摘要:氫燃料電池具有清潔、高效等諸多優點,受到了世界各國的高度關注,極板是其重要部件之一。綜述了質子交換膜氫燃料電池金屬雙極板設計、成形等方向的研究和應用進展。在金屬雙極板設計方向,從極板平面流場分布設計、3D 流場設計、考慮電堆結構的極板流場設計以及微流道尺寸優化設計等方面進行綜述;在金屬極板成形方向,從剛模沖壓成形、軟模沖壓成形以及成形質量與電池性能相關性等方面進行綜述。最后,結合筆者對行業的調研和理解,對未來金屬極板的方向發展進行了展望。
關鍵詞:氫燃料電池;金屬雙極板;流場設計;沖壓成形;工藝與性能相關性
DOI:10.3969/j.issn.1674-6457.2022.03.004
人類賴以生存的傳統化石燃料日漸枯竭,世界各國政府紛紛出臺傳統能源車禁售時間表,氫能作為國際公認的清潔、高效能源,受到各國政府和產業的高度重視。燃料電池通過化學反應直接將化學能轉換成電能,產物只有水,并且本身沒有運動部件,結構簡單,能量轉換效率大于80%,遠高于燃燒發動機。
早在 20 世紀 60 年代,美國研制了堿性氫燃料電池,成功應用于阿波羅宇宙飛船、航天飛機等航天器中,累計運行 10 余萬 h,可靠性達到了 99%[1]。隨后,歐、美、日本和韓國等發達國家,開發了功率大、工作和啟動溫度低的質子交換膜氫燃料電池堆,應用于乘用車、固定式分散電站等民用領域。比如,日本東京政 府將奧運村打造成“氫氣城市”,5000多住戶和商業設施全部采用氫燃料電池供電;豐田汽車公司 2014 年推出了第1代 Mirai 氫燃料電池汽車,累計銷售超過了 1 萬輛[2],并于 2020 年 12 月發布了第 2 代量產化 Mirai 氫燃料電池乘用車,采用前置電堆系統,優化 了儲氫系統以及后驅動,其電池堆由 330 節燃料電池 串聯,峰值功率為 128 kW,體積功率密度達到 4.4 kW/L,質量功率密度為 4 kW/kg,續航里程達到 了 850 km,性能得到了大幅提升,豐田 Mirai 第 2 代 氫燃料電池車結構見圖 1。
圖 1 豐田 Mirai 第 2 代氫燃料電池車結構
國內,燃料電池中巴車早在2008年北京奧運會、 2010 年上海世博會期間就進行了示范運行。如今,北京冬奧會在張家口打造氫能奧運村,張家港市、常熟市、如皋市等建立了加氫站并運行氫燃料電池公交線路,上汽集團推出了榮威 950 氫燃料電池乘用車。截止到2019年底,我國累計推廣燃料電池汽車超過了 6500 輛,建成加氫站超過了50 座,逐漸形成了較 為完整的產業鏈。為了推動新能源領域的快速發展,氫能相關內容寫入了 2019 年《政府工作報告》,《中國制造 2025》將新能源汽車作為10大重點發展領域 之一。2020 年 10 月國務院出臺《新能源汽車產業發展規劃(2021—2035 年)》,提出開展燃料電池系 統技術攻關,突破氫燃料電池汽車應用支撐技術等瓶頸,提升基礎核心零部件等研發能力。我國氫能相關產業發展進入快車道,各大主機廠、燃料電池專業廠家等紛紛投入巨資開展了氫燃料電池相關技術研發和示范應用,目前已經形成了主機廠、燃料電池企業 以及相關零部件配套企業等完整的產業鏈。新源動力股份有限公司 2020 年 6 月推出新一代金屬極板氫燃料電池堆,額定輸出功率為 110 kW,體積功率密度 為 4.2 kW/L。大批氫燃料電池車、船舶等相繼下線或進入測試階段,如雄韜氫恒 31 t 氫燃料電池碴土車下線、氫時代 110 kW 氫能重卡進入測試、畔星 50 kW 氫燃料電池灑水車發布等等。我國氫燃料電池核心技術指標與國際先進水平仍有較大的差距,商業化應用方面還有一定的制約,歐陽明高院士等[3]分析認為,目前差距主要表現在體積/質量功率密度、壽命、電池成本等方面,這些均與氫燃料電池雙極板的設計與制造水平密切相關。?
質子交換膜氫燃料電池(PEMFC)結構如圖2 所示[4-5],其核心部件之一是微流道雙極板,起到均勻分配氣體、收集電流、冷卻和支撐等作用。目前,極板微流道槽寬約為 0.5~1.5 mm、深寬比為 0.5,材 料主要有石墨、金屬以及復合材料等,占電池總重量的 60%~80%、成本的 30%~40%、體積的 60%,是導 致電池體積/質量功率密度低、成本高的主要因素之一[6-7]。石墨基極板主要采用微細機械加工、壓鑄等工藝,金屬極板主要采用沖壓、液壓脹形等工藝。由于金屬極板具有重量輕、體積小、制造成本低等多種優勢,是氫燃料電池發展的主要方向之一。為此,筆者對金屬極板流場設計和制造技術研究及應用現狀進行綜述,并對其發展趨勢給予展望。
1 燃料電池雙極板流場設計發展現狀?
1.1 極板平面流場分布設計現狀
燃料電池雙極板起到分配反應氣體、收集電流、排水、導熱和機械支撐等多種重要作用。雙極板的流場結構決定了有效反應面積比例、反應氣體分布均勻性等,顯著影響燃料電池功率、極板范圍的電流密度分布、極板間電壓一致性等多個重要參數,從而決定了燃料電池工作性能指標和使用壽命,是燃料電池結構設計的重要內容[8]。典型的雙極板流場主要有點狀流場、平行直流道流場、交指形流道流場以及單通道蛇形流道流場等,如圖 3 所示,分別在流場分布均勻性、流體壓降、電池壽命以及排水等方面存在不同程度的不足[9-10]。因此,國內外學者在流場設計與性能分析方面開展了大量研究工作。QIU 等[5]設計了由 14 個等長度流道構成的蛇形流場雙極板,獲得了均勻分布、密度較高的電流。Um 等[11]采用計算燃料電池動力學模型,研究了雙極板流場傳質行為,發現交指形流場較平行直流場,更能夠通過擴散層傳遞氧、排出水。FERNG[12]和 Hashemi 等[13]學者構建了 3D 計算流場動力學模型,發現蛇形流場較平行直流場有更好的反應氣體和電流分布。Liu 等[14]設計了尺寸逐漸變小的微流道,提高了燃料的利用率。Hu 等[15]采用 3D 計算流體動力學方法,優化設計了點狀-交指形組合流場。本田等公司采用了平行波浪形流場,兼顧了排水和減小進出口壓差[16]。Sainan 等[17]采用流體動力學分析了多流道蛇形流場雙極板中傳質、電流、氣壓以及溫度之間的關系,并可用于分析水的產生。Freire 等[18]分析了不同橫截面形狀微流道蛇形流場水管理 方面的性能,發現梯形橫截面時對潤濕溫度等更加敏感。此外,國內外學者還提出了仿葉脈、肺氣管以及樹冠等仿生微流道陰極流場,集合了蛇形和交指形流場的優點,能夠更好地排水,提升 30%的峰值電流密度,并隨著分支數量的增加而增加。然而,仿生流場因過于復雜而制造更困難,成本更高[19-20]。近年來,基于電池輕量化、微型化以及制造成本、質量控制等考慮,商業化應用的金屬極板流場分布趨于簡單化, 將利于排水的平行直流道改進成平行波浪形微流道流場,以促使氣體充分擴散,并在氣體分配區采用點狀流場和放射狀分布微流道等獲得復合流場,提升氣流分配均勻性,將是未來極板流場的主流方式。
1.2 極板 3D 流場設計現狀?
微流道內的燃料氣體在靠近質子交換膜一側會因參與化學反應導致濃度降低,對燃料利用率等產生影響,微流道內的流場設計受到了廣泛關注。Heidary 等[21]研究了微流道突起堵塞的影響(見圖 4),發現陰極板微流道堵塞促進氧氣進入擴散層,增加氧在催化層聚集,提升電池堆性能,例如在模擬條件下提升靜功率 30%,而陽極微流道突起則沒有類似的效果。另外,微流道突起堵塞對排水有較大影響,在低流速、較低相對濕度時,促進質子膜水化,從而提升膜的質子導電率。Cai 等[22]設計了由主流場和次流場構成的多孔材料陰極 3D 流場,微流道脊部多孔結構利于反應物向質子交換膜流動,從而增加了反應物傳輸效 率、提高了分布均勻性。Han等[23]設計了底部帶波浪形結構的石墨微流道(見圖 5),增加了反應物的流動速度梯度,25 cm2 的單元實驗測試表明,最大功率 密度提高了 5.76%。以上復雜流場設計主要針對微機械加工的石墨極板,考慮制造技術不同,并不適用于金屬極板流場設計。為此,豐田Mirai 第 1 代中采用了網格狀復雜 3D 流場結構,解決了排水等問題,但存在制造難度較大等問題,已經被 Mirai 第 2 代舍棄, 而改為微流道槽寬變化的流場設計。但文濤等[24]設計了一種側邊帶凸起的 3D 流道結構(見圖 6),反應物和冷卻劑的流動狀態由層流轉化為紊流,但未見實物和性能測試等相關報道。總體而言,3D 流場結構設計將微流道內層流改變為擾流,從而促進了燃料在微流道深度方向流動,改善了靠近質子交換膜組一側因化學反應消耗而引起的燃料濃度降低等問題,必將被更多的商業化應用所采納。
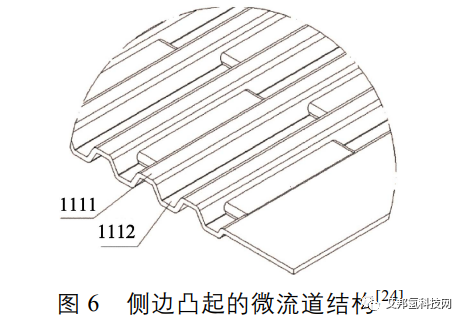
1.3 考慮電堆結構的極板流場設計?
為了提高雙極板流場性能,不僅僅局限于雙極板本身,而是從燃料電池總體結構角度,對反應物流場進行了更復雜的結構設計。Yang 等[25]綜合考慮反應物濕度、溫度等因素,改變出入口處冷卻效果,通過建立非等溫模型,發現改變氧氣的相對濕度,可以提升燃料電池性能。Jung等[26]從燃料電池反應氣體流場、冷卻以及排出等整體需求角度,設計了短且長度基本相等的直流道雙極板(見圖 7),兩側的微流道分別作為反應物通道和冷卻通道,結構緊湊、流場分布均勻、壓降小、冷卻效果好,同時,對反應氣體進出口進行設計,反應物自上而下流動,與重力平行,直流道方向與重力成 45°,非常利于快速排水。日本豐田汽車公司采用優化電堆結構設計、氫流量和氣壓等措施,設計了自潤濕燃料電池堆(見圖 8)[27]。由此可見,金屬極板流場設計是一個系統性問題,不僅要考慮極板流場本身,還要從燃料電池堆整體結構角度,不僅要考慮燃料分布均勻性,而且要綜合考慮排水、散熱、有效面積比例等多種因素優化設計極板流場結構。
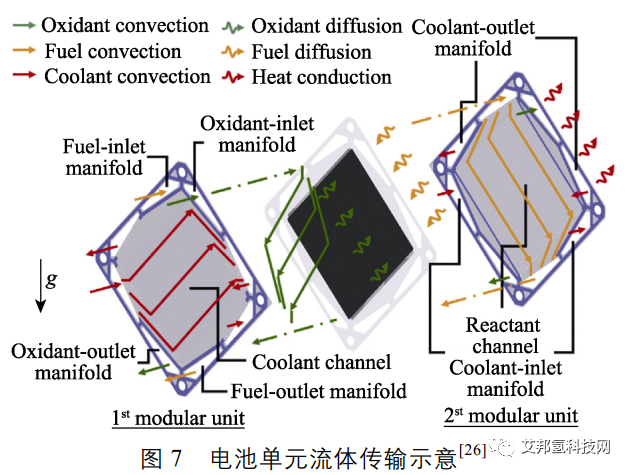
1.4 極板微流道尺寸優化設計現狀?
除了雙極板流場分布,微流道形狀尺寸(槽深、槽寬、脊寬、圓角等)對反應物分布、導電性、水管理以及反應物利用率等均會產生顯著影響。Shimpalee 等[28]發現,相同流場面積下,電流密度分布等隨蛇形流場流道長度、數量的增加而更加均勻,而 Cooper 等[29]研究發現,凈功率密度等隨交指形流 場微流道長度與寬度比值的減小而提升。Kumar 等[30] 研究了單通道蛇形微流道尺寸對陽極氫消耗的影響, 在 80%條件下優化的微流道尺寸分別為槽寬為 1.5 mm、脊寬為 0.5 mm 以及深度為 1.5 mm。Yoon 等[31]研究發現脊寬越小,電池性能越好,說明氣體擴散較導電性更加重要。然而,傳統的雙極板流場優化設計,主要面向兩側表面均可數控加工的石墨雙極板,并不完全適合采用沖壓成形的金屬極板。為此,彭林法等[32]針對金屬雙極板液壓脹形工藝,建立相應 優化模型,發現當微流道尺寸分別為槽寬為 1.0 mm、 脊寬為 1.6 mm、槽深為 0.5 mm 以及圓角半徑為 0.5 mm 時,反應效率最高,達到 79%。Zhao 等[33]針對金屬雙極板沖壓成形時,發現模具圓角、凸凹模間隙是決定微流道成形深度的主要參數,其減小會導致 成形深度極限的減小,他們構建了反應效率和成形能力模型,發現板厚為 0.1 mm 時,最佳微流道幾何尺 寸參數為槽寬為 0.9 mm、脊寬為 0.9 mm、深度為 0.4 mm 以及圓角半徑為 0.15 mm。由于金屬極板沖壓成形很難在其兩面同時成形出連續的反應物和冷卻流場,還必須考慮金屬薄板塑性成形極限、局部減薄等制約,因此,金屬極板流場設計時,金屬薄板成形性能、沖壓工藝等也是必須要考慮的因素。
2 金屬雙極板成形技術研究進展?
2.1 金屬極板剛模沖壓成形現狀?
金屬雙極板制造工藝主要有壓鑄成形、化學刻蝕 以及沖壓成形等,其中沖壓成形能夠成形厚度很小的金屬極板,而且制造效率高、成本低,是金屬雙極板制造的主流技術。Ko? 等[4,34-36]系統研究了不銹鋼、 純鈦微流道沖壓成形和液壓脹形工藝,發現 316、304 不銹鋼以及 T1 鈦成形性能較好,但純鈦微流道高度相對較小;微流道槽寬尺寸對成形性能影響顯著,尺 寸越小成形深度越小;成形力增加會引起脊表面粗糙 度增加,沖壓成形的雙極板接觸電阻大于液壓成形的極板,在燃料電池模擬環境下,成形件的耐腐蝕性能 降低。Chen 等[37]研究了不銹鋼雙極板沖壓成形工藝, 發現低速時易產生起皺、圓角破裂、脊減薄嚴重等缺陷,需要進行成形工藝優化。Elyasi 等[38]研究了 316L 不銹鋼雙極板沖壓工藝,發現無潤滑時微流道圓角處發生破裂(見圖 9),而有潤滑時能夠顯著提高成形微流道高度、提升厚度分布均勻性,尺寸誤差僅有 2.9%。針對金屬雙極板沖壓成形時圓角減薄嚴重甚至破裂的現象,彭林法等[39-40]研究了不銹鋼雙極板微流道沖壓 成形工藝,采用優化設計的雙極板,沖壓成形出高質量金屬雙極板(見圖 10)。同時,也發現沖壓成形金屬雙極板微流道深度在寬度、長度方向存在一定的誤差,會對后續電池裝配和功率等性能產生較大影響。任志俊等[39]使用厚度為0.15 mm、伸長率為33%的TA0 純鈦板,考慮薄板成形困難、易出現翹曲等缺陷,設計了連續成形模具裝置,沖壓成形出槽寬為 1.2 mm、深為 0.35 mm 的微流道純鈦雙極板。為了獲得微流道深寬比較大、壁厚分布較均勻的金屬極板,業內常采用多步成形工藝[40],已經實現了小批量試生產。隨著燃料電池體積、重量、成本等要求越來越高,極板的厚度也越來越小,厚度為 75 μm 的金屬極板已經開始商業應用。然而,金屬極板沖壓成形難度也越來越大,主要表現在壁厚減薄率增加、微流道尺寸精度控制更加困難、脊頂部的平整度難以保證等。可喜的是,在工業化需求牽引下,這些難點正在逐步被解決。
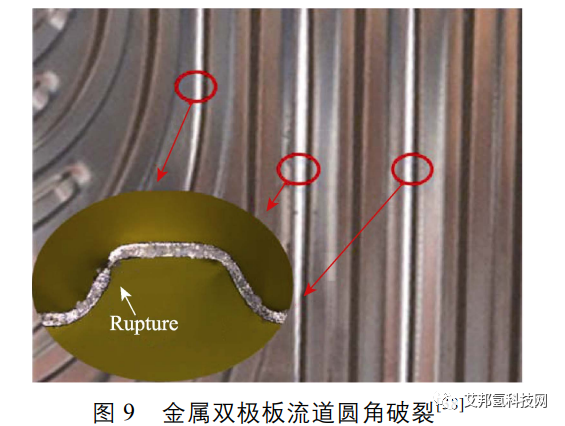
2.2 金屬極板軟模成形現狀?
為了避免剛性模具沖壓成形壁厚減薄等問題,提出了僅使用凹模或凸模的金屬雙極板液壓脹形、橡膠成形等軟模成形工藝。Ko?[34]和彭林法等[32]開展了金屬雙極板液壓脹形工藝研究(見圖 11),發現壁厚分 布更加均勻,微流道尺寸越小成形越困難,所需液壓力也越大。Osia 等[41]研究了金屬雙極板液壓脹形、沖壓成形以及兩者的復合工藝,發現復合工藝綜合了 兩者優點,成形的雙極板質量更高。劉艷雄等[42-43] 開展了金屬雙極板橡膠軟模成形工藝,分析了橡膠硬度、內外圓角以及側壁斜角等參數對工程應變、微流 道深度等的影響,并發現槽寬/脊寬比值大于 1 時, 應選擇凹模成形,而比值小于 1 時則選擇凸模,最終成形出 SS304 不銹鋼雙極板。Elyasi 等[44]采用帶微結構橡膠作為軟模,成形的雙極板微流道最大深度比從 76%提高到 88%,同時提高了微流道尺寸精度。Lee 等[45]研究了有、無涂層純鈦、槽寬為 0.8 mm 的微流 道雙極板橡膠軟模成形工藝,發現純鈦微流道成形最大深度僅有 0.27 mm,且形狀失真嚴重。橡膠軟模成形時,由于微流道成形變形量極大,橡膠壽命較低, 很難滿足工業化生產需要。液壓成形在模具成本、金屬極板壁厚均勻性等方面具有明顯的優勢,比利時 Borit NV 以及國內相關公司開展了金屬極板液壓成形,雖然單次成形時間相對較長,但是采用一模多件等技術,在一定生產效率窗口內保持較低的零件成本優勢,使其越來越受到行業的關注。
2.3 金屬極板成形質量與電池性能相關性研究現狀?
金屬極板由數量較大的微流道陣列組成,其微小的流道尺寸和極薄的板厚,對微流道成形深度等一致性產生顯著的影響。從應變狀態角度分析,薄壁微流道成形以脹形為主,受約束和摩擦力等綜合作用,位于極板中心位置的微流道深度最小,在長度方向或寬度方向,越接近邊緣位置,微流道深度越 大,如圖 12 所示[46]。此外,由于極板本身剛性較差,微流道在極板面內分布極不均勻,沖壓成形的金屬 極板產生翹曲等缺陷;微流道脊寬較小,其頂部平面部分較小甚至是一定弧度的曲面。受以上多種因素影響,金屬極板與質子交換膜的接觸面并非平面,必須施加預緊力以保證金屬極板與質子交換膜的緊密接觸,導致接觸面上不同區域接觸應力不同,對接觸電阻、質子交換膜孔隙率等均產生顯著影響, 從而降低燃料電池輸出功率、性能均勻性和壽命等。因此,金屬極板成形質量、裝配精度以及預緊力等與燃料電池性能相關性研究,是其工業化應用的重要內容之一,受到業內和學術界的廣泛關注,相關企業做了大量相關研究,但是成果通常作為內部資 料很少公開。在公開資料中,上海交通大學做了較多的相關研究。
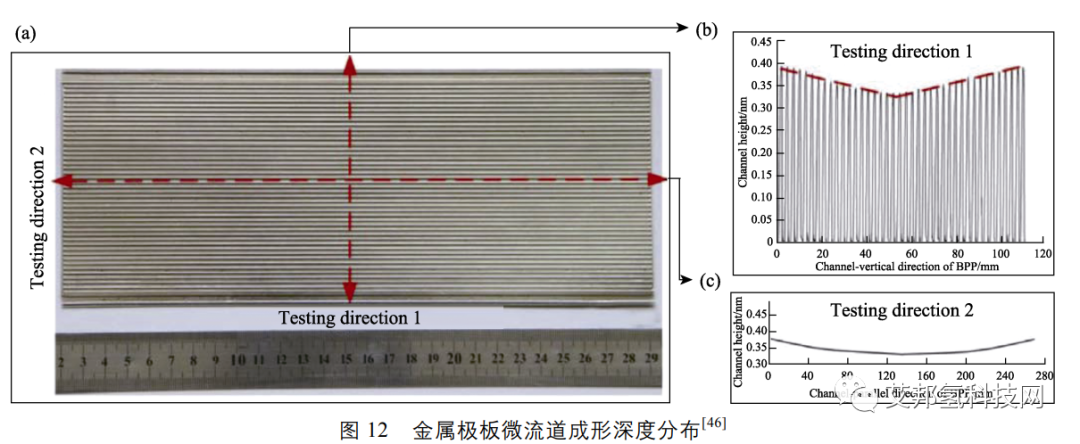
來新民教授團隊[47]分析了微流道/脊寬對接觸電阻、交換膜組孔隙率的影響,發現微流道/脊寬小于 1.0 時,相同裝配位移下的接觸電阻和孔隙率均明顯增大,以微流道圓角半徑與槽寬之比作為尺寸因子, 獲得了尺寸效應的影響規律。進而,分析了微流道、 脊等深度誤差對接觸電阻的影響,采用蒙特卡洛方法處理深度誤差分布隨機性(見圖 13),結果表明,深度誤差對極板與質子交換膜組間的接觸電阻有顯著的影響,較大的高度誤差顯著增加接觸電阻(見圖 14),并降低燃料電池性能;并且,深度誤差分布隨機,使燃料電池每個單元的接觸電阻存在明顯差異, 特別是尺寸誤差超過 30%時,接觸電阻增加了 14.5%。因此,金屬極板成形尺寸誤差應控制在 20 μm 以內。金屬雙極板焊接可以明顯改善極板的平整度等參數,對接觸電阻產生顯著影響,稠密的焊縫可使接觸電 阻減小 47%,雙極板焊接工藝優化是非常必要的。此外,建立了燃料電池裝配模型,研究了裝配壓緊位移量對接觸電阻、膜孔隙率的影響,優化裝配夾緊力為 0.67 MPa,極板的定位誤差應控制在 0.05 mm 以內[48-49]。
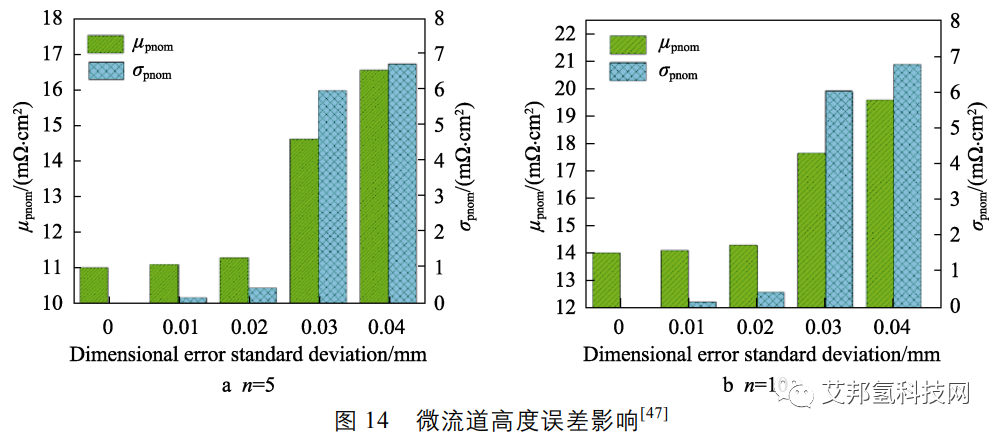
3 結語?
質子交換膜氫燃料電池具有轉換效率高、零排放等多種優勢,在車、船、飛行器、固定電站等諸多領域有著廣泛的應用前景,世界各發達國家均開發了相關產品,已經進行了商業化運用或示范應用。雙極板在燃料電池中起到分配反應氣體、收集電流、冷卻以及支撐等多種作用,對燃料電池電流密度、體積/質量功率密度、成本、壽命等多個參數有重要影響,是其核心部件之一,是決定燃料電池的商業化應用進程的重要因素之一。綜合文獻和行業發展調研,極板優化設計、成形精度等有了很大提高,對氫燃料電池性能提升了 20%~50%。目前,國內外科研工作者和相關企業開展了流場設計、精密制造以及性能評價等大量相關研究,開發了多款金屬極板應用于氫燃料電池,已經從示范性應用逐步進入到階段性量產或商業化應用階段。但是,在質子交換膜氫燃料電池商業化應用需求牽引下,對金屬極板提出了更高要求,主要包括:
1)以提升燃料電池性能為目標的極板結構多層次優化設計。極板的功能較多,對燃料電池的多個性能指標有著重要影響,從多個層次進行優化設計:極板整體結構角度,考慮極板進出口排布、排水以及有效反應面積比等因素;極板流場角度,考慮反應氣體分配均勻性、流阻、壓降等因素;微流道結構角度,微流道/脊寬比、側壁傾斜角度、圓角半徑等幾何結構等對接觸電阻、排水性能等影響因素;基材塑性成形性能角度,考慮金屬材料成形極限、回彈、各向異性等對微流道深度、幾何精度以及極板板形精度因素。綜合考慮極板多種作用,從多個層次優化設計極板結構,以提升燃料電池性能。
2)低成本、高質量極板智能成形技術。不銹鋼極板成形工藝逐漸成熟,已經從示范性應用逐步進入到階段性量產或商業化應用階段。目前,氫燃料電池整體成本較高,目前寄希望于極板大批量生產,以能夠將成本降低至市場所接受的百元以內。綜合金屬極板制造行業發展,基于連續模的沖壓成形制造技術必將是主流方向。然而,金屬極板大批量生產涉及材料性能一致性、工藝穩定性以及質量控制等多個環節,相關研究如在線檢測與質量控制技術等,還有待進一步加強,尤其是板厚不斷減小、鈦等難變形材料應用,更需深入研究低成本、高質量極板智能成形技術。
3)極板成形質量與燃料電池相關性研究。該相關性研究對細化極板成形質量標準,推動燃料電池技術整體、快速發展具有重要意義。然而,受燃料電池測試成本等制約,極板微流道尺寸誤差、板形翹曲、表面質量以及裝配參數和誤差等對燃料電池性能的影響還不夠系統,并且出于對知識產權保護的考慮,研究成果很少公開,更不利于該問題的深入系統研究。
4)極板焊接和表面改性等技術。沖壓成形的一般為單個極板,電堆用雙極板產品還需要焊接、表面改性處理等工序。單極板焊接成為雙極板,由于板厚小、面積大,焊接質量可靠性不高,在成本、良品率等方面還有待進一步提升。金屬極板耐腐蝕性能不佳,表面改性技術是提升其耐腐蝕壽命的主要途徑。然而,金屬極板的結構特點、工作環境等對大面積、復雜結構的金屬極板表面改性技術提出了巨大挑戰。目前,納米多層碳膜已經應用于不銹鋼金屬極板,但在使用壽命等方面還有待提高。
總之,金屬極板設計與制造技術在需求牽引下已經獲得了長足的進步,進入示范或小批量生產階段,但是在結構多層次優化設計、低成本高質量智能制造、極板成形質量與電堆性能相關性以及極板焊接和表面改性技術等方面,還有待進一步提高。
來源:《精密成形工程》
原文始發于微信公眾號(艾邦氫科技網):燃料電池金屬雙極板設計與成形技術最新動態
