復合材料作為高性能結構材料具有輕質高強的優點,可以用于集成和制造大規模的整體組件。隨著制造和加工技術的發展,該類材料的應用逐漸由航空航天領域擴展到其他行業,如汽車、公共交通、生物醫學、海洋、電子和民用基礎設施等。
傳統上,復合材料的成型工藝包括手糊成型、模壓成型、纏繞成型、拉擠成型、熱壓罐成型、樹脂傳遞模塑等。復合材料結構件一直存在的問題是生產效率較低,限制了產量。其原因是成型過程中的手工鋪層過程是勞動密集型工作,需要耗費大量時間和人力成本。另外,通常針對普通熱固性復合材料的熱壓罐工藝需要較長固化和后處理時間 。
在此背景下,研究者們將目光轉向了自動化技術,例如自動鋪帶(Automated tape laying, ATL)技術和 自動鋪絲(Automated fifiber placement, AFP)技術。
自動鋪放技術是實現復合材料原位固結成型的最具前途工藝之一,如今已應用于單向預浸絲束或預浸帶的生產。ATL 通常使用最大304.8mm 的寬預浸帶,而 AFP 使用通常在 6.35~25.4mm 之間的窄預浸帶。從這個意義上講,ATL 在提高材料沉積速率方面更有優勢。然而,AFP 機器通常與可同時處理多束(8~32束)預浸絲束的機頭結合使用,這有效提高了其鋪放效率 。AFP機器能夠根據模具表面的形狀,實現預浸料連續可變角度的放置。此外,還能對絲束進行切割,以適應制造邊界的變化,能夠保證復雜結構的加工要求 。由此 AFP 機器可生產不同形狀的復合材料制件,例如簡單的平面層壓板,彎曲度較小的面板和三維表面,實際示例包括飛機機翼蒙皮、框架、縱梁和機翼盒,機身結構和深潛水器等。
典型的 AFP 工藝過程如圖 1 所示 。將單向預浸帶向下輸送到先前放置的鋪層(基材)的上表面。然后當預浸帶和基材的表面接近咬合點(進入的預浸帶與基材接觸的位置)時,使用熱源對其進行加熱,通過壓緊裝置(通常為壓輥)將熔化的表面相互壓緊,實現粘結 。盡管自動鋪放技術是一種很有前途的技術,但在將其完全商業化之前,仍有許多挑戰需要克服。除了需要實現工業要求的沉積速率與熱壓罐工藝相當的機械性能外,使用半結晶熱塑性塑料時,該工藝還必須達到所需的結晶度,消除或減少可能導致分層的殘余應力,并解決孔隙度高于 1% 閾值的問題。
圖 1 AFP 工藝過程
對于連續纖維增強熱塑性樹脂基復合材料,其增強體通常為碳纖維(CF),碳纖維的質量對連續纖維增強熱塑性樹脂基復合材料的性能有著重要影響。
碳纖維是指含碳量大于 90% 的纖維材料,其中石墨纖維含碳量高達 99% 以上。碳纖維的分子結構屬于亂層石墨結構。碳纖維具有強度高、重量輕、剛度好、導電性好、熱膨脹小、導熱系數高、耐腐蝕等優點,是先進復合材料中增強材料的首選。按照前驅體的不同,可將其分為聚丙烯腈(PAN)基、瀝青基和粘膠基碳纖維。其中 PAN 基碳纖維在目前的生產和應用中占據主要地位。日本東麗公司生產的 PAN 基碳纖維產量和質量處于世界領先水平,其典型產品如 700 級的 T700SC 碳纖維,拉伸強度為 4900MPa,拉伸彈性模量為 230GPa;800 級的 T800H 碳纖維拉伸強度為 5490MPa,拉伸彈性模量為 294GPa。國產碳纖維方面,2015 年前后國內已有多家碳纖維企業的 T800H 級碳纖維的力學性能達到了東麗 T800H 碳纖維的水平。
為滿足航空航天、軍工產業對先進結構材料日益增長的需要,連續纖維增強熱塑性樹脂基復合材料得到了研究者和工業界的廣泛關注。其優勢包括:
(1)剛而韌的線性高分子鏈賦予其優異的抗沖擊性能和抗損傷性能。
(2)使用溫度區間從 -40℃到熔點以下 50℃左右。
(3)復合材料制備過程僅發生物理反應,成型周期短。
(4)可以二次加工,多次成型精確控制尺寸及內部結構。
與傳統的熱固性樹脂基復合材料的區別在于,熱塑性樹脂基復合材料的基體為熱塑性樹脂。高性能熱塑性樹脂的特點是其高玻璃化轉變溫度(Tg),這賦予了它們在較高溫度下仍然具有良好機械性能的特點。聚醚醚酮(Polyether-ether-ketone, PEEK)是一類常用的高性能熱塑性樹脂 ,具有許多優點,如非常高的韌性和耐損傷性、優異的耐環境性、良好的抗蠕變和抗疲勞性,以及非常好的耐磨性。因此,碳纖維和聚醚醚酮基體的組合——碳纖維 / 聚醚醚酮復合材料,被廣泛應用于航空航天工業的高溫應用。如芳香族聚合物復合材料(APC–2)是 Cytec 公司常用的碳纖維 / 聚醚醚酮預浸帶的商品名 。AS4/APC–2被 廣泛使用,而其他APC–2 版本的研究較少,如 IM6/APC–2和 IM7/APC–2,這些帶 /絲束的寬度較窄,為 6.35mm。此外,由TenCate公司制備的 AS4/PEEK 帶也得到了應用。目前,有關自動鋪放的大量工作涉及碳纖維 / 聚醚醚酮預浸帶。
對于連續纖維增強熱塑性樹脂基復合材料,通常在加工過程中需要高溫條件使樹脂熔融,這涉及到熱和應力在界面上的作用。這類材料具有在不需要熱壓罐中固化的情況下就地快速處理的潛力。將連續纖維增強熱塑性樹脂基復合材料的熔融加工與自動鋪放工藝相結合,使得復合材料部件具有在現場粘合成型的可能性。然而,與熱固性樹脂不同的是,熱塑性樹脂在自動鋪放過程中需要進行原位固結。由于以 PEEK為代表的熱塑性樹脂在熔融狀態下具有高黏度,在制造過程中要求高的加工壓力和溫度,使得它們的制造非常昂貴,這是該類材料一個主要的缺點。此外,由于加熱和冷卻速度非常快,壓力施加的時間較之熱壓罐成型非常短,獲得具備與熱壓罐工藝同一水平機械性能的材料是具有挑戰性的。
關于自動鋪放技術的科學研究方面,對 2017—2021 年國內外連續纖維增強熱塑性樹脂基復合材料自動鋪放技術相關研究進行了分類總結,如表 1 所示。
表 1 近年來連續纖維增強熱塑性樹脂基復合材料自動鋪放技術相關研究總結
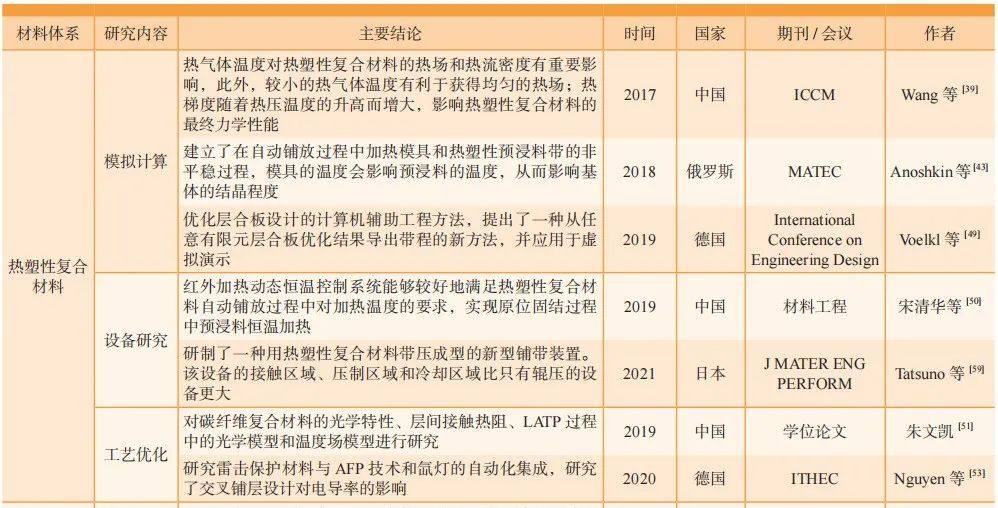
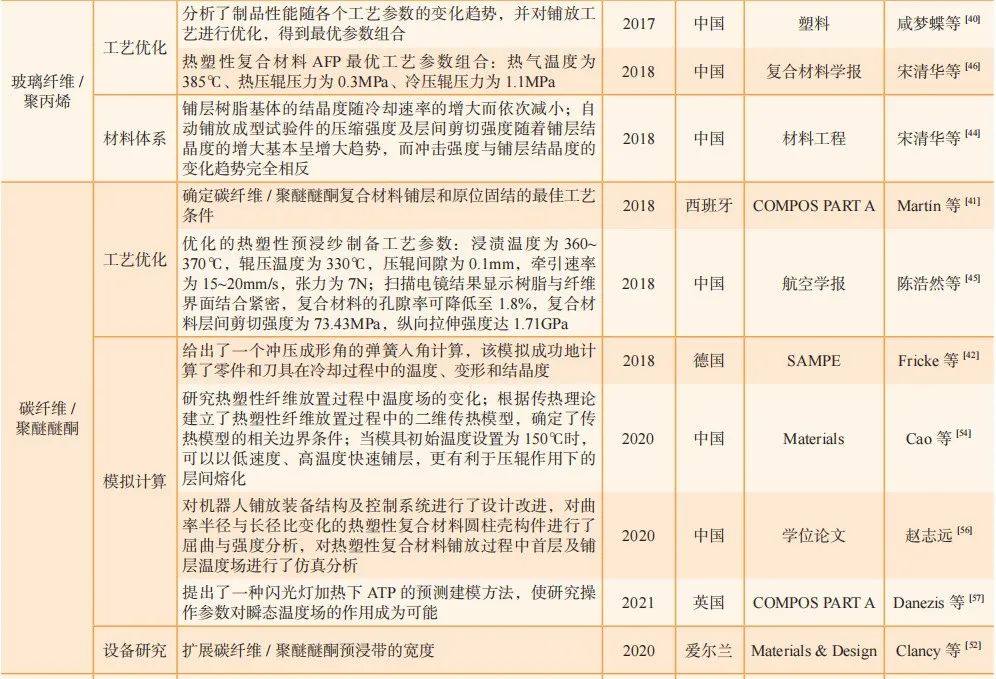


國外方面,相關研究主要集中于德國、英國等,自動鋪放材料體系包括碳纖維 / 尼龍 6、碳纖維 / 聚醚醚酮等,研究重點不僅包括工藝優化,還包括對溫度場等關鍵工藝參數的模擬計算。
國內方面,自動鋪放材料體系包括玻璃纖維 / 聚丙烯、碳纖維 / 聚苯硫醚、碳纖維 / 聚醚醚酮等,研究重點主要為工藝優化和材料體系的研究,模擬計算的相關研究也在近年來不斷出現。
目前國內外高度重視自動鋪放技術的研究工作,從該領域的研究論文上看,國內外形成了各具特色的研究方向。各國研究者都在不斷加大自動鋪放技術的研究力度,力圖提升相應技術水平,保持技術領先優勢,這也帶動了與該領域有關的材料、設備等方面研究的發展。
自動鋪放技術的應用領域方面,國外在熱固性復合材料自動鋪放技術方面的研究已趨成熟,目前正致力于研究熱塑性復合材料自動鋪放技術。美國國防高級研究計劃局(DARPA)30 年前在先進潛水艇復合材料成型方面率先應用熱塑性復合材料自動鋪放技術,并提出該項技術將面臨鋪放成型所需的高質量、低成本預浸料、加工效率及成型構件性能等多方面挑戰。美國 ADC公司、航空主結構熱塑性材料組織(TAPAS)、歐盟“Clean Sky”項目等均開展了針對熱塑性復合材料自動鋪放技術在航空領域應用的相關研究。在 2017 年巴黎航展上,法國“熱塑性弓形盒”項目展出了一個全尺寸熱塑性機身驗證件(圖 2),并針對下一代單通道飛機使用高性能熱塑性復合材料進行內部評估。驗證件具備主要機身結構的所有典型特性,如薄蒙皮、閃電防護、桁條和框結構,因而能夠在真實工業環境下對復合材料制造技術進行詳細評估。其中,機身驗證件蒙皮通過自動鋪放技術制造 。
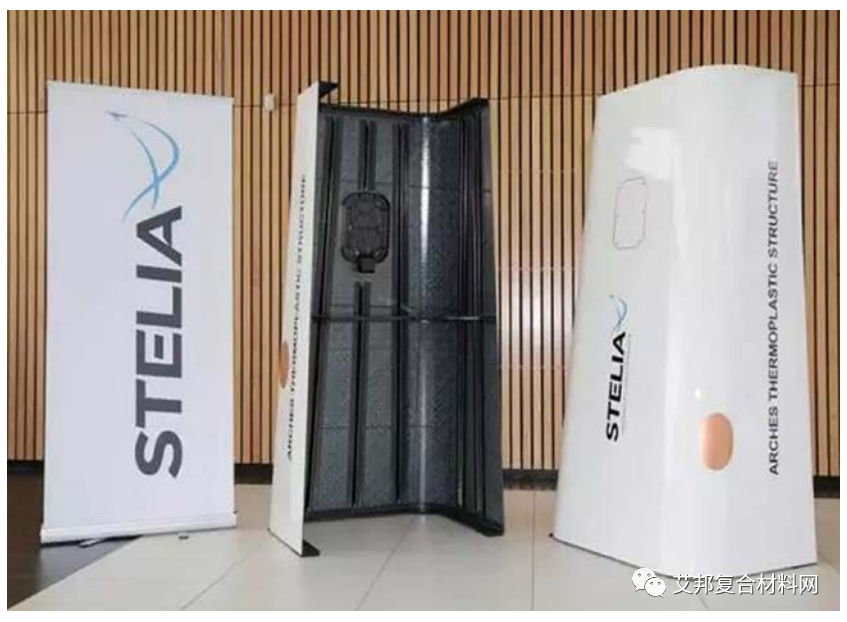
國內在相關制造技術及體系的積累建立方面,與國外存在一定差距。目前國內在制造工藝方面,上海飛機制造有限公司選取機翼典型前緣蒙皮結構,完成了類似金字塔式的工藝關鍵技術攻關。主要研究內容包括大厚度平板試驗件鋪放、前緣蒙皮典型結構鋪放、缺陷可檢性研究(圖 3)。
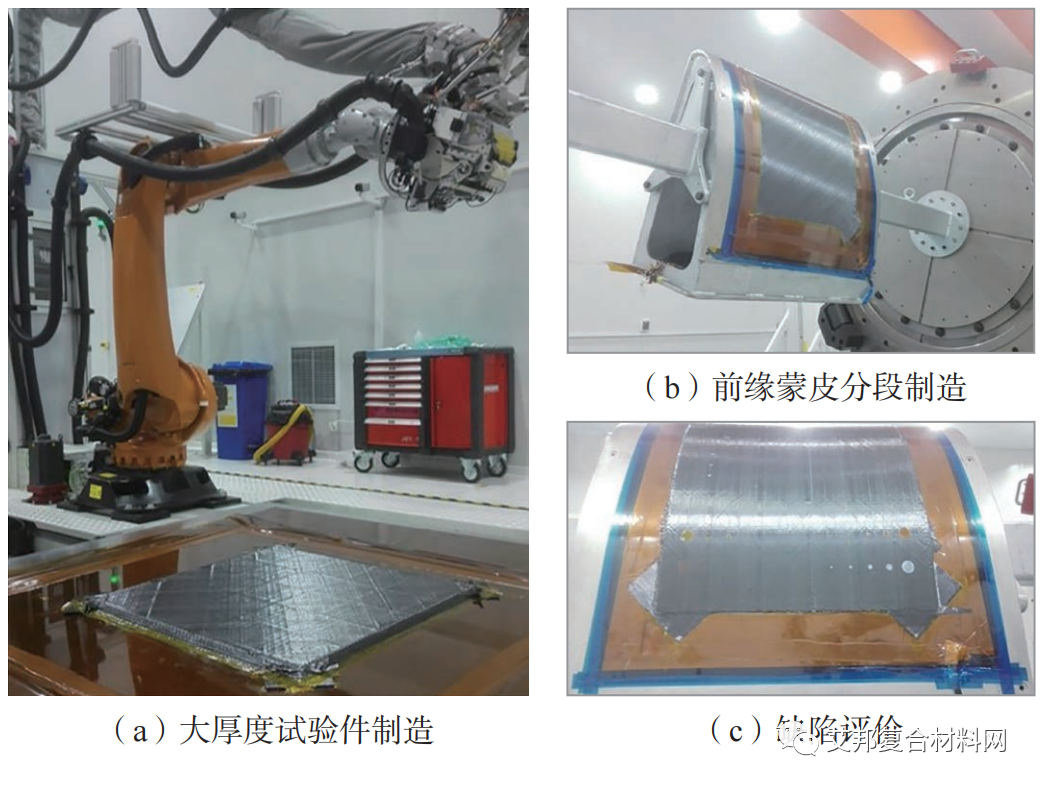
圖 3 連續纖維增強熱塑性復合材料自動鋪放工藝
?
在制造裝備方面,南京航空航天大學在國內率先開展了連續纖維增強熱塑性復合材料熱氣加熱自動鋪放技術及裝備的研究(圖 4(a)),但因該設備熱氣加熱溫度低,只能用于成型中低性能熱塑性復合材料;中國科學院海西研究院在國內率先完成單絲窄帶激光加熱自動鋪放平臺的搭建與調試(圖 4(b)),可開展系列單元技術的模擬與試驗驗證,可進行板材和小曲面樣品的激光加熱自動鋪放成型。
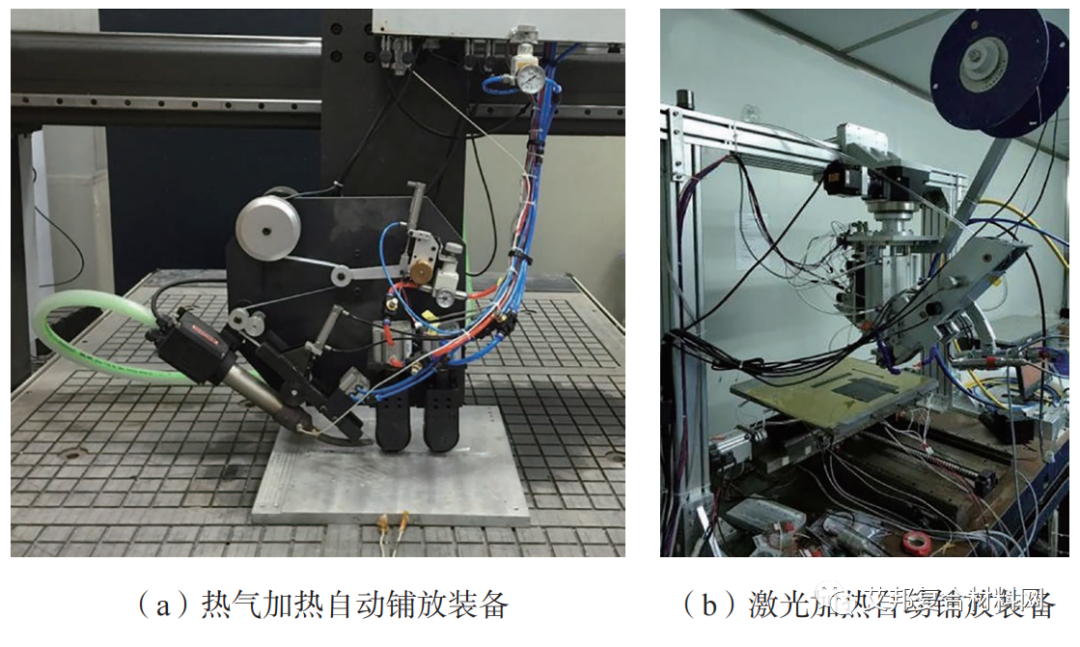
圖 4 熱塑性復合材料自動鋪放裝備
航空工業復合材料技術中心最新引進的法國 Coriolis 公司機器人AFP 設備配有先進的激光加熱系統,最高加熱功率可達 6kW,采用熱成像攝像機溫度檢測儀對加熱溫度的測量范圍為 0~700℃,溫度測量精度可達 0.1℃,可應用于熱塑性復合材料 AFP 工藝研究、熱塑性預浸帶AFP 工藝適應性驗證和熱塑性復合材料自動鋪放成型。
基于連續纖維增強熱塑性樹脂基復合材料的自動鋪放后處理技術
為提高 AFP 加工的 CF/PEEK 復合材料表面質量,Shadmehri 等采用了一種基于 AFP 機器的復合材料表面后處理(Repass)方法,研究了后處理次數對材料表面光潔度的影響,并與熱壓罐成型的復合材料表面情況進行對比。這種后處理指的是在不添加新材料的情況下,通過 AFP 機器頭向層合板施加熱量和壓力。使用表面粗糙度測試儀測量了不同次數后處理和熱壓罐處理的樣品最上層的表面粗糙度。研究結果表明,采用后處理可顯著提高 CF/PEEK 復合材料的表面光潔度。然而,從圖 5(a)中可以看出,與熱壓罐處理的樣品相比,即使經過兩次后處理的樣品也有一個更粗糙的表面。此外,從金相照片(圖 5(b))可以明顯地看出,后處理有效地改變了纖維的分布,使相鄰層的分離線更加清晰可見,更容易區分。
圖 5 使用 AFP 機器后處理前后樣品的表面粗糙度
Chanteli 等研究了激光后處理對 CF/PEEK 復合材料表面質量和力學性能的影響。對于使用自動鋪放技術進行單向鋪層的 CF/PEEK復合材料,在鋪層完成后,使用激光(500W)對復合材料表面進行后處理,同時對比了采用熱壓罐工藝制備的復合材料的對應性能。從表面粗糙度來看,如圖 6 所示,激光后處理降低了 CF/PEEK 復合材料的表面粗糙度,對其在表面光潔度有一定要求的相關領域的應用起到了積極作用。對于不同的后處理次數,一次激光后處理明顯改善了表面質量,兩次處理略微改善了表面質量。另一方面,對不同處理的 CF/PEEK 復合材料層合板的層間剪切強度(ILSS)進行了測試,結果顯示,后處理對 ILSS 值的影響不顯著。圖 6 顯示了自動鋪放制造的層合板的失效模式。具體來說,無后處理樣品顯示出分層,以及纖維破壞和變形,相比之下,所有激光后處理過的試樣均表現出有微小裂紋和小的分層失效。此外,上述試樣的分層破壞主要發生在底層,邊緣出現小裂紋。可見,相對于無后處理層板,后處理使層板脆化。無后處理層板在破壞前表現出明顯的塑性變形,而在后處理試樣中則未出現此類現象。
圖 6 激光后處理前后樣品的表面粗糙度
連續纖維增強熱塑性樹脂基復合材料自誕生之初就引起了航空工業的重視,該類材料優異的綜合性能是其隨后數十年不斷發展和應用的巨大動力。復合材料自動鋪放技術能夠實現機身、機翼等大型結構件的自動鋪疊成型,對于制造效率、精度及穩定性的提升起到積極作用。而當連續纖維增強熱塑性樹脂基復合材料與自動鋪放技術相結合時,可以實現構件在加工過程中的原位成型,不需要再使用熱壓罐,因此縮短了構件的成型周期,提高了生產效率,達到了降本增效的目的。
目前國內該領域的起步較晚,與國外存在一定的技術差距。從未來的發展趨勢來看,以自動鋪放設備一體化技術和連續纖維增強熱塑性樹脂基復合材料自動鋪放后處理技術為代表的相關研究前沿熱點是下一步研究的重要方向。
具體來看,在設備方面,當前需要提升設備的可靠性和一體化程度,未來應加強自動鋪放設備的模塊化設計,提高其對不同種類熱塑性樹脂基復合材料的適應能力。
在材料方面,當前存在的主要問題之一是自動鋪放成型的復合材料表面粗糙起伏、質量不穩定,未來該問題的解決方案,一是提高預浸料樹脂分布及浸漬程度的均勻性,二是開展自動鋪放后處理技術增加材料表面的光潔度。在國內科研團隊的不斷努力下,相信在不遠的將來可以一定程度彌補國內相關領域與國外的差距,滿足科研院所及下游企業的需求。
來源:王凱 , 劉寒松 , 肇研 . 連續纖維增強熱塑性樹脂基復合材料自動鋪放技術研究進展 [J]. 航空制造技術 , 2021, 64(11):41–49
原文始發于微信公眾號(艾邦復合材料網):連續纖維增強熱塑性樹脂基復合材料自動鋪放技術研究進展