圖1電解水制綠氫
電解槽的每個電解小室分為陽極小室和陰極小室。電解槽的陰極小室產生氫氣,陽極小室產生氧氣。
其主要性能要求包括:制得的氫氣純度高,能耗低,結構簡單,制造維修方便且使用壽命長,材料的利用率高。
電解槽主要部件和材料包括電極、隔膜、絕緣材料和電解液。目前我國電解水制氫設備多運用于光伏、風電等可再生能源制氫,這是主攻方向。
圖2電解槽工作原理
目前在中國,ALK已經完成可商業化,產業鏈較為成熟,PEM目前還處于商業化初期,產業鏈國產化程度不足;SOEC和AEM仍處于研發和示范階段,目前沒有進行商業化應用。
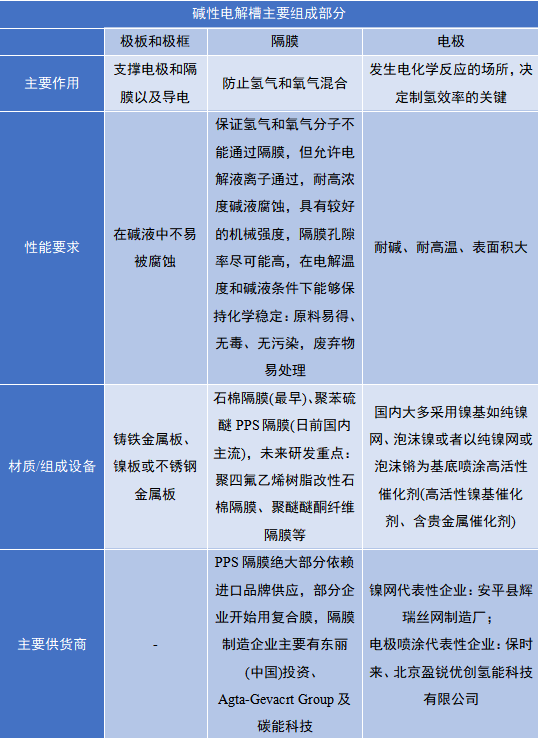
堿性電解水制氫系統主要包括堿性電解槽主體和BOP輔助系統。電解槽主體由端壓板、密封墊、極板、電板、隔膜等零部件組裝而成。
堿性電解技術最大的優勢是陰陽電極板中不含有貴金屬,因此電解槽的成本相對較低。最核心的特點是要求電力穩定可靠,不適合風光等間歇性電能。
商業成熟度高,運行經驗豐富,國內一些關鍵設備主要性能指標均接近于國際先進水平,單槽電解制氫量大,易適用于電網電解制氫。
圖3?堿性電解池
?
電解槽包括數十甚至上百個電解小室,由螺桿和端板把這些電解小室壓在一起形成圓柱狀或正方形,每個電解小室以相鄰的2個極板為分界,包括正負雙極板、陽極電極、隔膜、密封墊圈、陰極電極6個部分。
堿性電解水制氫電解槽主要成本構成為電解電堆組件(45%)和系統輔機(55%);電解槽成本中55%是膜片及膜組件。
1.3.制氫能力越大,設備成本越高
1臺1000Nm3/h電解水制氫裝置的成本是2臺500Nm3/h成本的70-75%,正在研制的更大產量的電解槽會進一步降低投資和運行成本,有利于電解水設備的大規模應用。
針對可再生能源發電的波動性、不穩定性特點,電解水制氫裝置確定設備型號、數量及制氫/供氫的均衡/負荷率,原則上應進行技術與經濟的綜合比較,確定選型、總制氫容量等,然后進行合理配置,具體擬建綠氫系統的總制氫量所用電力應小于可再生能源發電的額定輸出功率。
圖4?堿性電解槽制氫能力與成本的關系
2.1 簡介
PEM電解水制氫系統由PEM電解槽和輔助系統(BOP)組成。
和堿性電解水制氫技術相比,PEM電解水制氫技術具有電流密度大、氫氣純度高、響應速度快等優點,PEM電解水制氨技術工作效率更高。
但由于PEM電解槽需要在強酸性和高氧化性的工作環境下運行,因此設備對于價格昂貴的金屬材料如銥、鉑、鈦等更為依賴,導致成本過高。
目前中國的PEM電解槽發展和國外水平仍然存在一定差距,國內生產的PEM電解槽單槽最大制氫規模大約在260Nm3/h,而國外生產的PEM電解槽單槽最大制氫規??梢赃_到1000Nm3/h,國產大型質子交換膜水電解技術還有很大的進步空間。
圖5 PEM電解槽
2.2 組成
質子交換膜電解槽由質子交換膜、催化劑、氣體擴散層和雙極板等零部件組裝而成,是PEM電解水制氫裝置的核心部分。
電解槽的最基本組成單位是電解池,一個PEM電解槽包含數十甚至上百個電解池。
質子交換膜電解槽成本45%是電解電堆、55%是系統輔機,其中電解電堆成本中53%是雙極板,膜電極成本由金屬Pt、金屬Ir、全氯磺酸膜和制備成本四要素組成。
SOEC電解系統的最基本組成單元是SOEC電解池,多個電解池組裝在一起成為SOEC電堆。多個電堆和氣體處理系統、氣體輸送系統一起可以組合成SOEC電解模塊。高溫固體氧化物電解水制氫技術電解池由電解質、陰極和陽極等核心部分組裝而成。
?
SOEC電解水制氫技術最大的優勢是電耗低,適合產生高溫、高壓蒸汽的光熱發電系統。但由于對陰陽極材料的特性要求較高,使得材料的成本大大增加,因此商業化應用受到限制。
?
高溫固體氧化物電解水技術總體產業化程度不高,推出的商業化產品較少,仍處于研發階段。
?
國外企業主要包括德國Sunfire公司和美國Bloom Energy公司等。國內目前尚處于研發示范階段。
?
由于在運行過程中對于熱能的需求更大,國內外SOEC示范項目主要集中于熱能資源豐富或廢熱較多的地區,如鋼鐵冶煉工廠、化工合成工廠或者核能發電工廠,這些是未來SOEC的主要應用場景。
?
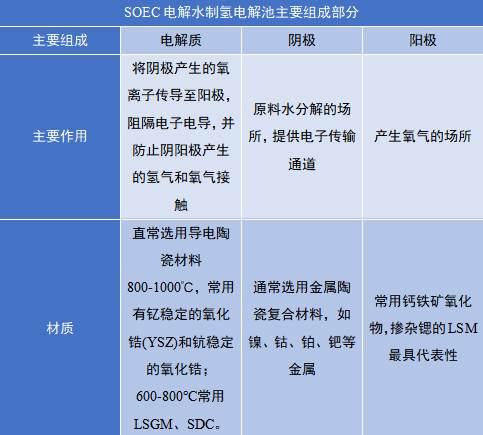
4、固體聚合物陰離子交換膜水電解(AEM)
固體聚合物陰離子交換膜水電解(AEM)是指使用成本較低的陰離子交換膜作為隔膜,低濃度的堿性溶液或純水作為電解液,非貴金屬催化劑作為反應催化劑的制氫過程。
AEM電解池核心構成包括陰極材料、陽極材料和陰離子交換膜。
目前開發的陰離子交換膜仍然無法兼顧工作效率和設備壽命,還未找到最合適的材料,陰極材料主要是鎳,陽極材料主要是鎳鐵合金。
AEM電解水技術是目前較為前沿的電解水技術之一,AEM電解水技術結合了ALK電解水技術和PEM電解水技術的優點,目前處于實驗室研發階段,全世界只有極少數的公司在嘗試將其商業化。
相關閱讀:
三、電解水制氫技術未來展望
隨著電力成本下降、設備投資成本的占比逐漸增加。未來降本驅動因素主要在于,電價降低、設備利用率的增加以及技術進步降低電解槽成本。
但由于堿性電解槽工藝技術已經十分成熟,通過技術革新降低成本幅度不大,PEM存在較大將本空間,未來10年通過技術改進和規模擴張,可以降本40%,制氫成本將下降5%-10%。
隨著產業的進一步發展,未來應用場景將不斷拓寬,大型化、低成本、低能耗是產業發展共識。
需要大規模制氫產能的化工冶金領域將持續采用堿性電解槽制氫,而在分布式能源場景中,如現場制氫加氫站這種氫能產量較小的場景,PEM電解槽將具有獨特優勢。
?
來源:浙理氫能,有刪減
原文始發于微信公眾號(艾邦氫科技網):電解水制氫技術對比
