↑ 輕量化結構這一趨勢,席卷了物資生產的所有領域。塑料之所以在輕量化領域中占據關鍵地位,這是因為其自身性能,可在相當大程度上降低元件重量。采用諸如發泡注塑這樣的發泡加工工藝,可進一步提升塑料元件的輕量化結構潛能。
發泡注塑系統的主要原理是在塑化過程中,產生最大可能的均質分散聚合物-氣體的解決方案。所有供應商采用的技術雖然基本相似,但在具體實施細節上卻存在差異。
在注塑發泡過程中,氣體和聚合物以一定的比例混合,產品的均勻性主要包括氣體的比例,氣孔的大小分布以及缺陷問題等。因此,保證穩定的氣壓,聚合物的熔融情況等是產品穩定的必要條件。
以Cellmould技術為例:Cellmould技術的獨特之處是其安裝在螺桿上的圓柱形屏障,將塑化區域與充氣區域獨立開來,并且還可以選擇增加套管止回閥。兩部止回閥根據指定運營條件來完美配合、穩定運行。螺桿上塑化和充氣區域之間的屏障有多種型號可供選用,因此磨損可以忽略不計,塑化區域的氣密性也不會降低。
在塑化單元的混合區域,液氮(壓力高達300bar)通過注入端口計量進入塑料熔體。在螺桿的混合區域,熔體流分流成大量獨立的細流,加劇了液氮的分布(見圖1)。在塑化和充氣加工環節中,會有針閥噴嘴保持熔體缸關閉,熔體/氣體混合物在熔體缸內得以維持壓力,因此在混合加工的末端會有段單相聚合物氣體解決方案。由于進入模腔的過程中存在壓力損耗,塑料熔體中氣體的溶解度會被降低。稠密分布的氣體會在熔體中成核,從而形成類似細孔發泡結構的產生條件。
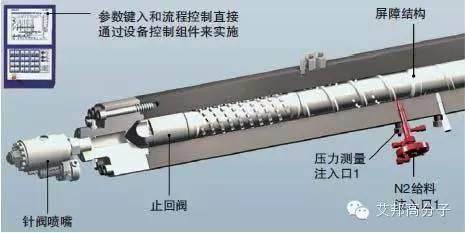
發泡結構品質是否合格,依賴于注塑加工的加工條件,這包括塑料熔體黏度、注入速度(速度越高,發泡質量越高),特別是設定的發泡率(材料減少量)。后者通過相應的下部給料進入安裝好的模腔來設定,或者通過完全填充模腔,隨后模腔通過預先設定的精準行程打開。注入增壓器是Cellmould組件中不可或缺的一部分(見圖2),用以達到均質發泡分布所需要的高注入速度。
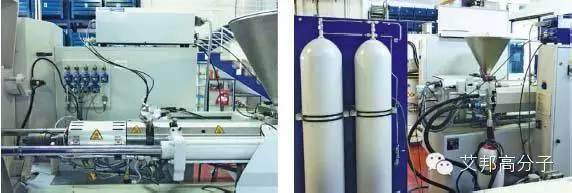
惰性氣體可由增壓器提供,或者由氮氣發生器抽取環境空氣產生。不論用何種方式,氣體隨后都會通過壓力發生器進入氣體注入端口,按照設計,一部供氣組件可同時供給若干設備(見圖3)。在供壓組件和塑化缸的氣體注入端口之間有氣體控制模塊,整合的閥門系統和相關的氣流率都可通過Cellmould加工處理軟件加以操控。相應的設備亦可適用于整個Wittmann Battenfeld設備系列。
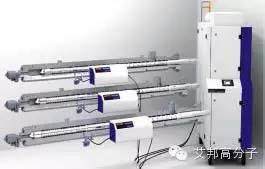
二、高壓發泡注塑及其優勢
當注入模腔內時,由于塑料熔體逐漸接觸冷卻模腔表面,會即時增加黏度,因而熔體外表面的發泡會受到相當大程度的抑制,反之亦然,較熱的內芯區域利于發泡結構的形成。由此產生出由高密度外層和內芯組成的三明治結構元件,其內芯比重比外層低5到20%。
對于所有傳統塑料級而言,元件密度的降低量與流道/壁厚比率成正比。以PP加工為例,比率為100:1時,密度降低15%,而當比率150:1時,密度可能降低10%。回復“PP”查看更多
高壓發泡除了可以加快速度,減少發泡注塑周期時間;還可以最大限度的減小塑料制品外層低發泡的厚度。這樣,既增加了機器的生產效率,又能減少每件制品的原料用量!
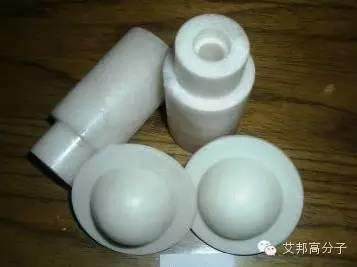
除了可減少重量,高壓發泡注塑還有助于提升元件質量;特別是均質發泡內芯的膨脹壓力,會補償收縮和翹曲現象。效果良好的情況下,幾乎可完全避免下陷和收縮翹曲的出現,這往往也提升了尺寸穩定性。對于加工商,這更是提供了切實的加工工程優勢,例如降低了所需合模力(減少量高達50%),熔體黏度的下降而引致的注入壓力隨之也降低,元件重量的下降,縮短了生產周期時長,特別是冷卻時間,這無疑提高了生產的經濟收益。
除了依賴注入加工參數的變化,發泡輕量化元件還可顯現出獨有的紋理和霧化表面。表面效果的產生主要是由于在注入過程中,氣泡向前推出熔體流,接觸時產生的結構被凝結并存留下來。
通過標準技術往往無法獲得光澤表面,例如,那些用于外殼產品的可見元件。通過將發泡注塑和循環動態模溫控制結合在一起,元件表面質量可獲得大幅度改良提升。”
這些是元件可見表面的共形變體冷卻與注塑和循環熱/冷溫控組件的整合。只有靠近型腔的有限模具區域會被控制溫度。在氣化熔體的注入之前直接加熱,如以加壓水加熱到180℃,由于材料沒有立即與冷模具壁相接觸,從而可形成沒有凝結氣泡的連續平滑面層(見圖4)。
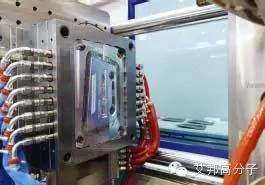
用這種方式生產出的元件表面質量,可與無泡塑料元件相媲美。通過對比采用模溫控制和沒有模溫控制生產出的元件,可看出效果對表面質量的影響(見圖5)。
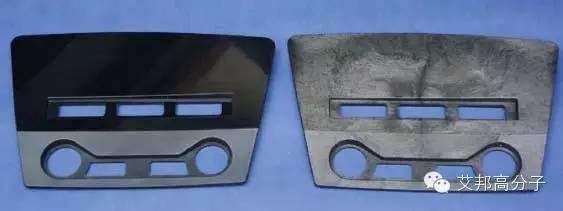
目前的研發課題包括將發泡注塑的適用范圍拓展到熱塑性彈性體。采用聚丙烯和聚酰胺材質,通過化學和物理發泡都可以獲得優質的發泡結構,我們的測試系列顯示,大多數TPE級只能夠采用物理方法來發泡。并且在這其中,只有基于熱塑性聚酯TPE,能夠獲得優質氣泡結構和均質性。
TPE的質地越柔軟,發泡過程中的表面問題就越明顯,特別是如果發泡注塑結合精準注塑模具開模。尤其是當模腔已經被刷亮,或者甚至更進一步拋光過,元件表面經常會呈現出不計其數的凹痕。
關于這種現象的解釋有很多,可能是當填充的時候,空氣滯留在制模和型腔表面之間,流不出去;又可能是因為發生粘黏,當精準開模和膨脹發泡部分圍住了逐點的空氣,當它被再次定位在型腔中,便導致了凹陷。
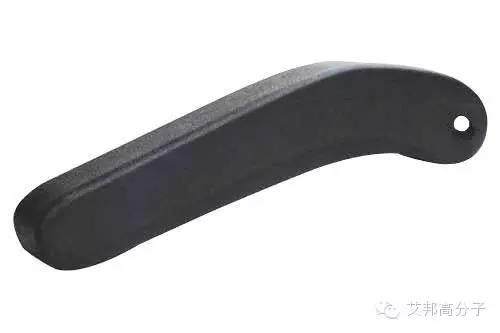
一系列實驗顯示出,TPE并不像那些堅硬的和固體工程熱塑性塑料,TPE可通過媒介來降低注入速度,從而避免加工的表面問題。型腔表面的結構化也能起到類似的積極影響,例如通過電子放電加工而將表面變得粗糙,采用玻璃球爆破或者起紋,通過注塑元件和型腔表面之間的接觸面上的微型管道來幫助滯留氣體或空氣逃離。
工程塑料的發泡注塑的表面條紋分布問題,也是同樣的思路。這里的解決方案也是:表面的動態共形溫度控制,如果精準開啟同時使用,便可獲得高品質而成本低廉的軟泡沫,例如可用于汽車制造中的扶手,或者作為減震裝置用于便攜式終端產品,可在墜落的情況下保護產品不被損壞。
在輕量化結構用途的增長趨勢下,發泡注塑已經進入到了全新的繁榮發展時期。最近的創新成果包括提升表面質量到高光澤度的加工方法,以及結合無泡和發泡部分于同一元件的生產工藝。其中最重要的成果,是基于加工工藝和模具工程學的發展,從動態模溫控制到單個或多步驟精準開啟整個模具或部分型腔。
實用的模擬模型為元件產品設計師給予了有力幫助。總體而言,發泡注塑的發展成熟度已然接近于傳統注塑,其特有的輕量化和三明治結構,可在生產中進行精密準確的再復制,并可持續拓寬涵蓋熱塑性彈性體在內的適用材質范圍。我們相信,發泡注塑2.0將會再一次改變我們的生活!
加入艾邦高分子微信群,請加微信:18681464439或13058121209
推薦閱讀:
閱讀原文申請加入我們
↓↓↓
始發于微信公眾號:艾邦高分子