鈣鈦礦太陽能電池主要由五部分組成,包括透明導電基底、電子傳輸層(ETL)、鈣鈦礦吸光層、空 穴傳輸層(HTL)、金屬電極,具體如下:
1)透明導電基底:一般采用氧化銦錫導電玻璃(ITO) 或者氟摻雜的氧化錫導電玻璃(FTO)。作為其他材料的載體,光線由此射入,將收集到的光電子傳送至外電路。
2)電子傳輸層(ETL):由致密TiO2和介孔TiO2兩層材料組成。其中,致密TiO2用于阻止導電基底與 鈣鈦礦的直接接觸,避免空穴向導電基底傳輸;介孔TiO2為鈣鈦礦生長提供框架與支撐,形成多孔TiO2/鈣鈦礦混合層,用于傳輸電子。
3)鈣鈦礦吸光層:典型代表為碘化鉛甲胺(MAPbI3, MA=CH3NH3+),用于吸收太陽光產生光電子的活性材料。
4)空穴傳輸層(HTL):通常使用Spiro-OMeTAD,用于提取與傳輸光生空穴。
5)金屬電極:通過在空穴傳輸層外面蒸鍍一層金獲得,用于傳輸電荷并連接外電路。
鈣鈦礦電池的結構及工作原理
鈣鈦礦電池主要制備工藝
對應鈣鈦礦的五層結構,電子傳輸層(ETL)、鈣鈦礦吸光層、空穴傳輸層(HTL)為制備工藝的核心環節,最核心環節即鈣鈦礦吸光層的制備。透明導電基底層可外采導電玻璃或柔性片;金屬電極通常通過使用貴金屬真空蒸鍍獲得。
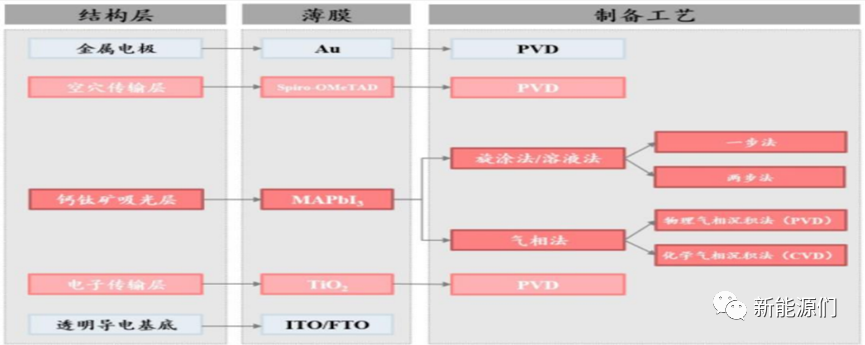
鈣鈦礦電池主要制備工藝
針對鈣鈦礦電池最核心的工藝環節(鈣鈦礦吸光層的制備),主要包括旋涂法以及氣相法。旋涂法又稱濕法,氣相法又稱為干法。
1)旋涂法:旋涂法工藝相對簡單,為目前主流的鈣鈦礦吸光層制備方法。按照步驟的不同可進一步分為一步法、兩步法。其中,一步法指將鈣鈦礦的原料全部加入溶劑中,完全溶解后形成前驅溶液,前驅體溶液旋涂于基板上,溶劑在高速旋轉中揮發,溶質留在基板上結晶形成鈣鈦礦薄膜。兩步法指,首先將PbX2溶于溶劑,旋涂在基底上成膜;然后將PbX2浸泡在溶液中或再次旋涂于基板上,與PbX2膜反應生成鈣鈦礦。
2)氣相法:包括物理氣相沉積法與化學氣相沉積法。氣相法適用于大面積器件的制備,同時可以避免旋涂法制備過程中有毒溶劑的使用。另一方面,由于控制前驅體的相對比例并非易事,氣相法對設備性能提出較高要求,高質量膜層的制備難度較高。
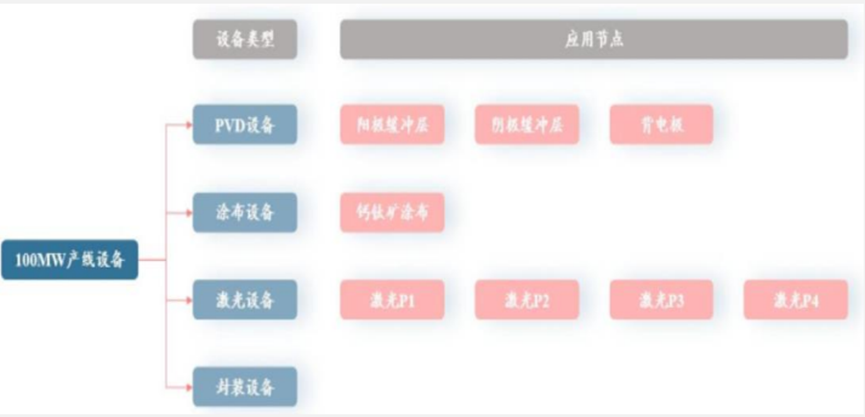
鈣鈦礦吸光層的制備工藝比較
鈣鈦礦電池制備主要設備需求
鈣鈦礦太陽能電池主要設備包括鍍膜設備、涂布設備、激光設備、封裝設備為鈣鈦礦電池制備四大設備,其中,鍍膜設備價值占比約50%。
從上述各設備的具體作用來說,鍍膜設備主要應用于制備陽極緩沖層、陰極緩沖層、背電極;涂布設備主要應用于制備鈣鈦礦吸光層、晶化;激光設備主要應用于串聯電池等,主要包括激光膜切與激光清邊。這三大設備為鈣鈦礦電池核心設備。
鈣鈦礦設備/產線投資額經濟性顯著,這也是鈣鈦礦電池技術備受資本市場追捧的關鍵之一。對比晶硅PERC電池,鈣鈦硅太陽能電池產線投資額僅為其約50%(5/9.6億)。
鈣鈦礦電池組件生產線設備構成
鈣鈦礦電池技術下,從原材料到鈣鈦礦組件僅需單一工廠即可完成,流程簡單、生產周期短;而現在主流的單晶硅技術路線,是以產業鏈形式“硅料-硅片-電池-組件”完成組件交付,流程復雜、生產周期長。
左為單結鈣鈦礦產線,右為PERC產線。
鈣鈦礦光伏電池的優勢
1、從產能投資來看,鈣鈦礦電池有巨大優勢
以1GW產能投資來對比,晶硅的硅料、硅片、電池、組件全部加起來,需要大約9億、接近10億元的投資規模,而鈣鈦礦1GW的產能投資,在達到一定成熟度后,約為5億元左右,是晶硅的1/2。
2、純度要求低,低能耗
太陽能級的硅料,純度需要達到99.9999%(6個9),現在還有把標準把純度拉升至了99.99999%的(7個9)。
但對于鈣鈦礦,只需要1個9(95%)即可滿足使用需求,這一個9,不僅會降低能耗,同時對于穩定性也會有一個根本提升。
3、制造成本低
從綜合成本角度,相比于晶硅,鈣鈦礦也有很大優勢——單片組件成本結構中,鈣鈦礦材料占比僅約為5%,總成本約為5毛到6毛錢左右,是晶硅極限成本的50%。
4、從生產端,鈣鈦礦電池的重要優勢——顯著縮短產業鏈
原文始發于微信公眾號(光伏產業通):鈣鈦礦光伏電池制備工藝