近年來,隨著汽車外觀的設計越來越大膽、越來越科幻;為了實現設計要求,汽車內外飾注塑件正向壁厚更薄、結構更復雜、強度要求更高及外觀更精美的方向發展!傳統的恒定模溫成型技術難以適應這一發展要求,因為它極大地限制了設計人員的開發思路,使得新的設計創意難以得到實現。
為此,已在大型LCD顯示器和電子通信行業中得到廣泛應用的可變模溫成型技術現在被引入到了汽車制造業中,例如,北美福特等新車型的內外飾就是采用該技術被生產出來的。
下面,我們就來了解一下可變模溫成型技術:
不同于傳統的恒定模溫成型技術,可變模溫成型技術能夠在注塑成型的過程中,隨時根據實際生產的需要,改變模具的表面溫度,以達到優化注塑產品性能的目的。回復“注塑”,查看更多
圖1反映了可變模溫成型技術的工作階段及其與恒定模溫成型技術的對:
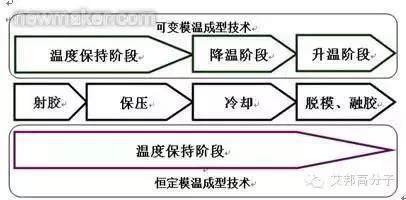
1、升溫途徑
在可變模溫成型過程中,其升溫階段可由多種方法得以實現,如水溫加熱、油溫加熱、高溫氣體加熱、蒸氣加熱、電加熱、電磁感應加熱和氣體燃燒加熱等。
由于水溫加熱的最高溫度太低,油溫加熱會產生油氣問題,電磁感應加熱不適用于大型制件,氣體燃燒加熱對成型設備的要求較高,因此市場上常見的加熱手段以電加熱和蒸氣加熱為主。隨著技術的發展,目前還出現了紅外線加熱及激光束直接加熱等新的加熱技術。
2、降溫途徑
對于可變模溫成型的降溫階段,實現的手段通常比較單一,主要利用冷卻水來冷卻降溫。
由于具有諸多的優點,使得可變模溫成形技術為汽車內外飾注塑件的成形帶來了突破性的進步。
在此,以韓國NADA公司的電加熱控制技術(E-Mold)為例,來介紹可變模溫成形技術在汽車內外飾生產中的應用優勢,主要有以下7點:
1、成型周期更短
可變模溫成形技術通過快速升溫和降溫,可以將成形周期控制在更短的時間內。一般小零件的成形周期在30s以內,大型零部件的成形周期在60s以內,即使一些成形溫度特別高的結晶型塑料,其成形周期也可被控制在120s以內。
圖2顯示了燃料電池分隔器的成形周期溫度變化情況:橫坐標為時間(s),縱坐標為溫度(℃),其成型周期只有120秒左右。
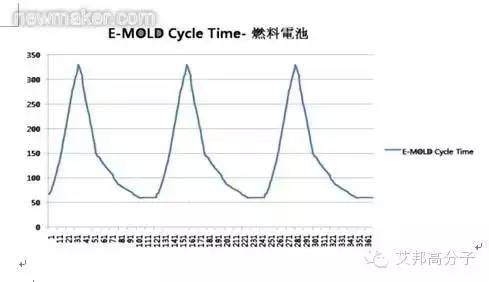
2、獲得普通噴漆難以實現的鋼琴漆效果
汽車內外飾注塑件的免噴涂目前已成為汽車行業的一個發展趨勢。現在,汽車內飾件的設計也借鑒了高光澤家電外殼的設計經驗,將高光澤鏡面效果引入設計中。
例如,對于一些運動型SUV車型使用的內飾件,設計者采用高光澤ABS合金或PC合金來制造儀表板控制器和副儀表板面框,以及車門扶手裝飾板等內飾件,并將PMMA材料創新性地應用于汽車外飾,如車門中柱飾板等。這些材料改變了汽車內飾傳統的亞光、柔和的設計風格,使其更活潑、更動感且更銳利。
圖3所示為福特新翼虎的內飾,相比上一代而言,外觀有較大的改善。
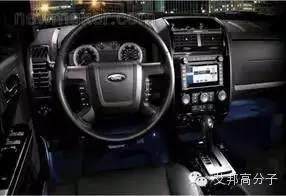
3、提高塑件的皮紋均勻性
以大眾汽車的標準皮紋為例,K31和K48皮紋是其具有代表性的細皮紋和粗皮紋。在試驗中,采用了上海錦湖日麗塑料有限公司提供的亞光級PC/ABSHAC8250Z作為基材,并分別采用可變模溫成形技術和恒定模溫成形技術對該材料進行成形加工。
結果,經兩種成形技術生產出的產品的亞光程度具有明顯的區別,見表1。
表1:不同成型技術對皮紋的復制性的區別
注塑過程中產生的內應力通常是造成汽車零部件在成形后發生翹曲的主要原因。在制件成形后,由于應力難以釋放,因而導致了開裂、變形等諸多問題。
如果采用可變模溫成形技術,可以在熔體填充型腔的過程中,通過將模溫控制在材料的熔點溫度以上,來有效地防止內應力的產生。圖4所示上圖為薄壁多孔結構的應力變形情況,下圖為采用可變模溫成形技術得到的制品。
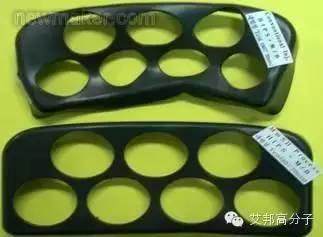
推薦閱讀:
5、改善塑件熔接線外觀,提高強度
利用可變模溫成形技術,可以有效地改善塑件在熔接線位置處的外觀。
以E-Mold成形的車門扶手控制面板為例,所用材料為PC/ABS。在生產中,分別采用了開啟E-Mold溫度控制器的可變模溫成形技術和關閉控制器的恒定模溫成形技術。
采用可變模溫成形時,由于塑料熔體在充模時的鋒端保持在較高溫度上,所以在熔接痕處的分子排列更有序,分子間的交聯更緊密,反映在塑件外觀上,則表現為熔接痕較輕甚至消失,反映在力學性能上,則表現為熔接線的強度更高。
圖5上圖為熔接痕的手繪示意圖,下圖為通過用硬幣的模擬實驗,直觀地表示出了熔接痕的產生機理;圖6為兩種成型技術制品的微觀圖。
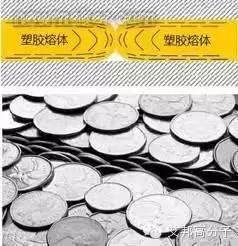
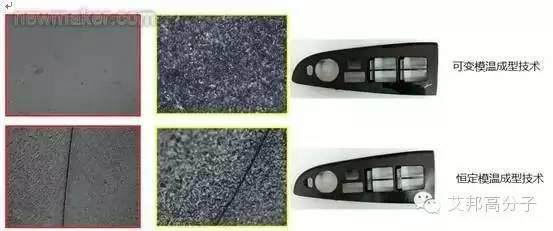
圖6:用可變模溫成形技術成形出的高光面和皮紋面的熔接痕100倍顯微鏡照片
6、提高塑件的可電鍍性能
很多汽車內外飾零部件都需要使用電鍍工藝,如:散熱格柵、車門把手、尾門飾條、儀表板飾圈、換擋桿飾圈和內門扣手等。在塑料電鍍的過程中,粗化是很重要的一環,粗化的好壞將直接影響到鍍層的結合力、光亮度和完整性。粗化時,通過CrO3的氧化作用,溶解出丁二烯,在樹脂表面上形成1~2μm的錨坑。丁二烯的氧化分解賦予樹脂表面以羧基等極性基,有利于膠體鈀的吸附和后續鍍層的附著力。
粗化前,塑件表面的平整程度將直接影響粗化液的刻蝕效果。在模具表面的拋光級別相同的情況下,利用可變模溫成形技術,可以使塑件的表面更光滑,粗化后的刻蝕更均勻,塑件的殘余應力更小。相對于傳統的注塑工藝,塑件的電鍍良率更高。回復“注塑”,查看更多
圖7、圖8分別為塑料粗化環節的電鏡照片和不同成形工藝對粗化影響的電鏡照片。
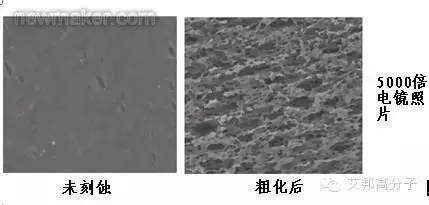
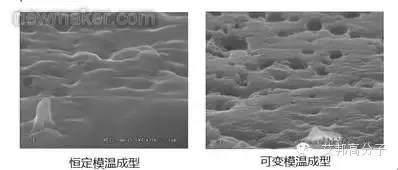
7、實現含玻纖材料的高光澤表面
在汽車零部件中,為達到設計強度的要求,經常會使用如PA+玻纖或者PBT+玻纖等材料。
通常,這些零件只能作為結構件使用,因為表面浮纖使其難以被用于外型面上。而利用可變模溫成形技術,可以有效地控制材料的玻纖外露問題(如圖9所示),從而可以用含玻纖材料直接注塑成形汽車的內外飾件。通過采用獨特的材料改性手段,利用E-Mold技術實現了PC+30%玻纖的鋼琴漆黑亮效果,如圖9所示:
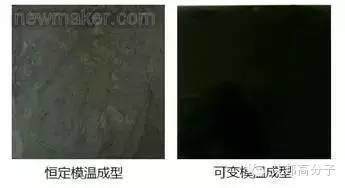
圖9 可變模溫成形技術對玻纖外露的改善
總之,可變模溫成形技術所具有的這種可實現高玻纖含量產品的高光澤表面效果的優勢是其他成形技術難以企及的。在傳統設計中,對于具有一定強度要求的結構件,通常會選用加玻纖的結晶型工程塑料或聚碳酸酯合金材料,這些材料通常具有很好的抗彎強度和沖擊強度。但是,由于玻纖含量通常超過30%,因此,當采用恒定模溫成形時,制件表面的浮纖無法消除,從而限制了加玻纖材料在外觀件上的應用。
利用可變模溫成形技術,可以實現加玻纖材料在外觀件上的應用,或者也可實現結構件和外觀件的一體化設計。這樣的設計不僅可以減少零部件的數量,也可降低部分零部件的設計難度,減少裝配工序,并有效控制成本。圖10所示為PC+30%GF材料的玻纖外露狀況顯微鏡照片。
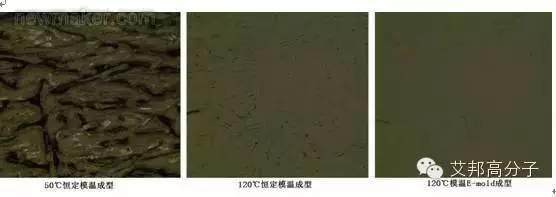
由于可變模溫成形技術的諸多優點,目前已有部分主機廠在設計中引入了這項技術,試圖實現更多的設計理念,豐富內外飾件的材料選擇。
表2顯示了一些較成功的應用案例。
表2可變模溫成形技術的實用案例
實際上,韓國NADA公司的E-Mold技術在可變模溫成形的應用中也有其局限性。
首先,由于采用的是預埋電加熱棒的模具技術,所以無法對現有的模具進行改造利用;
其次,預制的加熱棒形狀的可塑性較小,無法實現與大曲率曲面和深孔面的配合,限制了其應用;模具成本的上升導致單個制件的平攤成形成本增加,使其在小批量特殊產品上的應用受到成本限制。
綜上所述,可變模溫成形技術作為一種較為成熟的注塑工藝,正在從傳統的家電、通信行業進入汽車行業中。配合適用于高模溫成形的改性工程塑料,這項技術必將為汽車內外飾件的設計帶來更多的創意。
加入注塑微信群,請加微信:13058121209或18681464439,注明“注塑+公司”
推薦閱讀:
閱讀原文加入我們
↓↓↓
始發于微信公眾號:艾邦高分子