陶瓷材料具有高強度、高硬度、耐高溫、耐氧化、耐腐蝕、化學性能穩(wěn)定和輕質(低密度)等突出的優(yōu)點,在航空航天、生物醫(yī)療、汽車、電子、能源、國防等諸多領域有著非常廣泛的應用。然而傳統(tǒng)的陶瓷成型技術面臨加工困難(尤其是復雜幾何形狀結構成型更為困難)、制造周期長、生產成本高等不足和局限性,制約陶瓷零件更廣泛的應用。近年來出現(xiàn)的陶瓷3D打印技術為該問題提供了一種全新的解決方案,陶瓷3D打印具有以下顯著優(yōu)勢:(1) 無需原坯和模具,生產周期短,制造成本低;(2) 制造精度高;(3) 可實現(xiàn)幾乎任意形狀復雜結構成型,突破了傳統(tǒng)工藝制造幾何形狀的約束;(4) 適合個性化定制和單件小批量生產;(5) 打印材料種類廣泛,諸如氧化鋯、氧化鋁、磷酸三鈣、碳化硅、碳硅化鈦、陶瓷前驅體、陶瓷基復合材料等。此外,在微小零件3D打印、陶瓷/金屬復合材料和功能梯度材料方面,以及材料-結構-功能一體化打印方面還具有獨特的優(yōu)勢。目前國內外學術界和產業(yè)界已經開發(fā)的陶瓷3D打印工藝有十多種,主要包括:立體光固化成型(SLA)、數(shù)字光處理(DLP)或者面曝光成型、選擇性激光燒結成型、黏結劑噴射成型、陶瓷熔化沉積成型(fused deposition of ceramics, FDC)、疊層實體制造、陶瓷墨水噴射打印成型、陶瓷漿料(擠出)直寫成型等。經過多年的發(fā)展,盡管陶瓷3D打印已經取得巨大的進展和突破,但是現(xiàn)有的各種陶瓷3D打印技術仍然面臨以下挑戰(zhàn)性難題:打印效率低;逐層打印致使成型零件存在各向異性,導致后續(xù)燒結過程中易于出現(xiàn)裂紋、變形等缺陷,嚴重影響打印件的質量、良率和精度。針對傳統(tǒng)陶瓷3D打印存在打印效率低和成型件具有各向異性的不足和局限性,青島理工大學青島市3D打印工程研究中心蘭紅波、張廣明等人提出一種連續(xù)面曝光陶瓷3D打印新工藝,通過采用自主研發(fā)的復合富氧膜并結合配制的樹脂基陶瓷漿料實現(xiàn)陶瓷素坯件的連續(xù)打印。連續(xù)面曝光陶瓷3D打印新工藝,引入一種復合富氧膜并結合特殊配制的樹脂基陶瓷漿料實現(xiàn)陶瓷素坯件的連續(xù)打印,整個打印系統(tǒng)主要包括的功能模塊:數(shù)字光處理模塊、儲料槽、復合富氧膜、陶瓷漿料、成型零件、打印平臺等。圖1 連續(xù)面曝光實驗系統(tǒng)裝置. (a) 連續(xù)面曝光實驗系統(tǒng)裝置; (b) 實驗系統(tǒng)裝置主要結構; (c) 控制模塊; (d) 儲料槽其成型原理圖2所示是利用陶瓷漿料中的丙烯酸光敏樹脂的氧阻聚效應。由于氧阻聚效應,進入儲料槽的氧氣會抑制復合富氧膜頂部一定厚度內的陶瓷漿料的固化反應,從而形成幾十微米的“死區(qū)”(dead zone)。同時,數(shù)字光處理模塊發(fā)出的紫外光能固化“死區(qū)”上方的陶瓷漿料。由于已經固化的陶瓷部件與固定在儲料槽底壁復合富氧膜的離型膜PDMS沒有發(fā)生黏附,所以打印時無需緩慢剝離,從而能實現(xiàn)陶瓷零件的連續(xù)打印成型。復合富氧膜是一種由多孔支撐層和富氧離型層組成的雙層復合薄膜,多孔支撐層采用含有微孔的高透光PET膜,富氧離型層采用二甲基硅氧烷 (PDMS),復合富氧膜不但具有高度透氧和透紫外光的特性,而且具有優(yōu)良的離型(低表面能)、抗拉伸、耐候性等物化性能。圖3 PET膜孔徑大小對成型精度的影響. (a) 不同孔徑下對打印精度影響的示意圖; (b) 不同孔徑下實際成型素坯件.對于相同厚度的離型層,多孔支撐層PET的平均孔徑越大,其透氧量越高,進而導致“死區(qū)”厚度的增加,更多的陶瓷粉使得投影入射光線的散射現(xiàn)象更加嚴重,導致實際固化區(qū)域與理論固化區(qū)域的差值增大,降低了整體的打印精度.平均孔徑為0.22 μm的 PET多孔膜更適合作為復合富氧膜的支撐層,可確保素坯件的整體打印精度.
連續(xù)面曝光陶瓷3D打印的工藝流程較為復雜,涉及的工藝步驟和工序較多,完整工藝流程如圖4所示。首先進行模型缺陷檢查,然后加支撐和模型分層,最后將模型切片數(shù)據編輯成連續(xù)投影圖像傳輸?shù)綌?shù)字光處理模塊;將表面改性后的陶瓷粉和預混液配制成陶瓷漿料(各組分確保均勻混合,避免陶瓷材料團聚、光敏樹脂與陶瓷材料密度不同導致分層);基本流程是Z向工作臺帶動成型平臺浸入到陶瓷漿料中,使成型平臺與成型窗口的復合膜保持設定距離(“死區(qū)”的厚度);Z向工作臺以設定的打印速度(優(yōu)化出的工藝參數(shù))連續(xù)提升,同時數(shù)字光處理模塊連續(xù)播放分層的數(shù)據信息,光源系統(tǒng)產生的紫外光投射到陶瓷漿料上,成型平臺在Z向工作臺的提拉下將已固化部分從漿料中拉起,陶瓷漿料持續(xù)填充已固化區(qū)域,整個過程連續(xù)無間斷,直至整個模型打印完成;從打印平臺取下成型件,將素坯件進行清洗和烘干處理;根據陶瓷漿料組分、固相含量的不同,采用優(yōu)化出的脫脂燒結工藝路線和參數(shù)(燒結溫度、時間曲線),首先脫脂,然后在燒結爐中進行燒結處理,完全去除陶瓷件中的有機成分,獲得最終的陶瓷打印件。其中模型數(shù)據處理和陶瓷漿料配置屬于打印前處理模塊,清洗、脫脂、燒結等屬于打印后處理模塊。研究團隊利用連續(xù)面曝光陶瓷3D打印技術,并結合優(yōu)化工藝參數(shù),打印了鏤空陶瓷件、薄壁陶瓷件。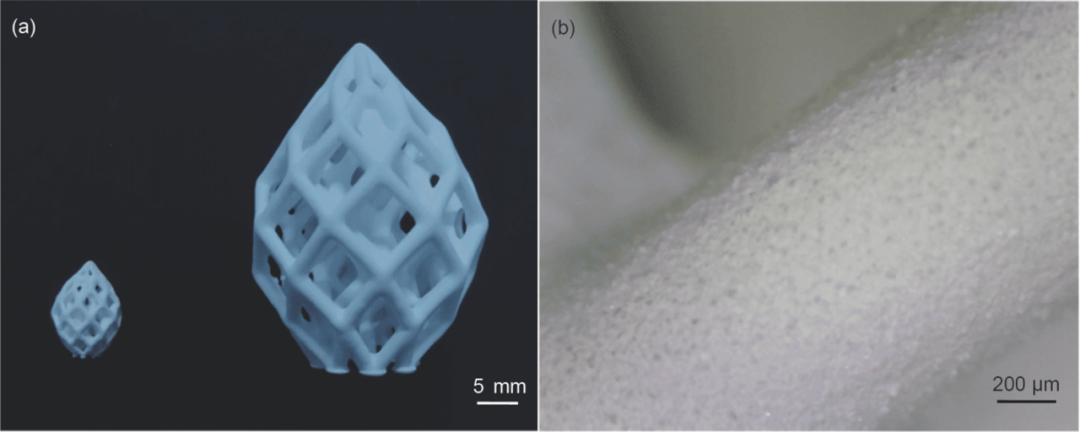
圖5?基于連續(xù)面曝光陶瓷3D打印制造的鏤空陶瓷零件(脫脂燒結后). (a) 兩種不同鏤空零件; (b) 鏤空零件局部放大圖以樹脂基氧化鋯陶瓷漿料作為打印材料,氧化鋯陶瓷漿料固相含量為50 vol%,其中陶瓷粉的平均粒徑為5 μm。成型窗口復合富氧膜的支撐層采用平均孔徑為0.22 μm 且厚度為10 μm的PET微孔膜,離型層為厚度為50 μm 的PDMS。打印速度設為80 mm/h。連續(xù)面曝光陶瓷3D打印制造的素坯件經過脫脂燒結后得到的陶瓷零件如圖5(a)所示。實驗打印結果顯示:制件沒有開裂和裂紋等缺陷,表面質量和尺寸精度高,體積收縮率約為 24%。通過顯微放大圖可以看出表面連續(xù)性較好,即未出現(xiàn)臺階現(xiàn)象,也未出現(xiàn)表面裂紋和較大孔隙。圖6 基于連續(xù)面曝光陶瓷3D打印制造的薄壁零件. (a) 簡單薄壁結構的陶瓷件; (b) 小型葉輪的素坯件和陶瓷件
薄壁陶瓷件的制造是陶瓷3D打印的難點,成型窗口復合富氧膜參數(shù)與鏤空陶瓷件案例相同,采用的氧化鋯陶瓷漿料固相含量為40 vol%,打印速度設為100 mm/h。降低陶瓷漿料的固相含量有助于增加其流動性,提高填充速度。首先打印了一些結構較為簡單的中空薄壁件,并進行了脫脂和燒結,如圖6(a)所示,成型效果較好,未出現(xiàn)瑕疵。在此基礎上又進行了結構較為復雜的小型葉輪的打印,打印的素坯件和脫脂燒結后得到對應陶瓷件,如圖6(b)所示.實驗結果顯示:所制造的陶瓷零件表面質量好,沒有出現(xiàn)開裂和裂紋等缺陷。來源:王赫, 蘭紅波, 錢壘, 等. 連續(xù)面曝光陶瓷3D打印. 中國科學: 技術科學, 2019, 49: 681–689.doi: 10.1360/N092018-00338原文始發(fā)于微信公眾號(陶瓷科技視野):連續(xù)面曝光陶瓷 3D 打印新工藝