
歐洲汽車制造商廠在加速普及CFRP(碳纖維復(fù)合材料)量產(chǎn)車。BMW在2013年發(fā)售的i3和2014年發(fā)售的i8,首次在量產(chǎn)車上使用了CFRP單殼體車身,而且在2016年上市的主打車型寶馬7系的基礎(chǔ)骨架上,不僅采用了鋁合金,還采用了CFRP。梅賽德斯奔馳、奧迪也將之作為今后輕量化技術(shù)的主要材料,面向量產(chǎn)車進(jìn)行了研發(fā)。
?

BMW i系列的CFRP單殼體車身
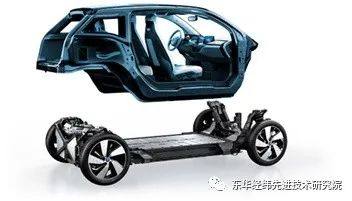
圖1?BMW i3車身構(gòu)造
上部:CFRP制活動(dòng)模塊
下部:鋁制驅(qū)動(dòng)模塊
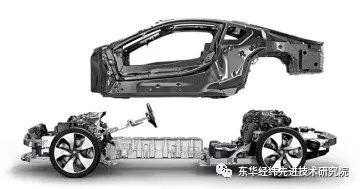
圖2?BMW i8車身構(gòu)造
上部:CFRP制活動(dòng)模塊
下部:鋁制驅(qū)動(dòng)模塊
在BMW i3的車身構(gòu)造中,駕駛艙部分的活動(dòng)模塊為CFRP制的單殼體構(gòu)造。另一個(gè)包含動(dòng)力總成、底盤、電池的驅(qū)動(dòng)模塊為鋁制,這2個(gè)模塊結(jié)合構(gòu)成了革命性的新型車身構(gòu)造。
碳纖維的素材由三菱Rayon生產(chǎn)。BMW于2013年發(fā)售i3后,截止到2015年5月的1年半時(shí)間,銷售了16000輛。在此之前,只有超跑將CFRP用于車架骨格構(gòu)造部位,像BMW i3這樣在量產(chǎn)車上大量使用CFRP是劃時(shí)代的。
該車身構(gòu)造的材料明細(xì)如圖所示,碳纖維強(qiáng)化塑料為68.5kg占全體的一半,再加上熱塑性樹脂13.3kg、粘著劑、填充材料等19.5kg,總重量不到101.3kg,構(gòu)成了駕駛艙的CFRP制單殼體結(jié)構(gòu)部分。
剩余36.8kg集中于下層的驅(qū)動(dòng)模塊除底盤、動(dòng)力總成、電池以外的車身構(gòu)造部分。下層部分的明細(xì)為鋁板15.9kg、鋁擠出材5.4kg、鋁鍛造材5.4kg、鋼材10.1kg,共計(jì)36.8kg。
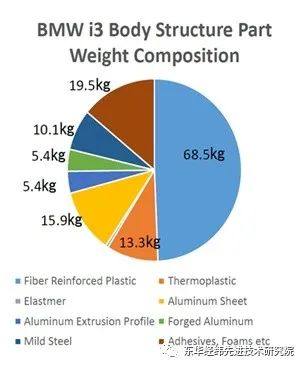
圖3 BMW i3車體結(jié)構(gòu)重量組成

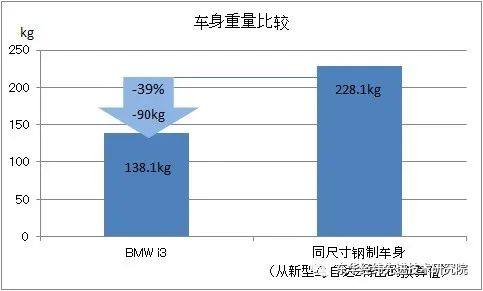
圖4 BMW i3 活動(dòng)模塊
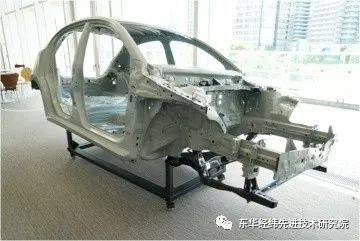
圖5 Mazda2車身
為了比較BMW i3的車身重量,在這里用Mazda 2的車身作為參照。Mazda 2是沒有使用鋁及CFRP等新材料,而只使用鋼材來考慮如何徹底進(jìn)行輕量化從而開發(fā)出的一款具有出眾輕型車身的車型。增加了超高張力鋼板、高張力鋼板,并且分析了高張力鋼板的薄板特性,為了使薄板化也能保持強(qiáng)度而在表面形狀上下了功夫,比之前車型減重10.2kg。考慮到車輛尺寸及配置提升所增加的25.4kg,所以實(shí)際實(shí)現(xiàn)了35.6kg的輕量化。車輛性能的評(píng)價(jià)也很高,十分適合作為比較對(duì)象。比較車輛尺寸兩者長(zhǎng)度幾乎相同,對(duì)車重影響較大的軸距尺寸一致。但是,由于在車寬和車高方面BMW i3略大,因此為了使Mazda 2在車輛尺寸方面在比較時(shí)與BMW i3處于相同條件,加上了相當(dāng)于長(zhǎng) x 寬 x 高的差值重量后的總重量為228.1kg。
與此相對(duì),BMW i3的車身重量為138.1kg。這與以Mazda 2為基礎(chǔ)計(jì)算的鋼制同尺寸的車輛相比減輕了39%的90kg。這與集結(jié)了Mazda 2的最新技術(shù)的鋼材所進(jìn)行輕量化開發(fā)的結(jié)果35.6kg相比,采用CFRP和鋁合金作為主體的車身構(gòu)造的輕量化效果顯而易見。
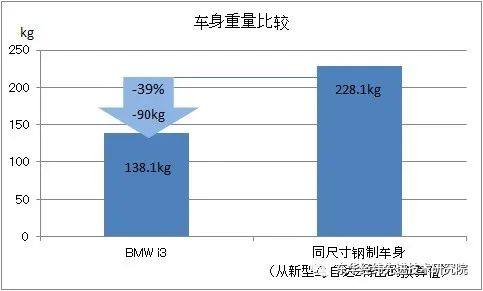
圖6?BMW i3車身重量的鋼材車身比較
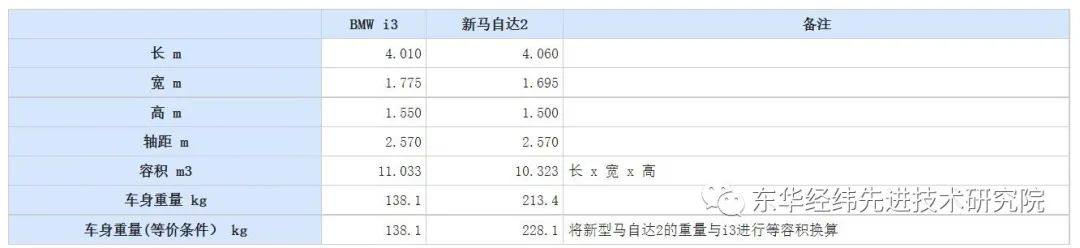
表1?BMW i3車身重量與鋼材車身的比

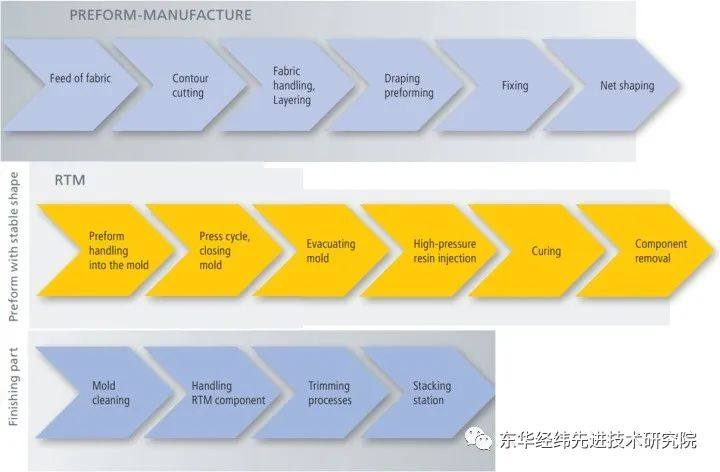
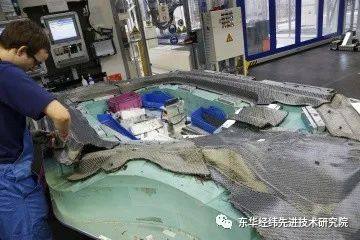
圖7?BMW i3 CFRP材料的制作過程
此次,能成功將CFRP用于BMW i3量產(chǎn)車上的最大的原因是生產(chǎn)技術(shù)。以往的超跑上所使用的高溫法1次成型需要數(shù)小時(shí)。BMW i3的駕駛艙部分的CFRP活動(dòng)模塊所使用的高壓樹脂傳遞模塑(RTM)法可將時(shí)間縮短到數(shù)分鐘。RTM是將纖維方向不同的碳纖維積層板所重疊成的“堆棧",按產(chǎn)品形狀進(jìn)行切割,將這個(gè)堆棧加熱從而做出穩(wěn)定的立體形狀。把預(yù)成型的“毛坯”安裝在磨具上,在其中注入高壓樹脂、使纖維和樹脂相結(jié)合。在加熱的同時(shí)進(jìn)行沖壓使之硬化,從而做出高剛度的制品。
BMW i3的CFRP復(fù)合零件,由許多個(gè)CFRP部材相粘合,從而構(gòu)成駕駛艙部分的活動(dòng)模塊的單殼體構(gòu)造。通過100%自動(dòng)化的最新粘合技術(shù),能準(zhǔn)確的粘合各個(gè)零件粘合面的間隙,通過追加熱處理縮短了硬化時(shí)間。BMW i3的粘合面的總長(zhǎng)度為每1臺(tái)寬20mm,長(zhǎng)達(dá)160m。

BMW i3的CFRP零件的生產(chǎn)工序除了導(dǎo)入了德國(guó)大型成型機(jī)廠家Dieffenbacher和KraussMaffei之外,還引進(jìn)了Fraunhofer ICT的研究機(jī)構(gòu)進(jìn)行技術(shù)合作并聯(lián)合開發(fā)的最新設(shè)備。此次i3駕駛艙周圍的CFRP車身骨架部分是通過樹脂注入成型(RTM)法的熱硬化成型件,最新的RTM法有著許多改進(jìn),變化也日新月異。BMW i3采用了以下3種成型法。
HP-RTM成型(High-Pressure Resin Transfer Molding)
此次的i3有13個(gè)零件是通過HP-RTM做成的。
其生產(chǎn)工序是:將由CFRP編成的編織物材料卷曲材中切出,進(jìn)行沖壓成型的預(yù)處理(原材料)。將原材料放入RTM成型機(jī)中,進(jìn)行真空處理后,用高壓將樹脂射出,在模具中進(jìn)行熱硬化,最后切下制品。
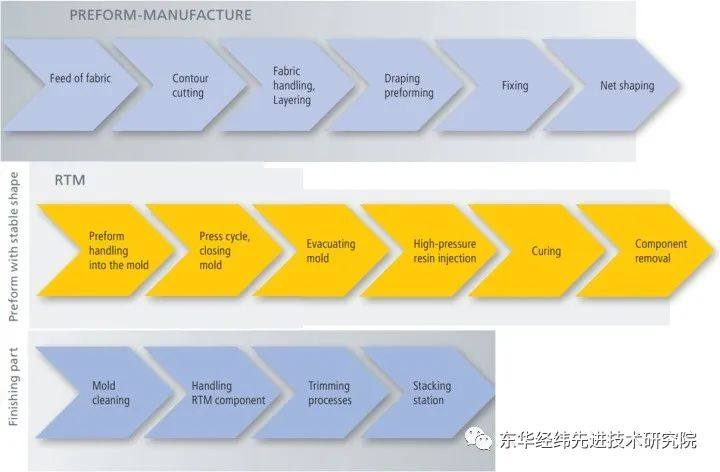
圖8?HP-RTM成型過程
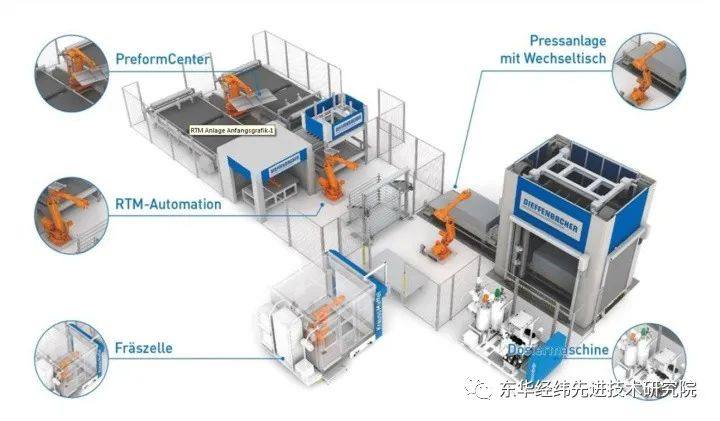
圖9 HP-RTM成型設(shè)備
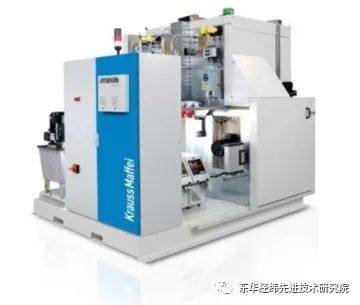
圖10?德國(guó)KrussMaffei公司HP-RTM樹脂注入機(jī)
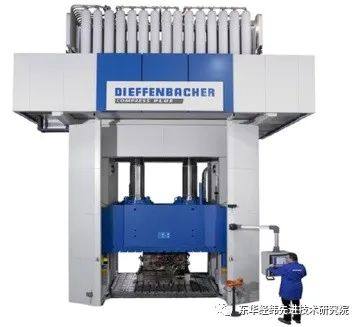
圖11?德國(guó)Dieffenhbacher公司的高性能熱壓機(jī)
濕法成型(Wet Molding)
此次i3有19個(gè)零件采用Wet Molding制成。濕法成型作為HP-RTM的發(fā)展形,可縮短循環(huán)時(shí)間。
工序上,到切出卷材這一步為止是一樣的,將樹脂注入的工序提前到模具安裝之前進(jìn)行。把CFRP材料里注入了樹脂的編織物移動(dòng)到RTM加工中心,將模具密閉加壓使樹脂滲透在纖維里面,進(jìn)行熱硬化。也可使用再生纖維薄板。
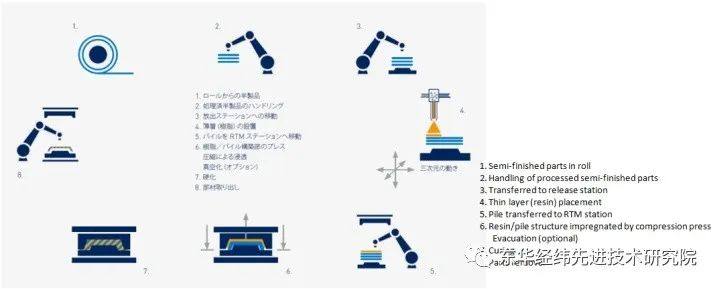
圖12 濕法(Wet Molding?)成型過程
HP-RTM Braided/W Core成型
此次i3有2個(gè)零件采用HP-RTM Braided/W Core制成。
HP-RTM Braided像編加入了纖維的橡膠管那樣,在圓周上加入碳纖維后編成管狀后,通過RTM成型射出樹脂進(jìn)行熱硬化,是管狀CFRP制品的成型方法。適用于管狀的骨架和加強(qiáng)筋。

德國(guó)Dieffenbacher公司從樹脂注入成型(RTM) 開始,還開發(fā)了其他各種各樣的成型技術(shù),如圖所示還和其他公司共同進(jìn)行研究開發(fā)。
第一個(gè)是樹脂注入成型(RTM),如前所述,正在開發(fā)從HP-RTM延展的濕法成型技術(shù)。
第二個(gè)是SMC(Sheet Molding Compound), 將包含不連續(xù)的碳纖維等材料的板狀熱硬化性樹脂放入模具中進(jìn)行沖壓成型、熱硬化的方法。與之對(duì)應(yīng)的最新技術(shù),為降低成本及提升品質(zhì)在直接將材料投入相同生產(chǎn)線的成型機(jī)內(nèi),制作板狀素材的D-SMC正在開發(fā)中。
第三個(gè)是LFT-D(Long Fiber Thermoplastics Direct process), 使用長(zhǎng)纖維復(fù)合材料的熱可塑性樹脂成型。與之對(duì)應(yīng)的最新技術(shù)是將追加的強(qiáng)化材料同時(shí)成型的Tailored LFT-D正在開發(fā)中。
第四個(gè)是GMT(Glass Mat Re inforced Thermoplastics),將玻璃纖維的不織墊在可塑樹脂內(nèi)浸潤(rùn)成型的方法。與之對(duì)應(yīng)的最新技術(shù),正在向在以往的玻璃纖維上疊加碳纖維強(qiáng)化材料進(jìn)行成型的LWRT ( Lightweight Reinforced Thermoplastics)技術(shù)方向發(fā)展。
無論哪種技術(shù)的開發(fā),都是與Fraunhofer ICT共同開發(fā)的,說Fraunhofer?ICT的存在是不可或缺的也不為過。
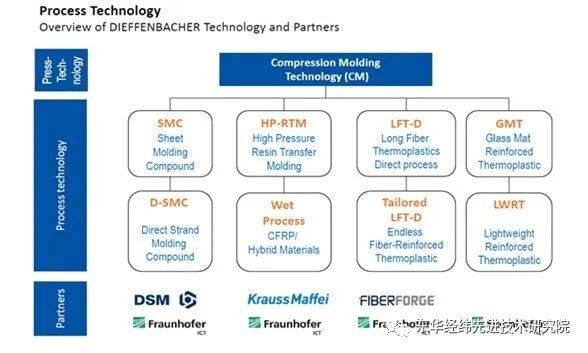
圖13?歐洲輕量化成型技術(shù)的趨勢(shì)

SMC產(chǎn)品的表面處理十分優(yōu)秀,十分適合用作汽車的外板。Dieffenbacher公司2012年與Fraunhofer公司共同開發(fā)了作為SMC成型最新技術(shù)的D-SMC生產(chǎn)線。D-SMC在即將進(jìn)行沖壓成型工序之前,通過調(diào)配熱硬化性樹脂復(fù)合材料,實(shí)現(xiàn)了SMC成型的成本降低和品質(zhì)管理的提升。要求輕量化及高強(qiáng)度時(shí)包含碳纖維,一般的外飾配件不使用碳纖維的例子也很多,有著種類繁多的產(chǎn)品。
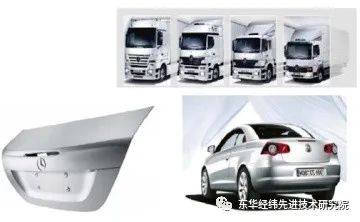
圖14?采用SMC/ D-SMC技術(shù)的例子
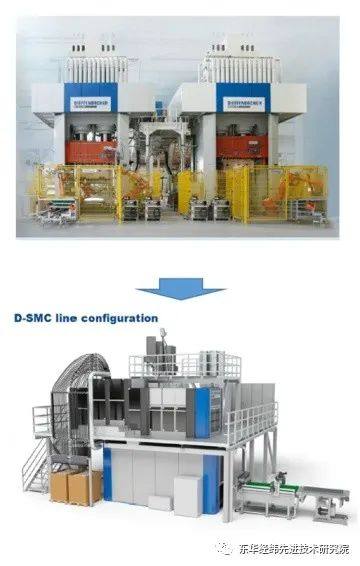
圖15?相對(duì)于傳統(tǒng)加工法的SMC(照片上),將D-SMC(照片下)樹脂材料調(diào)配設(shè)備設(shè)置在成型機(jī)旁邊可直接向成型機(jī)內(nèi)投料

D-LFT (Direct Long Fiber Thermoplastics) 是將使用長(zhǎng)纖維復(fù)合材料的熱塑性樹脂成型,從聚合物溶解到成型過程的工序直接銜接的生產(chǎn)系統(tǒng)。其特征是,由于使用了碳纖維,耐熱性十分優(yōu)越,具有較高的拉伸強(qiáng)度的同時(shí),能夠很好的保持復(fù)雜產(chǎn)品形狀的尺寸精度。如照片所示,在前置模塊的骨架部分、下層擋板、備胎板等成型商品上廣泛應(yīng)用。
Tailored D-LFT通過在D-LFT成型時(shí)使用追加的加強(qiáng)材料同時(shí)成型,可使剛性和強(qiáng)度以及能量吸收能力進(jìn)一步提升。這兩種技術(shù)也是由Dieffenbacher公司和Fraunhofer ICT及DSM公司共同開發(fā),提供可生產(chǎn)多種汽車配件的設(shè)備。
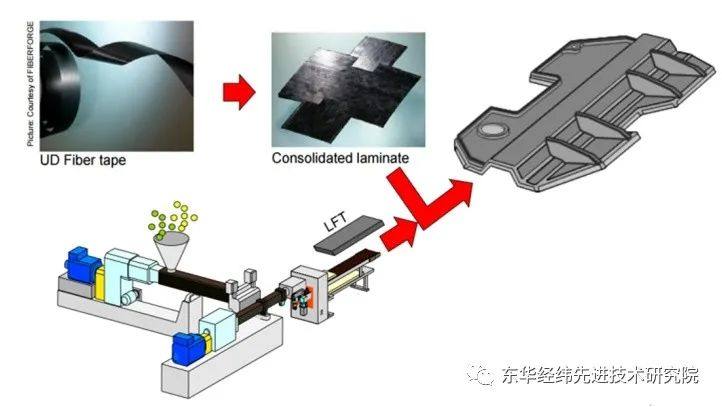
圖16?Tailored D-LFT成形工藝

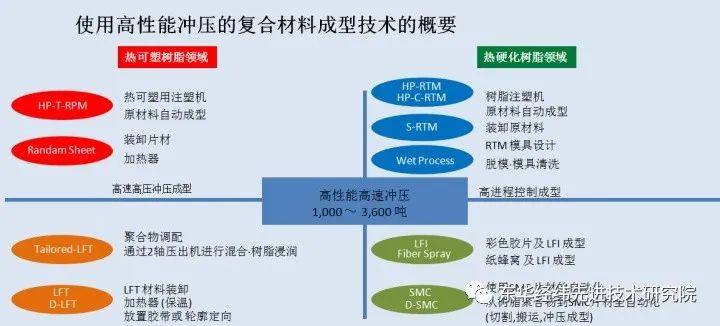
圖17?使用高性能沖壓成型的復(fù)合材成型技術(shù)
通過整理使用了高性能沖壓成型的復(fù)合材料成型技術(shù)后,得到如上圖的分類。以往雖然以使用CFRP產(chǎn)品的熱硬化性樹脂為主,但使用熱塑性樹脂的產(chǎn)品正在增加。作為最終工序,即使是熱硬化性樹脂成型的HP-RTM產(chǎn)品,也有在前工序使用CFRP的原材料成型時(shí),通過使用了熱塑性樹脂HP-T-RTM來成型的例子,RTM也不斷地在開發(fā)新的成型技術(shù)。

德國(guó)正在大力推進(jìn)整車廠、供應(yīng)商、設(shè)備廠商等民間企業(yè)和大學(xué)、研究機(jī)關(guān)相互協(xié)作。產(chǎn)、官、學(xué)與新技術(shù)相結(jié)合的計(jì)劃已經(jīng)確立,通過各自的經(jīng)驗(yàn)和知識(shí)技術(shù)相結(jié)合從而推進(jìn)開發(fā)。參加此項(xiàng)目的大學(xué),研究機(jī)關(guān)的人材又能進(jìn)入民間企業(yè),從人材培養(yǎng)的觀點(diǎn)來看也是十分優(yōu)秀的。
前述的Fraunhofer是德國(guó)十分有實(shí)力的研究機(jī)關(guān),在德國(guó)國(guó)內(nèi)有60以上研究據(jù)點(diǎn),有約2萬人的員工從事研究工作。研究課題主要是以3-5年后為中心的實(shí)用化應(yīng)用技術(shù)。
其中之一的Fraunhofer ICT以輕量化技術(shù)開發(fā)為主、與各整車廠及設(shè)備廠商等就CFRP的產(chǎn)品技術(shù)進(jìn)行了許多共同開發(fā)。每年的研究預(yù)算約4000萬歐元十分龐大。有550名員工,安防相關(guān)的員工約為300名,汽車和一般產(chǎn)業(yè)相關(guān)的研究人員150名。

Fraunhofer ICT

2016年上市的新型BMW 7系上采用了CFRP,生產(chǎn)技術(shù)方面,車身各部位采用樹脂注入成型(RTM)法的CFRP加強(qiáng)配件。新型7系如BMW i系列一樣,駕駛艙部分并非全都使用CFRP單殼體構(gòu)造,而是在鋼制車身的基礎(chǔ)上,部分使用鋁合金和CFRP以達(dá)到輕量化的目的。不僅BMW、奧迪、梅賽德斯奔馳預(yù)定在新型車型上采用CFRP,在歐洲CFRP于零售車輛上的應(yīng)用技術(shù)開發(fā)也在迅速推進(jìn)。
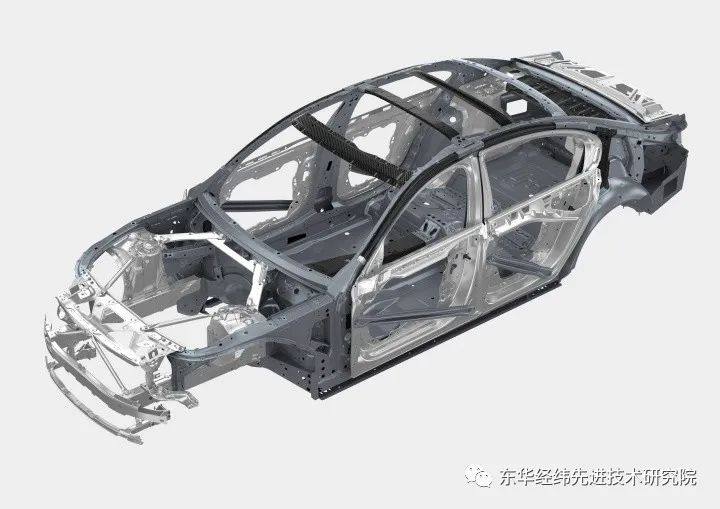
新型BMW 7系的車身構(gòu)造
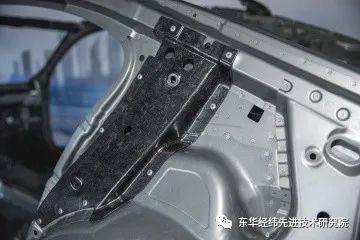
中心梁加強(qiáng)
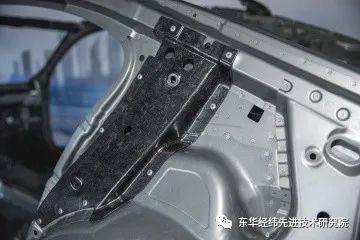
后柱加強(qiáng)
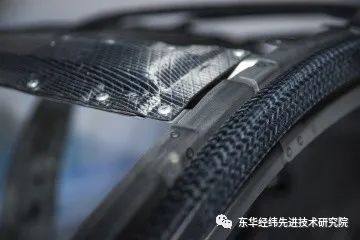
中柱及側(cè)柱上采用CFRP
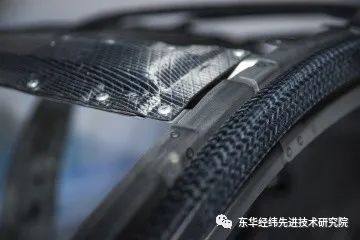

車頂和車頂側(cè)軌

車頂側(cè)軌
來源:前沿材料
編輯:艾帥帥
?
原文始發(fā)于微信公眾號(hào)(艾邦高分子):碳為觀止!寶馬車型減重39%,碳纖維復(fù)合材料技術(shù)如何在德國(guó)汽車領(lǐng)域大顯身手?