比它們與之競爭的環氧樹脂更貴,但這種情況有望改變。Offringa 說,“如果隨著在高負載主要結構中的應用增加,它像預期的那樣強勁增長,成本預計會隨著體量的增加而下降。” ATC 的 Leach 對此表示贊同,并指出盡管熱塑性膠帶已經使用了幾十年,但體量仍然很小。“原始設備制造商在復合材料方面擁有豐富的經驗,并且傾向于使用膠帶,”他說。“從熱固性材料轉變為熱塑性材料的主要驅動因素是成本。我們怎樣才能讓熱塑性零件變得負擔得起?”Porcher 的 Quéfélec 對此表示贊同。“整個價值鏈……必須重新挑戰商業案例。與熱固性材料相比,高成本會損害競爭力。技術準備水平(TRL-technological readiness level )?落后,但正在迎頭趕上。”Barrday 的 Buck 簡單地說:“熱塑性塑料行業可以使用具有 PEKK/PEEK 性能的聚合物,但價格與 PPS 相當。”
這些真實和潛在的缺陷——缺乏粘性、間隙、波紋、不均勻——造成了下游挑戰,盡管這些缺陷是可以控制的,但使熱塑性膠帶比競爭性替代品更難加工。這反過來又減緩了它們在高性能應用程序中的采用。然而,它們提供的優勢是真實存在的,這刺激了對技術和工藝研發的大量投資,以幫助將這種材料推向更大的結構部件。“在過去二十年里,我們完成了基本的創新,”TenCate 的 Unger 說。“未來的主要創新將是工藝和自動化的成熟以及零件制造基礎設施的擴展。”在制造方面,由 GKN Aerospace Fokker 領導的 Thermoplastic Affordable Primary Aircraft Structure (TAPAS) 財團正在為空客開發熱塑性飛機機身結構和熱塑性扭矩箱(用于尾翼和機翼結構)。正在評估的是一種 TenCate UD 膠帶,它包含 Hexcel(美國康涅狄格州斯坦福德)的 AS4 碳纖維和來自阿科瑪(法國科隆布)的 PEKK 基體。TAPAS 工作分為兩個項目,TAPAS I 和 TAPAS II,后者已接近尾聲。Offringa 說,TAPAS 的工作證明了熱塑性膠帶的潛力,特別是在機身蒙皮、發動機掛架、小型機翼和尾翼結構方面。“材料正在被鑒定,工藝正在被鑒定。這些并不是巨大的零件本身,而是增加尺寸和體積的部件,”他說。展望未來,他說,“其中一家 OEM 可能會取得突破,決定真正轉向更大的熱塑性塑料部件。”索爾維的 Pratte 對此表示贊同:“小零件已經起飛,并建立了信心和成熟度。客戶開始關注更大的零件。”?為推動這一努力,索爾維和 GKN Aerospace Fokker 于 2017 年初宣布,他們將合作開發熱塑性復合材料,而索爾維將成為這家航空航天制造商的首選供應商。Fundacion para la Investigacion, Desarrollo y Applicaciones de Materiales Compuestos(FIDAMC,馬德里,西班牙)也正在評估熱塑性膠帶在制造機翼和機身結構中的應用,通過高壓釜外原位纖維鋪設。FIDAMC 的高級復合材料專家費爾南多·羅德里格斯·倫斯 (Fernando Rodríguez Lence) 表示,膠帶質量是一個主要限制因素,迫使較慢的鋪設速度以彌補膠帶缺陷并實現整合目標:“我相信我們的材料供應商將提高膠帶質量,提高性能以達到熱壓罐固化部件相似水平,并解決后處理的需要。”如果像人們普遍認為的那樣,波音或空客決定使用熱塑性膠帶制造主要結構,則很可能會迅速部署資源來解決膠帶質量問題。事實上,在過去 10 到 15 年中,大部分膠帶的開發都是由材料供應商和制造商發起和資助的。這樣的工作很有希望,但也很有限。OEM 承諾帶來的努力和資金將大大改變熱塑性膠帶的前景。在其歷史上的大部分時間里,熱塑性膠帶中的碳纖維都沒有定型,但隨著預浸料為不同的工藝和應用優化材料,這種情況正在發生變化。熱塑性漿料的設計不僅可以改善纖維處理能力,還可以改善纖維/樹脂的附著力。也就是說,樹脂和纖維的成分和性能范圍很廣,因此,根據纖維、樹脂和應用的組合,上漿選項也有很大差異。此外,一些樹脂與膠劑不相容。在過去四年中,Toho Tenax America(美國田納西州羅克伍德)、SGL 集團(德國威斯巴登)和施膠專家Michelman(美國俄亥俄州辛辛那提)推出了針對某些熱塑性塑料優化的碳纖維漿料。其他預浸料和膠帶供應商也提供熱塑性塑料上漿選項,但沒有透露具體細節。上漿有兩個目的。一是纖維與樹脂的附著力。另一個是當纖維被切割或者通過編織或編織機械時,減少纖維摩擦(減少長絲起毛或磨損/斷裂)。索爾維復合材料公司復合材料研究與創新小組技術研究員(Alpharetta, GA, US) Jim Pratte說,“上漿有時是減少纖維摩擦和破損的必要手段。你們的大部分上漿開發都試圖在性能和‘可運行性’之間找到最佳平衡,即無擴散、斷裂、間隙等。”?預浸料制造商 Barrday Corp.(美國馬薩諸塞州米爾伯里)的熱塑性塑料產品經理 Mike Buck 說:“上漿考慮對于熱塑性預浸料和粉末涂層織物很重要。從歷史上看,未上漿的纖維一直是熱塑性塑料的主要碳纖維形式。然而,碳纖維供應商開始開發和提供熱塑性漿料。”?有人猜測通用熱塑性漿料是可能的,但普遍認為這不太可能:“我認為這是一個夢想,”Pratte 說。“我認為這不會發生。當你觀察聚合物的表面能時,它的范圍太廣,無法被一種上漿類型所適應。”1. ?從原文的敘述中可以看出,從2018年開始,聚醚酮酮(PEKK)迅速進入民機復材行業。先是赫氏(Hexcel)與聚醚酮酮(PEKK)制造商法國阿科瑪(Arkema)戰略聯合,研發最新的熱塑性(TP)UD膠帶。
接著東麗(Toray)于2018年7月收購Cetex公司,將原Cetex公司熱塑性膠帶中的碳纖維改用自己的碳纖維,同時在原牌號前加上“Toray”:Toray?Cetex? TC1000?Premium索爾維(Solvay)原本是一家老牌化學公司,它先前收購了民機復材供應商氰特(Cytec),在這種資源的優勢下,索爾維推出了APC(PEKK-FC)復合材料。2.?赫氏(Hexcel)、東麗(Toray)、索爾維(Solvay)三家供應民機復材的公司,通過不同途徑都及時推出了自己的聚醚酮酮(PEKK)復材帶,這對我國有關行業的發展有著重要啟示。I want to say two words to you: “Thermoplastic tapes”》2018.1.29編譯
https://www.compositesworld.com/articles/i-want-to-say-two-words-to-you-thermoplastic-tapes楊超凡簡介:飛機制造高級專家,近年專攻民機復合材料。原航空工業部首批研究員級高級工程師,享受國務院特殊津貼。
原文始發于微信公眾號(艾邦復合材料網):楊超凡·聚醚酮酮(PEKK)復材的急速發展