01
研究背景
隨著化石燃料的逐漸枯竭和環境污染問題的不斷加劇,純電動汽車因其綠色環保的特性,受到各國的高度重視。近年來,我國也從政策和補貼方面大力推動純電動汽車的發展。電池包作為純電動汽車的核心部件,其質量(包括電池組)一般約占整車質量的30%~40%。對純電動汽車而言,整車質量下降10%,可減少5.5%的電能損耗,同時增加5.5%的續駛里程。
電池包是由電池模組及其外殼組成,它的主要功能是固定、保護和承載電池模組,其殼體約占電池包總質量的20%~30%。由于電芯能量密度的提升緩慢,所以減少電池包箱體質量是提升續駛里程的重要方法之一。
汽車在實際行駛中,會經受顛簸、急轉彎、緊急制動、路面激勵等復雜工況的影響,以此受到的外部沖擊和振動會導致電池包箱體變形過大和應力集中,進而擠壓電池模組引起內部短路、起火和爆炸。
因此,電池包結構和性能的安全性對整車的安全性能有重要影響。在此基礎上的輕量化研究,對純電動汽車未來的發展具有重要意義。
此外,實現輕量化的電動汽車,其續駛里程更長,更受市場歡迎。因此,輕量化的電池包外殼必須具有較高的強度和抗振動性。 02 國內現狀
目前,國內在電池包的結構設計和輕量化方面做了大量研究。華南理工大學陳元設計了一款輕量化電池包,分析了電池包在不同工況下的靜態應力、應變分布,同時開展在低階模態約束下,電池包質量與靜態載荷變形量的雙目標優化,在不降低性能的前提下實現電池包質量減輕29.1%,一階模態頻率由23.60Hz提升至27.60Hz。
湖南大學王品健對某款純電動汽車電池包進行了動靜態特性分析,得到電池包的一階模態頻率24.06Hz,接近路面激振頻率,再采用材料替換、尺寸和拓撲優化等方式對電池包結構進行優化設計,優化后電池包的動靜態性能得到明顯改善,實現質量減輕6.3%,頻率提高至49.37Hz。
侯文彬等以某款電動汽車電池箱為優化對象,通過有限元模擬分析了電池箱在不同工況下的強度和剛度,采用等代設計法進行多工況的整體優化,優化后電池箱質量下降29.9%,強度和剛度得到大幅提升。
馬其華等基于碳纖維復合材料成型和力學替代性要求,設計了一體化車架-電池托盤結構,并對結構進行不同工況下的靜力學分析,又在此基礎上用OptiStruct軟件對結構進行鋪層優化,優化后的結構滿足各工況載荷要求,總質量減輕30%。
湖南大學楊書建基于某企業的一款電池箱結構,采用有限元法對結構進行了靜態、模態和定頻振動特性分析,發現了電池箱強度和剛度的薄弱位置,采用優化設計法對結構進行改進,實現強度和剛度提升的同時,箱體質量減輕7.2%。
東南大學劉元強基于目標車型設計了一款動力電池包,對結構進行了靜力學、自由模態、諧響應以及定頻振動分析,得到電池包的一階固有頻率(58.13Hz)高于路面激勵頻率,最大應力均小于結構屈服強度,滿足極限工況下的使用要求。李垚坤等以某電動汽車電池包為研究對象,采用Abaqus軟件對結構進行了顛簸緊急制動工況下的靜力學特性以及隨機振動分析,基于響應結果對結構進行改進,實現結構強度和剛度提升的同時,電池箱質量減輕48.7%。
合肥工業大學程文文采用熔模鑄造工藝設計鑄造鋁合金一體化電池包,分析了電池包動靜態特性,發現最大應力遠小于屈服強度,存在強度過剩。進行多目標尺寸優化設計,電池包在滿足動靜態特性以及疲勞壽命要求的前提下質量減輕15.05%。 03 輕量化方法 電池包輕量化是在保障其各項服役性能不降低的前提下,合理選用材料和優化結構性能使電池包質量減輕的技術過程。
本文通過總結不同品型電池包在結構設計、箱體材料選用、靜態特性和動態特性4個方面的性能參數,從材料的角度出發,比較滿足4個方面要求的輕量化電池包用材料的服役性能,評估不同材料的輕量化效果,為選用合適的材料用于電池包的輕量化結構設計提供參考。
a. 電池包結構設計分類 ? 在電池箱質量減輕的情況下,電動汽車可多配備同等質量的電池,相應地增加續駛里程。下圖從結構設計總結同品型電池包的質量與體積的關系比較不同品型電池包結構性能。 由圖a可知,鋼鐵材料電池包的質量范圍為11.38~205.90kg,對應體積范圍為0.05~0.71m3;鋁合金電池包質量范圍為3.45~75.90kg,對應積范圍為0.04~0.56m3。可見,在同等質量下,鋁合金電池包的體積更大,有利于空間內電池模組的優化排布;同等體積下,鋁合金電池包的質量更輕,可以多配置同等質量的電池,延長續駛里程。
b. 材料設計分類 ? 目前,高強度鋼、鋁合金、復合材料在電池包箱體的輕量化中扮演重要角色。高強度鋼具有屈服強度和拉伸強度高、抗變形、減震吸能強、焊接工藝成熟等優點,但同時也存在自重過大、耐腐蝕性差等缺點。 ? 鋁合金是一種廣泛應用在汽車領域的輕質材料,其密度只有鋼的1/3,相比于傳統鋼材具有質量輕、可塑性好、比強度高、耐腐蝕、導熱和散熱性好、易回收利用等優點。導熱系數,鋁為237W/(m·K),鐵為80W/(m·K)。電池箱盛裝電池在消耗過程中會散發大量熱量,選用鋁合金作為電池箱材料具有明顯優勢。 ? 復合材料具有密度低、比模量高、抗腐蝕、耐磨損、成型性和沖擊性能好等優點,且質量只有鋼的1/4,但也存在成本高、回收利用率低、散熱性差等缺點,在汽車中的應用僅限于性能車領域。目前,應用鋁合金降低車身質量已成為純電動汽車發展趨勢。圖(b)為不同類別材料與比強度的關系。 由圖可知,電池包箱體用鋁合金材料的比強度均顯著高于箱體用鋼鐵材料。在鋁合金材料中,Al-S-6000的比強度最低,為52.22MPa/(g·cm-3),與鋼鐵材料中比強度最高的B410LA的數值60.51MPa/(g·cm-3)接近,可見鋁合金材料的輕量化優勢顯著。
但是其應用量卻沒有鋼鐵材料廣泛,一個重要的原因是成本效益,鋁合金的成本是鋼鐵材料的2倍左右,對于追求長續駛里程的電動汽車,采用鋁合金電池包是使汽車輕量化以提升續駛里程的重要途徑,但無疑會造成整車成本的增加,所以對于中等續駛里程的汽車通常選用鋼鐵材料作為箱體材料。因此,開展高性能低成本鋁合金研制是未來發展方向。
c. 靜態載荷分布分析 ? 對電池箱進行靜力學分析是為了計算電池箱結構的承載能力,在不同工況下所受應力是否超過材料的屈服極限等。
通過查閱相關文獻可知,緊急制動、急轉彎和顛簸工況對電池箱的沖擊作用較大,電動汽車在緊急制動、急轉彎或經過顛簸路面時,電池模組會因慣性對電池箱產生縱向、側向和地面沖擊載荷,其作用力遠超正常工況,特別是沖擊載荷,遠大于靜態載荷。
因此,在顛簸路面上行駛屬于極限工況。本文總結了兩種工況下最大應力與安全系數、應力集中位置及發生概率的關系。
顛簸路面急轉彎工況:該工況下,顛簸作用的最大應力作用于電池箱底面,急轉彎作用的最大應力作用于電池箱的大側面。圖3a為顛簸急轉彎工況下的最大應力和安全系數的關系。
由圖可知,鋁合金電池包的最大應力主要集中在22.34~140.80MPa之間,小于鋼鐵材料的應力范圍41.62~195.40MPa;鋁合金電池包的安全系數范圍1.58~12.76,大于鋼鐵材料的安全系數范圍1.09~7.33。
組合工況下的安全系數均>1,表明箱體所受應力均低于材料的屈服強度,電池箱箱體沒有發生屈服失效,強度和安全性良好。
由此可知,在該工況下,鋁合金電池包的應力集中小且安全系數高,即服役性能更好。因此,在滿足結構靜態特性的前提下,箱體選用鋁合金材料,可同時實現有效減輕質量和提升安全性能。 圖3b為顛簸急轉彎工況下應力集中位置與發生概率關系。由圖可知,應力主要集中在下箱體。該工況下的最大應力按概率易發生在下箱體吊耳、托架螺栓孔、下箱體底面和下箱體側圍。
這是由于顛簸急轉彎時,箱體里面的電池由于慣性作用向急轉彎和顛簸最大加速度的合成方向運動,兩者加速度的合成方向指向電池包轉彎的大側面,所以電池箱底面偏向大側面受到的力比較大,對應靠近大側面的托架、吊耳受到的力也比較大。
由于吊耳與托架起約束電池包位移的作用,此處的螺栓孔應力集中比較明顯。電池箱直接承載電池的重量,箱體與電池模組支架之間屬于線接觸,所以在箱體底面存在應力集中。
顛簸緊急制動工況:顛簸緊急制動工況下的靜力學分析,如圖4所示,在該工況下,顛簸時的最大應力作用于電池箱底面,緊急制動時的最大應力作用于電池箱的小側面。
圖4a為顛簸緊急制動工況下最大應力與安全系數的關系。由圖可知,鋁合金電池包的最大應力范圍為22.1~142.6MPa,小于鋼鐵材料的應力范圍37.11~185.04MPa。
鋁合金電池包的安全系數范圍為1.71~12.90,高于鋼鐵材料的安全系數范圍1.07~8.22,且同等應力條件下的安全系數是鋼鐵材料的1.2倍左右。同樣,在該工況下,鋁合金電池包的服役性能更好。 圖4b為該工況下應力集中位置與發生概率關系。同樣,應力主要集中在下箱體。最大應力按概率易發生在下箱體吊耳、托架螺紋孔處、下箱體底面以及承受緊急制動產生的沖擊力的小側面。
這是由于緊急制動時,箱體里面的電池因為慣性作用繼續向前運動而對前面的小側面產生了一定的沖擊力,顛簸情況下電池上下振動產生的力作用在電池箱底面,并通過模組支架再傳遞到托架、吊耳上,應力出現在約束箱體位移的吊耳和托架的螺栓孔處。
d. 動態載荷分布 ? 汽車零部件設計時通常都會將一階模態頻率作為一項基本指標,當汽車自身零部件與行駛時路面的激振頻率處于同一區間時,將會極大地降低整車的安全舒適度,同時也會發出共振噪聲。
對電池箱的模態分析可以得到箱體的一階固有頻率和振型,從振型上可以找出箱體結構剛度不足的地方進行優化設計。
查文獻可知,路面引起車身的振動頻率通常在1.32~27.78Hz區間,所以在設計電池箱體時,其一階模態頻率需要高于路面激振頻率,以便有效地減小該頻率區間對箱體的激振。
由圖5a可知,隨著電池包質量的增加,一階模態頻率存在下降的趨勢,所以電池包過重會增加與路面激勵共振的風險。鋁合金電池包的一階模態頻率范圍28.22~102.34Hz,高于鋼鐵材料的一階模態頻率范圍為30.22~58.13Hz。
因此,使用輕量化的鋁合金材料在減輕箱體質量的同時,可提高低階模態頻率,從而有效避免外界激勵,減少電池包的振動損耗。由圖5b可知,振動發生在上箱體的概率是62%,下箱體的概率是26%,箱體側壁的概率是8%。頂蓋部分發生振動彎曲變形的概率較大,容易引發共振,降低電池箱的使用性能和疲勞壽命。
由于上箱體不承重,在滿足輕量化的同時,還要提高其一階模態頻率,因此鋁合金是合適的材料。其次是箱體底面及側壁,出于結構安全性的考慮,在電池包設計時,在這些部位增加加強筋來提升結構的剛度是十分必要的。 04 結果討論 電池包結構輕量化設計多為輕質材料下結構的靜動態特性優化,選用合適的輕量化材料對提升電池包的結構設計技術和輕量化水平具有重要意義和工程應用價值,能夠實現箱體有效地減輕質量和延長整車的續駛里程。
通過總結不同品型電池包在結構設計、材料選用、靜態特性和動態特性4個方面的性能參數,比較了滿足4個方面要求的輕量化電池包用材料的服役性能,評估了不同材料的輕量化效果。主要結論如下:
(1)在同等質量下,鋁合金電池包的體積更大,有利于空間內電池模組的優化排布;同等體積下,鋁合金電池包的質量更輕,可以多配置同等質量的電池,增加續駛里程。
(2)鋼鐵材料用作電池包箱體材料,占據了較大比例。其中,DC01和Q235兩種材料是應用最為廣泛的普通鋼;在鋁合金中,Al6082-T6和Al6061-T6是兩種使用較多的箱體材料,但使用量遠不及鋼鐵材料廣泛,其成本限制了大規模應用。不同系列鋁合金材料的比強度均顯著高于鋼鐵材料,鋁合金的輕量化性能優異。
(3)在顛簸急轉彎和顛簸緊急制動工況下,鋁合金電池包的最大應力范圍均低于鋼鐵材料的應力范圍;鋁合金電池包的安全系數均高于鋼鐵材料范圍。鋁合金電池包的應力集中小且安全系數高,服役性能更好。最大應力主要集中在下箱體吊耳、托架螺栓孔、底面以及側圍。
(4)隨著電池包質量的增加,一階模態頻率存在下降的趨勢,電池包過重會增大與路面激勵共振的風險。鋁合金電池包的一階模態頻率在28.22102.34Hz之間,高于鋼鐵材料的一階模態頻率范圍30.22~58.13Hz,選用鋁合金電池包可在實現輕量化的同時提高低階模態頻率。振型主要集中在上箱體中部、下箱體中部和側圍,所以通過在這些部位增加加強筋來提升結構的剛度十分必要。
(5)鋁合金是安全合適的汽車輕量化材料,可在不降低電池包動靜態特性要求的前提下有效減輕車身質量,延長續駛里程。此外,鋁合金還具有質量/體積值低、比強度高、應力集中小且安全系數高、一階模態頻率高等方面的優勢,但其成本限制了大規模應用。隨著對長續駛純電動汽車需求的增長,發展高性能低成本鋁合金具有廣闊的應用前景。 05 文章來源
李全,王俊升,王兵,劉鑫秀.純電動汽車電池包輕量化設計綜述[J].汽車工程學報,2022,12(04):431-445.
END
原文始發于微信公眾號(鋰電產業通):純電動汽車電池包輕量化設計
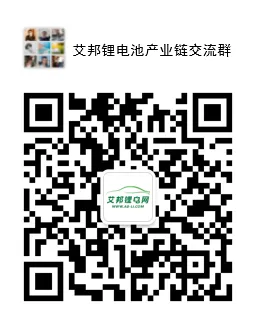