本文以液冷集裝箱式儲能系統為例,對儲能系統、儲能熱管理系統和儲能消防系統進行設計開發研究,闡述了液冷機組的設計選型,從理論和工程實踐驗證了液冷集裝箱儲能系統的優越性。
液冷儲能系統最大限度地提高了能量密度,相比于風冷儲能系統,其成本和性價比更具優勢。儲能系統以0.5C運行時,熱管理系統可以保證電池工作環境在最佳溫度范圍內。
1 儲能方案的選擇
目前,技術成熟度較高、應用較為廣泛的儲能技術為抽水蓄能和電化學儲能,電化學儲能主要是利用鋰電池技術,綜合考慮性價比、安全性、使用壽命和產業成熟度等因素,磷酸鐵鋰電池是現階段最適合用于儲能的電池。
電池起火主要由電池熱失控產生,熱失控主要是因為電池內短路,內短路的主要原因有機械濫用、電氣濫用和熱濫用,應對熱濫用的方式是采取良好的熱管理設計。
液冷技術通過液體對流換熱,將電池產生的熱量帶走,降低電池溫度。液冷的漏液風險可以通過結構設計避免,液冷的效率比風冷的效率高,液冷的溫差控制優于風冷,液冷的流體溫度和流量控制比風冷的風道控制簡單,采用液冷的電池壽命更長。
綜合成本考慮,液冷系統比風冷系統更有優勢,同時,目前儲能電站安全問題突出,液冷的儲能系統也在逐漸推廣應用。
筆者以某儲能系統工程為研究對象,采用液冷的熱管理方式,詳細論述了儲能系統的設計方案,供相關設計人員討論與交流。
2 液冷鋰電池儲能系統
鋰電池儲能系統包含電池艙和電氣艙,電池艙由電池簇、液冷系統、消防系統、匯流柜、配電箱等組成,電氣艙由變流器(PCS)、變壓器、控制柜、環網柜、交流配電柜、空調等組成,本研究詳細說明了電池艙的設計開發,對電氣艙的說明從略。
整個鋰電池儲能系統設計流程為電池包(Pack)、電池簇(Rack)、電池艙(Container),如圖1所示。
儲能系統電芯采用億緯鋰能方形鋁殼磷酸鐵鋰LF280K電芯(3.2 V/280 Ah),電池包的串并聯方式是1P48S,單個電池包有48塊LF280K電芯,電池包容量是43.008 kW·h,電池系統由8組電池簇并聯,每組電池簇由8個電池包串聯,儲能系統容量為2.75 MW·h,額定電壓為1 228.8 V。
儲能系統電池艙是標準的集裝箱20尺高柜(6.058 m×2.438 m×2.896 m),具有防水、保溫、防腐、防火、阻沙、防震、防紫外線等功能,其防護等級為IP54。
為了防止電池出現過度充電和過度放電現象,實現對電池的充放電管理,確保電池系統穩定、可靠運行,系統須配置電池管理系統(BMS),保護硬件須配繼電器、斷路器、熔斷器等。
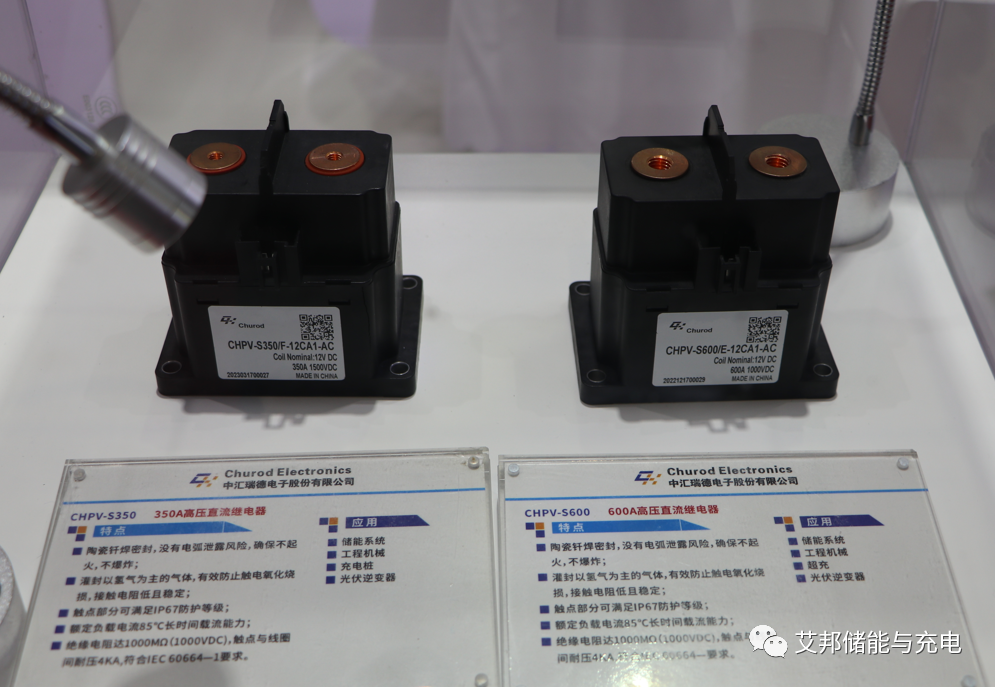
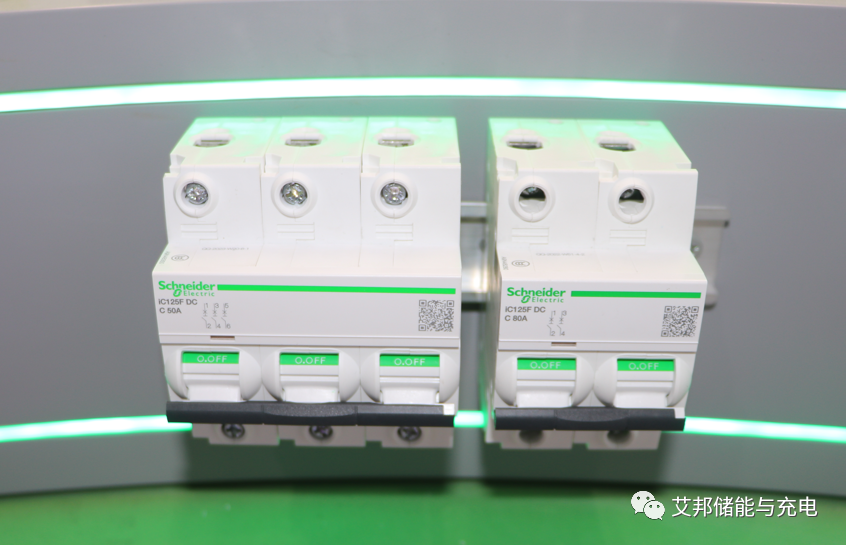
斷路器
3 儲能熱管理設計
3.1 熱管理系統設計
液冷熱管理系統由液冷板、液冷機組、液冷管路、高低壓線束和冷卻液組成,關于液冷漏液的問題,采取以下措施。
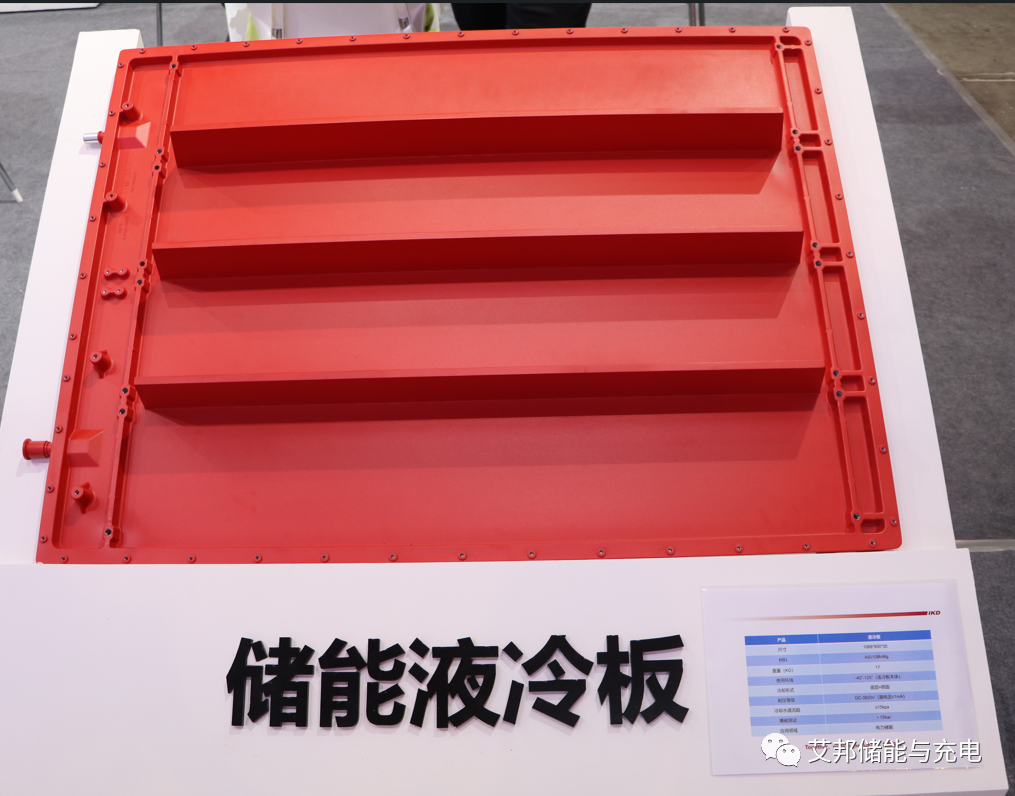
液冷板
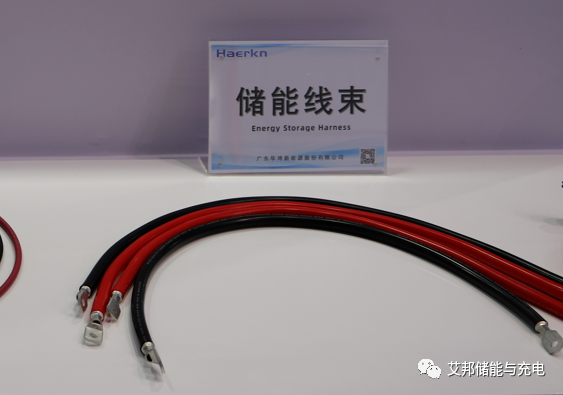
儲能線束
第一,液冷接頭采用車規級的防漏液冷卻管道快插接頭,可以保證在儲能系統運行時,漏液的風險降到最低。
第二,在液冷機組膨脹水箱設置液位傳感器,如果有漏液現象發生,液冷機組會報警。
第三,電池包設計的防護等級為IP67,保證漏液時對系統無影響,電池包的液冷板是鋁合金壓鑄一體成型,集成了底座和液冷板的功能,其中,液冷板和密封蓋板采用攪拌摩擦焊連接;
同時,液冷板也會做氣密性檢測,保證液冷板密封性能良好。電池包液冷板采用“蛇形”流道,冷卻液采用質量分數50%水+質量分數50%乙二醇,液冷系統通過一定的熱管理策略,使得冷卻液流經液冷板時,對電池包進行制冷或制熱。
儲能液冷板
液冷機組具備制冷、制熱以及除濕功能,液冷機組熱管理系統的策略和工作模式緊密相關。
當Tmax≥28 ℃、Tvag≥25 ℃時,液冷機組進入制冷模式,壓縮機開啟,高溫高壓的制冷劑從壓縮機中排出,進入冷凝器冷凝,放熱降溫后,通過膨脹閥進行節流降壓,然后進入蒸發器,并與冷卻液進行換熱,制冷劑在蒸發器中吸熱蒸發后流回壓縮機吸氣口,完成一個制冷循環。
此時,水路中的水泵開啟,PTC加熱器不開啟,冷卻液在板式蒸發器中冷卻后進入電池包液冷板,對電池進行冷卻,將熱量帶出,從而達到冷卻電池的目的。當Tmax≤25 ℃ 、Tvag≤22 ℃時,停止制冷模式。
當Tmin≤12 ℃、Tvag≤15 ℃時,液冷機組進入制熱模式,壓縮機處于關閉狀態,水泵、PTC加熱器開啟,冷卻液經過PTC加熱器加熱后,進入電池冷板,加熱電池。此模式適用于電池溫度過低時,需要對電池進行加熱的情況。當Tmin≥20 ℃、Tvag≥23 ℃時,停止制熱模式。
當進水口溫度≤12 ℃,液冷機組進入自循環模式,壓縮機、風機、PTC加熱器關閉,水泵開啟,使冷卻液在電池冷板和機組中周而復始地循環流動,將電池包中的熱量帶出。當集裝箱內濕度高于對應溫度下的露點溫度時,液冷機組開啟除濕模式。
3.2 熱管理系統設計計算
儲能集裝箱采用外維護模式,儲能系統共有8簇,其中,4簇并排在一起,另外4簇與之背靠背布置,儲能系統的液冷回路采用并聯方式,但相鄰兩個電池包采用串聯方式,各支路采用流量計獨立監控,保證各個電池包冷卻液的流速和流量均衡。
集裝箱內一些主要的熱負荷為電芯發熱功率P、電芯溫升吸熱Q,單體電芯在不同倍率下的充電或放電功率可用式(1)表示。
P0=I2×R×1.2 ? ? ?(1)
式中:I為電芯容量;R為電芯直流電阻。儲能系統設定的充放電倍率為0.5C,電芯LF280K在0.5C充電的發熱功率平均值為12.5 W,放電的發熱功率平均值為9.5 W。
儲能系統的總電芯數量為n,整個儲能系統有3 072塊LF280K電芯。
?
電芯總發熱功率(0.5C充電)為P=n×P0=12.5×3 072=38 400 W。
設置電芯的最大溫升ΔT=10 ℃,電芯的質量m=5.42×3 072=16 650.24 kg,電芯溫升發熱量可用式(2)表示。
Q=CmΔT ? ? ?(2)
式中:C為電池比熱容,kJ/(kg·℃),一般取1.055。代入得Q=175 660.03 kJ。
電池本體吸收熱功率P1=Q/t,充放電2 h,則t=7 200 s,P1=24 397 W。
液冷機組的制冷負荷P2>(P-P1)·k,其中,k為安全系數,一般取1.2~1.5,P2=19.6 kW,所以制冷功率設定為20 kW。
?
因為鋰離子電池的工作溫度為-20~50 ℃,充電溫度為0~50 ℃,所以若鋰電池在零下低溫環境中重新開始工作,就需要先預熱一段時間,將電芯溫度提升到0 ℃及以上。
?
假定環境溫度為-30 ℃,電池吸收的熱量為Q1=CmΔT1,其中ΔT1=-30 ℃,電池吸收的熱量為Q1=526 980.09 kJ,電池的吸熱功率為P2=Q1/t1,其中,t1=12 h,P2=12.2 kW,所以制熱功率設定為14 kW。液冷機組為非標定制化設計,將其制熱制冷功率參數確定下來,然后在試驗中檢驗其性能。
4 儲能消防系統
消防系統以每個電池Pack為最小防護單元,采用氣液兩相霧化滅火劑的全新滅火技術方案,聯合采用吸氣式探測器、可燃氣體探測器、感溫感煙探測器對整個儲能箱進行全方位監控、時時探測。

火災報警控制裝置
其中,吸氣式探測器以電池簇為單位對整簇電池箱進行監控防護,可燃氣體探測器對電池艙進行監控防護,感溫感煙探測器對電氣艙進行監控防護。
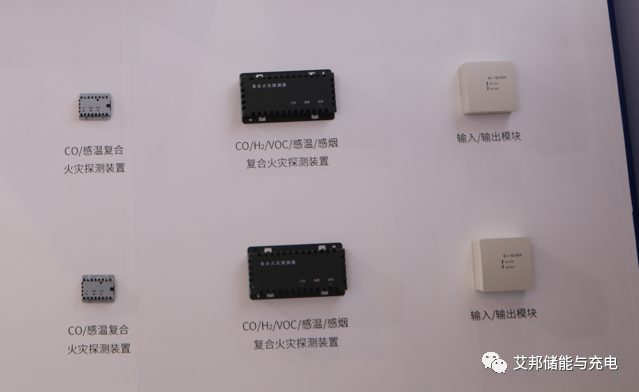
火災探測裝置
當某個電池包發生電池熱失控火災時,探測器探測到火情,探測器開啟該電池簇分區控制閥,同時將火情信息通過CAN總線傳送至火災抑制主機,聲光報警器打開,排風系統打開,抑制主機啟動輸出,滅火劑通過管路、分區控制閥輸送至氣液兩相的噴頭,滅火劑通過噴頭成霧化狀態,然后噴灑到電池包內部,實施降溫、滅火功能。
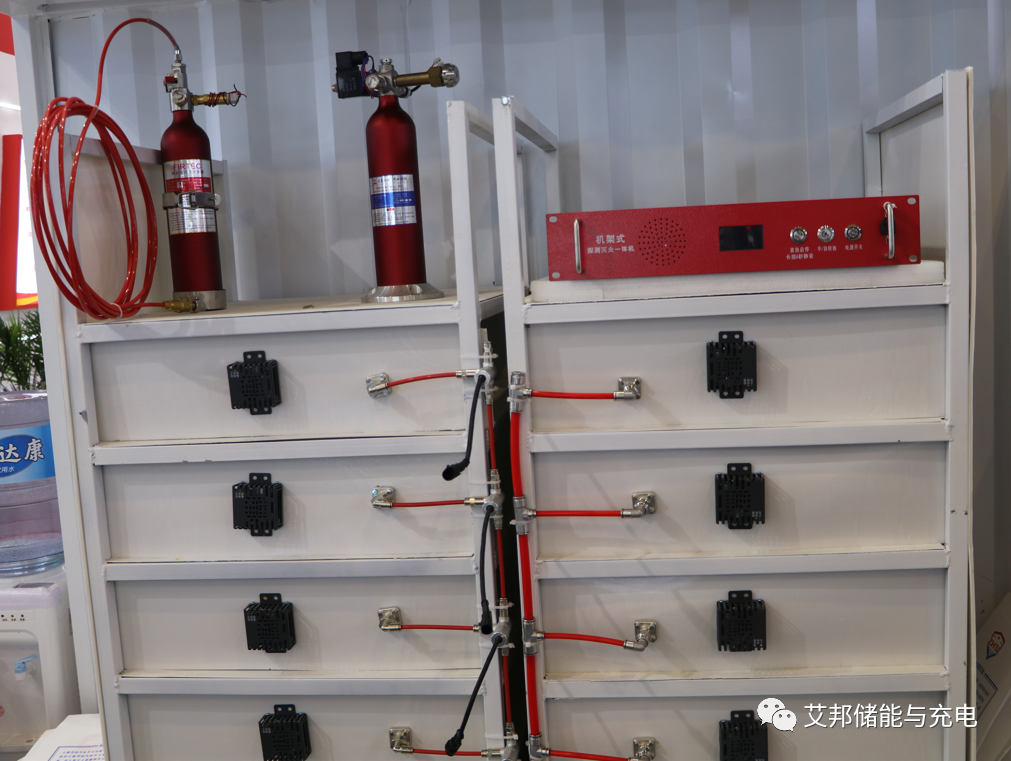
機架式探測滅火一體機
儲能火災抑制主機采用全氟己酮作為主要滅火劑,對儲能柜進行早期火災的撲滅、抑制和防控,一旦火情過大,滅火劑需要長時間噴灑,主機內部自帶的全氟己酮滅火劑使用完后,系統會自動補進消防栓水,實現長時間持續噴灑、抑制火災復燃和電池降溫的目的。
5 試驗驗證
液冷集裝箱儲能系統在環境溫度為25 ℃的情況下進行0.5C充電測試,由BMS記錄各電池包的溫度變化情況。
充電結束時,電池包內電芯表面溫度小于35 ℃,其溫升小于10 ℃,在整個充電過程中,監測點最低溫度為32.5 ℃,最高溫度為34.8 ℃,其溫差小于2.3 ℃,如圖2所示。
由圖2試驗結果可以看出,液冷集裝箱的溫升遠小于風冷集裝箱的溫差,一般風冷集裝箱的溫差達到5~8 ℃,能較好地促進整個儲能系統的溫度一致性,延長系統運行壽命。
6 結語
該工程設計了20尺液冷集裝箱儲能系統,包括系統理論設計、熱管理設計、消防設計等,最后通過試驗驗證表明,儲能系統溫度一致性較好,溫升符合要求。
液冷電池包在新能源汽車中運用非常成熟,儲能系統是靜止放置的,不會有漏液風險。液冷集裝箱系統減少了內部風道的設計,采用外維護系統,不用設置內部走廊空間,采用大電池包設計,最大限度地提高了能量密度。
從綜合成本上講,液冷集裝箱儲能系統更有優勢,儲能系統最重要的是保證其安全性,消防系統的設計是至關重要的,系統采用Pack級消防,同時采用全氟己酮+水消防持續抑制的方案,保證系統安全運行。
資料來源:《液冷集裝箱式儲能系統設計開發研究》作者:帥昌俊 武漢億緯儲能有限公司、艾邦儲能、網絡
?
?
原文始發于微信公眾號(艾邦儲能與充電):液冷集裝箱式儲能系統設計開發研究