本篇文章主要介紹了兩種復合材料成型工藝,分別是:HP-RTM和濕法模壓成型工藝。
HP-RTM成型工藝
HP-RTM是英文High Pressure Resin Transfer Molding的簡寫,全稱是高壓樹脂傳遞模塑成型工藝,簡稱HP-RTM成型工藝。它是指利用高壓壓力將樹脂對沖混合并注入到預先鋪設有纖維增強材料和預置嵌件的真空密閉模具內,經樹脂流動充模、浸漬、固化和脫模,獲得復合材料制品的成型工藝。
上述介紹中關鍵詞介紹:
-
高壓壓力:這里的高壓是相對于傳統RTM(Resin Transfer Molding)工藝而言,HP-RTM把注膠壓力提升到80bar。高壓注膠的好處是樹脂可以更快的達到每個拐角,因此可以提高產品的纖維含量,提高產品性能,對于造型復雜的零件更加適用;
-
預先鋪設:這里預先鋪設的纖維增強材料是指已經經過剪裁預成型的纖維材料;
-
預置嵌件:嵌件是指在成型前放置于模具里的零件,材質有金屬和非金屬,這樣使得成型后的制品,嵌件被包入本身的結構中,不可拆卸。是否需要預置嵌件由制品的結構設計決定。
以上流程可以通過一個簡單的工藝流程圖來體現:
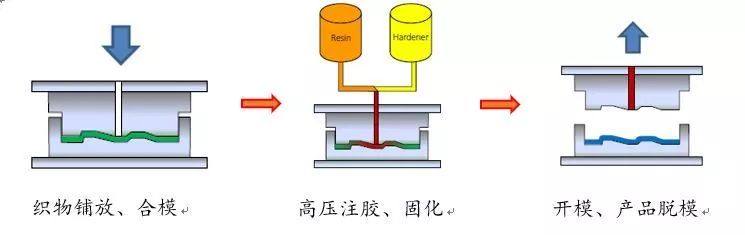
前面提到HP-RTM成型工藝是相對于傳統RTM工藝而言進行優化后的成型工藝,在不同的優化方向上,也相應開發出了其它的以RTM工藝為基礎,進一步提高生產效率和制品性能的工藝,比如現在HRC擁有的HP-CRTM(High Pressure Compression Resin Transfer Molding)成型工藝.
HP-CRTM成型工藝是在HP-RTM工藝技術中的樹脂注膠前,將模具上移0.5~1mm,增大密封模腔間隙,模具可以有更寬的澆道,降低樹脂流動阻力,注膠結束后再將模具在高壓下完全閉合,樹脂體系隨閉合壓力流動充模,成型壓力相對較低,這樣既保證纖維不亂紋,又保證了較高的注射速度。
工藝流程圖體現為:
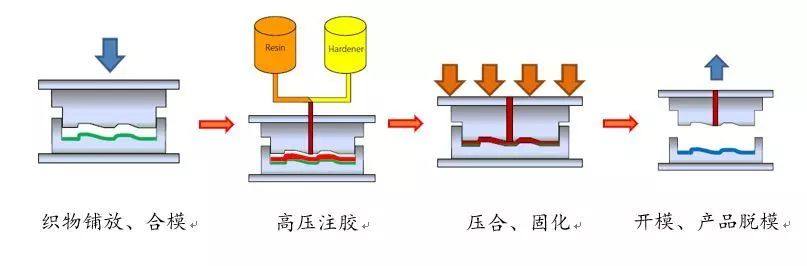
HP-RTM成型工藝是現在廣泛應用在多行業的復合材料成型工藝之一,它的優點在于可能實現相對于傳統RTM工藝的低成本、短周期、大批量、高質量生產(良好的制件表面),在汽車制造、造船、飛機制造、農業機械、鐵路運輸、風力發電、體育用品等多行業均有應用。
下面,我們來看一些采用了HP-RTM成型工藝及衍生的其它相關工藝得到的具體制品:
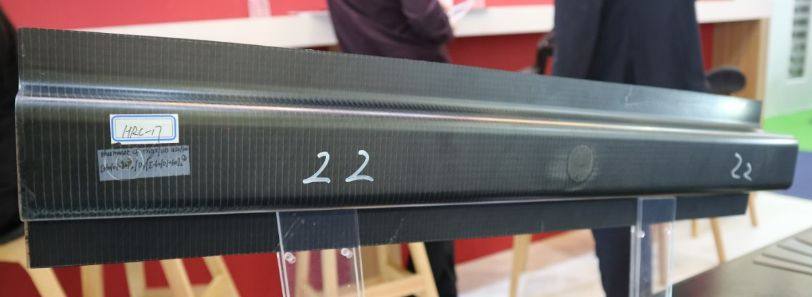
碳纖維電動滑板
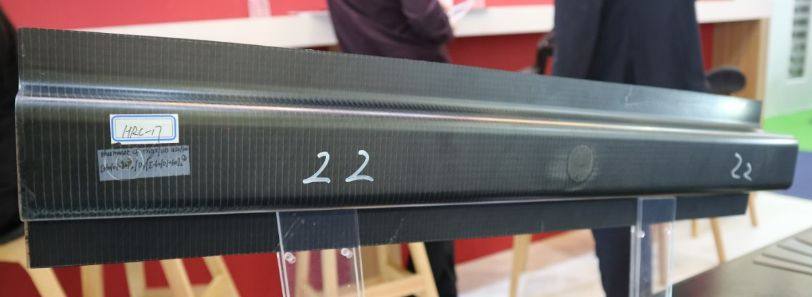
碳纖維帽型梁
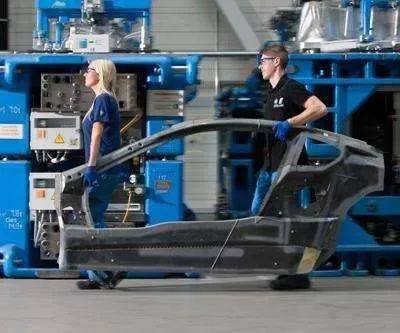
BMW i8 車身側框架
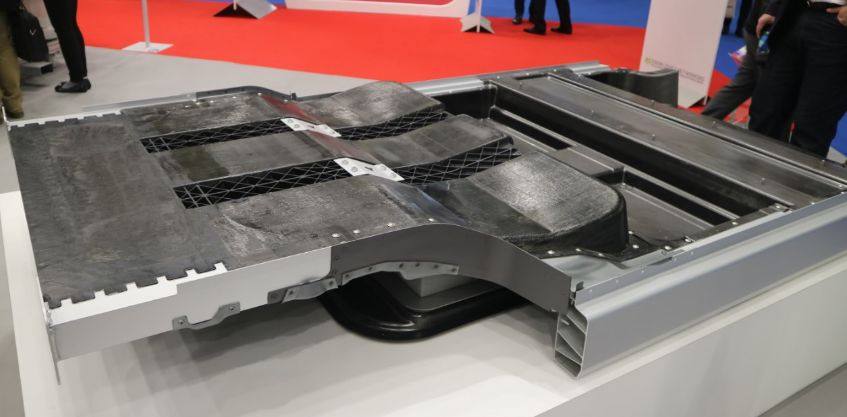
AUDI AG的碳纖維底板模塊,
成型工藝中應用了Ultra-RTM工藝
參考資料:
1. 微信公眾號:復材人生 《一鍵進入帶你了解HPRTM工藝》
2.? https://www.compositesworld.com/articles/hp-rtm-on-the-rise
?濕法模壓成型工藝
本期推送介紹的第二個成型工藝是濕法模壓工藝,也稱WCM(是Wet Compression Molding的簡稱)工藝,先來看相關的工藝流程圖:
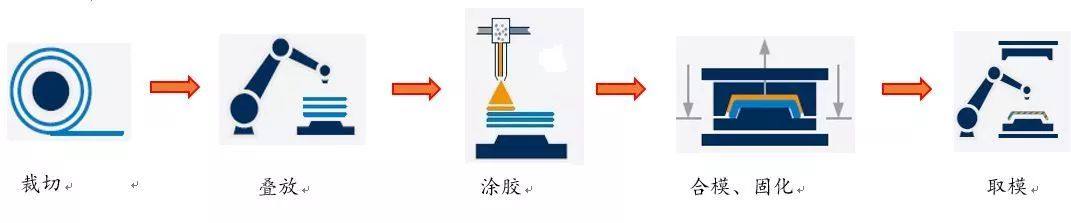
將濕法模壓工藝的成型步驟可分解如下:
1、使用裁切好的碳纖維或玻纖干布鋪放成平面;
2、將材料轉移在模具上;
3、進行涂膠,使樹脂覆蓋纖維;
4、進行合模,抽真空、加壓,加熱固化;
5、開模,取出產品。
濕法模壓工藝最主要的特點是前期裁切使用干的纖維布,先進行噴涂樹脂之后再放入模具進行成型固化,這也致使該工藝更適合加工形狀復雜程度低(2D或2.5D造型)的制品,應用行業廣泛,其優點是批量生產節拍快,模具設計簡單,單件成本低。
下面分享幾組應用濕法模壓工藝得到的制品及案例:
我們將上述關鍵詞串起來就得到了基本工藝流程,如下圖:

碳纖維mini機蓋
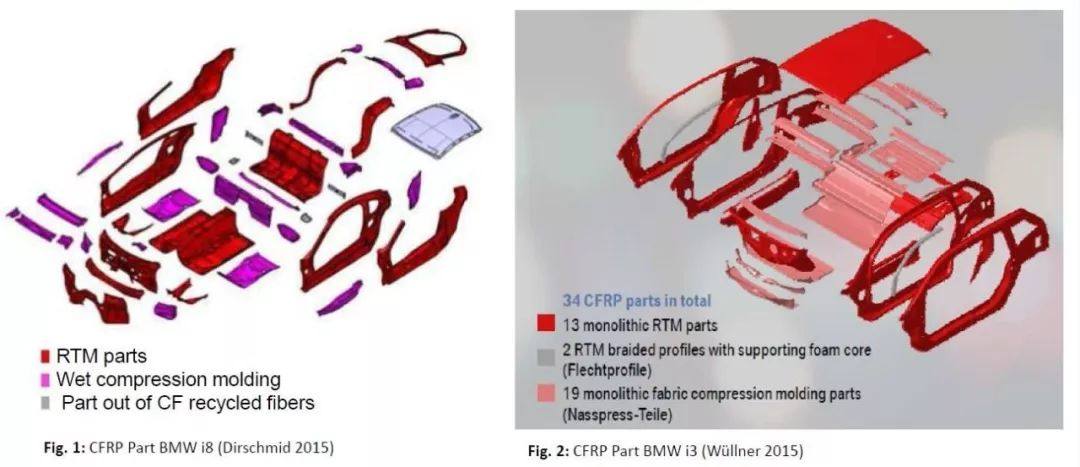
上圖是濕法模壓工藝在BMW i3和i8車型中應用圖示,其中在BMW i3(右)中使用了17個“濕壓部件”,在i8(左)中使用了21個。
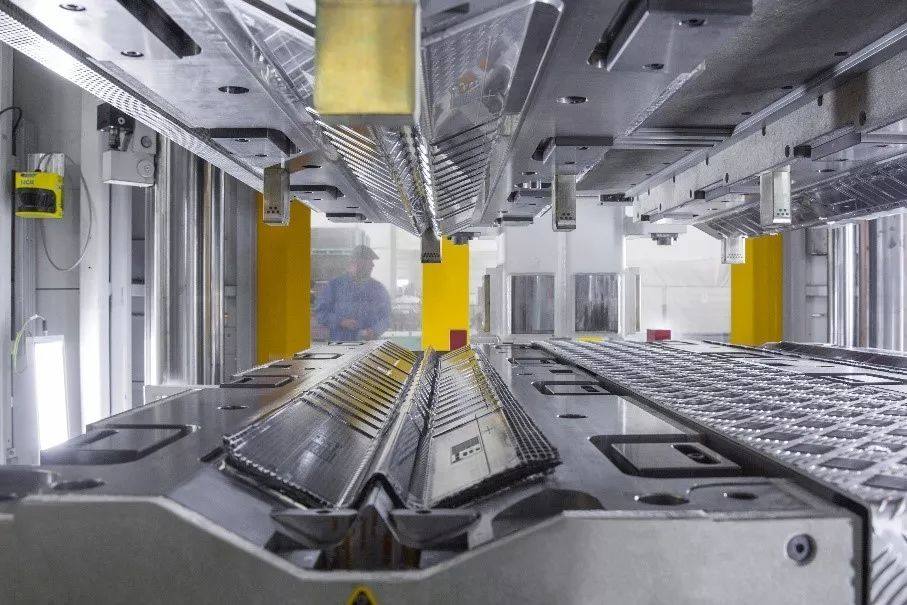
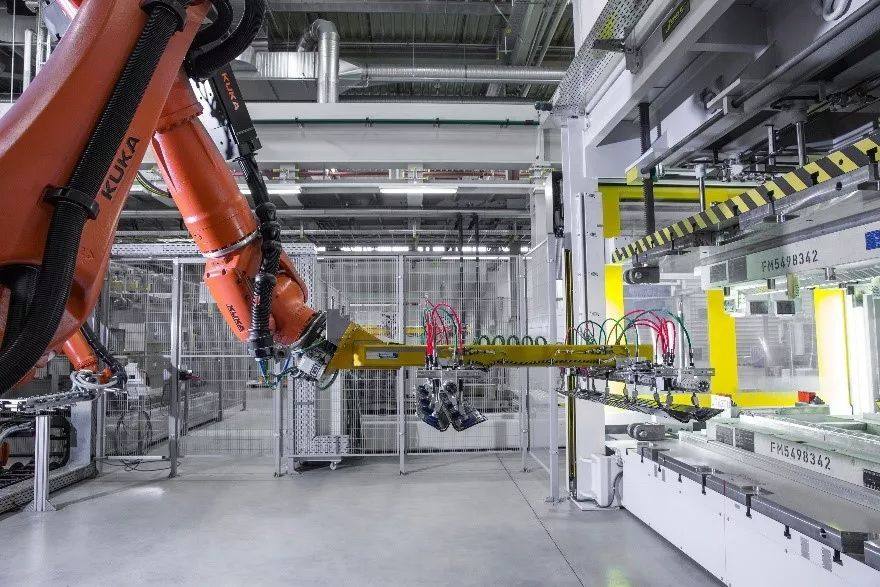
上圖,濕法模壓工藝被用來生產BMW7系的“Carbon Core(碳芯)”乘客艙組件,為造型復雜度較低的零件提供更短的生產周期和更低的成本。
參考資料:
https://www.compositesworld.com/blog/post/wet-compression-molding
文章來源于:黑話碳纖維
原文始發于微信公眾號(艾邦復合材料網):復合材料HP-RTM和濕法模壓成型工藝介紹