動(dòng)力電池包是電動(dòng)汽車(chē)核心零部件之一,其內(nèi)部由大量電池單體通過(guò)串并聯(lián)方式形成模組、系統(tǒng),電池包重量約占整車(chē)總重 20-30%,生產(chǎn)成本約為整車(chē) 50%。電動(dòng)汽車(chē)安全事故中絕大部分是電池包故障導(dǎo)致,如碰撞中電池包變形嚴(yán)重引發(fā)單體內(nèi)短路、充放電中單體溫升異常誘發(fā)熱失控等。
電動(dòng)汽車(chē)的快速發(fā)展對(duì)動(dòng)力電池包提出了嚴(yán)苛的要求,如超長(zhǎng)續(xù)駛里程、高比功率與高比能量指標(biāo)、高安全性和可靠性要求。
研究數(shù)據(jù)表明,傳統(tǒng)燃油汽車(chē)減重10%,經(jīng)濟(jì)性可提升 6-8%;而等速行駛工況下電動(dòng)汽車(chē)自重降低10%,可使整車(chē)增加10%左右的續(xù)駛里程。
車(chē)用動(dòng)力電池包可通過(guò)單體比能量提升、箱體結(jié)構(gòu)輕量化、制造工藝改善等方式來(lái)增加整車(chē)?yán)m(xù)駛里程。單體比能量受電芯內(nèi)部材料組分和外部尺寸限制,在短期內(nèi)難以有突破性的進(jìn)展;電池包結(jié)構(gòu)輕量化設(shè)計(jì)可減輕重量從而增加整車(chē)?yán)m(xù)駛里程,因此箱體輕量化與模組緊湊化設(shè)計(jì)無(wú)疑是提升續(xù)駛里程的可行途徑。
電池包輕量化設(shè)計(jì)主要有系統(tǒng)設(shè)計(jì)層級(jí)與詳細(xì)設(shè)計(jì)層級(jí)中多種途徑,如圖所示。
? ? ? ?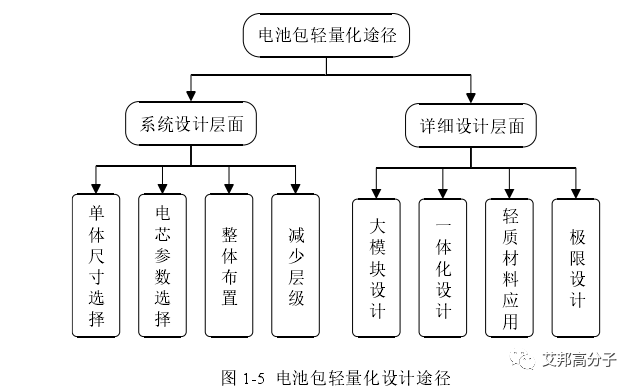
電池包結(jié)構(gòu)設(shè)計(jì)需滿足各項(xiàng)機(jī)械安全、密封絕緣和防火等性能要求。箱體結(jié)構(gòu)強(qiáng)度、剛度、耐撞性、可靠性等性能以及內(nèi)部模組布置等因素均會(huì)對(duì)電池包性能產(chǎn)生影響。理想的動(dòng)力電池包結(jié)構(gòu)設(shè)計(jì)應(yīng)滿足電動(dòng)汽車(chē)各項(xiàng)性能要求下最大程度減輕自身重量。其中較為有效的方式有以下五種。
在電池包箱體有限空間內(nèi),一定數(shù)量電池單體通過(guò)特定機(jī)械連接和電連接組成電池模組,根據(jù)車(chē)用電池包的空間形狀與承載特點(diǎn),電池模組串并聯(lián)排布組成動(dòng)力電池系統(tǒng),電池包中模組布置和結(jié)構(gòu)形式差異較大。
電池單體常用類(lèi)型有圓柱形、方形鋁殼和軟包鋁塑膜等,此外電池包內(nèi)部還布置有BMS控制器、高壓線束等輔助功能部件。
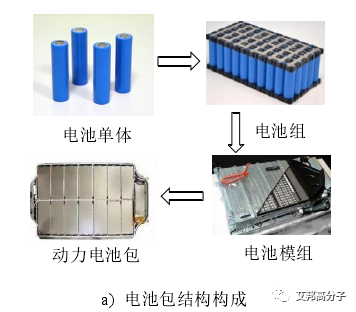
? ? ? ? ? ? ? ? ? ? ? ? ? ? ? ?
??
動(dòng)力電池包的布置形式通常由整車(chē)空間特征決定,需考慮車(chē)輛驅(qū)動(dòng)方式、整車(chē)重心位置與離地間隙等因素。
動(dòng)力電池包生產(chǎn)企業(yè)根據(jù)整車(chē)企業(yè)需求,開(kāi)發(fā)出模組排布不同、電池包箱體形狀和安裝吊耳位置各異的車(chē)用動(dòng)力電池包。經(jīng)過(guò)不斷研究與發(fā)展,電池包常用結(jié)構(gòu)布置形式有車(chē)身底部懸置式、車(chē)身結(jié)構(gòu)一體式和標(biāo)準(zhǔn)箱體分布式等。
早期電動(dòng)汽車(chē)多由傳統(tǒng)燃油車(chē)改裝而成,動(dòng)力電池包通常安裝在汽車(chē)前艙、后備箱、地板底部等位置,如圖 1-2 所示的日產(chǎn) Leaf“凹”形電池包。車(chē)身底部懸置式電池包采用螺栓連接于汽車(chē)車(chē)架底部,具有設(shè)計(jì)高效靈活、生產(chǎn)制造獨(dú)立性好等優(yōu)點(diǎn),是乘用車(chē)廣泛采用的動(dòng)力電池包結(jié)構(gòu)形式,如日產(chǎn)Leaf、眾泰云EV和吉利帝豪EV。
? ? ? ?
? ? ? ? ?
標(biāo)準(zhǔn)箱體分布式是通過(guò)幾個(gè)相同或者結(jié)構(gòu)近似的標(biāo)準(zhǔn)箱體電池包串并聯(lián)形成電池系統(tǒng),具有布置靈活,安裝位置多樣等特點(diǎn),空間較大且規(guī)整的客車(chē)或?qū)S闷?chē)多采用該種結(jié)構(gòu)形式,如宇通E10 純電動(dòng)客車(chē),如圖1-3 所示。
? ? ? ?
? ? ? ?
隨著電動(dòng)汽車(chē)?yán)m(xù)航里程的需求不斷提高,空間受限的傳統(tǒng)汽車(chē)結(jié)構(gòu)無(wú)法滿足最優(yōu)設(shè)計(jì)要求,車(chē)身結(jié)構(gòu)一體式電池包結(jié)構(gòu)布置形式逐漸受到重視,電動(dòng)汽車(chē)正向設(shè)計(jì)技術(shù)的成熟使得電動(dòng)汽車(chē)專(zhuān)用設(shè)計(jì)平臺(tái)出現(xiàn),如圖 1-4 所示的廣汽 GEB 電動(dòng)汽車(chē)專(zhuān)用設(shè)計(jì)平臺(tái)。
? ? ? ? ? ? ? ?
? ? ? ?
電動(dòng)汽車(chē)?yán)m(xù)駛里程需求增加和汽車(chē)正向設(shè)計(jì)技術(shù)提升促使車(chē)身設(shè)計(jì)與電池包結(jié)構(gòu)協(xié)同開(kāi)發(fā),力求車(chē)身結(jié)構(gòu)緊湊同時(shí)電池包性能較優(yōu),平臺(tái)化、模塊化的車(chē)身結(jié)構(gòu)一體式動(dòng)力電池包逐漸增多,如搭載大眾MEB平臺(tái)的奧迪Q4 e-tron、特斯拉TESLA平臺(tái)設(shè)計(jì)的Model S和Model X等車(chē)型。
系統(tǒng)設(shè)計(jì)層面下電池包輕量化設(shè)計(jì)首先從電芯參數(shù)和單體尺寸選擇開(kāi)始,不同化學(xué)體系與尺寸參數(shù)下鋰離子動(dòng)力電芯與動(dòng)力電池系統(tǒng)存在匹配設(shè)計(jì)問(wèn)題,通常需在電池系統(tǒng)概念設(shè)計(jì)階段計(jì)算確定。然后通過(guò)優(yōu)化電池包箱體內(nèi)部布置、減少設(shè)計(jì)層級(jí),實(shí)現(xiàn)箱體空間最大利用率,例如,寧德時(shí)代(CATL)提出的無(wú)模組設(shè)計(jì)技術(shù)(Cell To Pack CTP),圖 1-6為CATL 某種CTP系統(tǒng)結(jié)構(gòu)設(shè)計(jì)。
? ? ??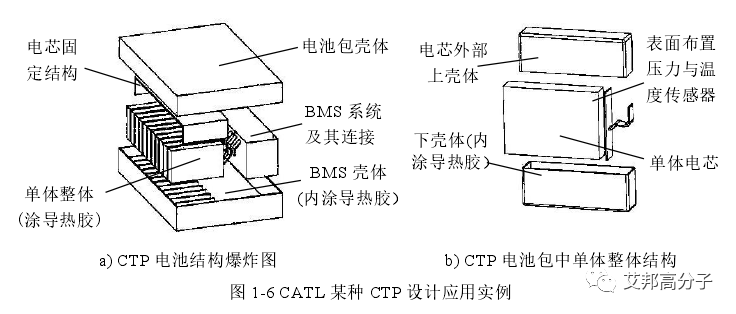
CATL在該CTP設(shè)計(jì)中采用單體和電池管理系統(tǒng)直接固定在電池包殼體中,電芯內(nèi)置在上下殼體中,殼體內(nèi)部填充導(dǎo)熱膠,電芯側(cè)壁和電芯殼體間內(nèi)置壓力或者溫度傳感器,兩種傳感器協(xié)同作用下能夠排查不良電芯單體,并且提前探測(cè)到電芯可能發(fā)生熱失控等安全事故。
該設(shè)計(jì)形式不采用模組結(jié)構(gòu),使電池包體積利用率提升了15%-20%;電芯單獨(dú)裝配,降低裝配難度,提高生產(chǎn)效率約 50%;同時(shí)實(shí)現(xiàn)故障電芯的及時(shí)檢測(cè)與更換,電芯殼體加強(qiáng)方案可降低電池包外殼的防護(hù)等級(jí)。
將單體電芯的尺寸和容量增加,致使每個(gè)單體電芯分?jǐn)偟慕Y(jié)構(gòu)件質(zhì)量減少。例如,CATL大模組設(shè)計(jì)結(jié)構(gòu),參見(jiàn)圖 1-7,通過(guò)大模組設(shè)計(jì)取消了現(xiàn)有技術(shù)中的電池箱體,直接將電池模組通過(guò)固定件穿過(guò)支撐套筒與安裝梁安裝在整車(chē)上,實(shí)現(xiàn)電池包輕量化同時(shí)提高了電池包在整車(chē)上連接強(qiáng)度。
? ? ? ? ? ? ? ?
? ? ? ? ?
減少電池包模組等中間層級(jí),將單體電芯尺寸做到最佳,提高箱體空間利用率。例如,比亞迪(BYD)提出的“刀片電池”電池包設(shè)計(jì)方案,如圖所示,通過(guò)設(shè)計(jì)出一種扁平化大尺寸電芯,采用陣列排布方式布置于電池包箱體內(nèi)部,單體電池就像“刀片”一樣插入到電池包中,該設(shè)計(jì)能使電池包比能量提升50%左右,生產(chǎn)成本降低約30%。
? ? ? ? ? ? ? ?
? ? ? ? ?
目前鋰離子單體電芯能量密度提升緩慢,箱體減重設(shè)計(jì)是十分有效的電池包輕量化途徑,而輕質(zhì)材料應(yīng)用對(duì)電池包箱體減重效果十分明顯。
目前應(yīng)用較為成熟的輕質(zhì)材料有鋁鎂合金和復(fù)合材料兩大類(lèi),鋁、鎂、鈦合金是目前金屬材料體系中密度較小的輕質(zhì)材料。鋁合金具有重量輕、回收利用、抗氧化性好,是目前輕質(zhì)電池包箱體的常用材料,考慮到箱體結(jié)構(gòu)強(qiáng)度的影響,壓鑄型鋁箱與擠壓-拼焊鋁箱多用在電池包下箱體,沖壓-拼焊鋁箱一般用在電池包上箱蓋,如圖所示。
? ? ? ?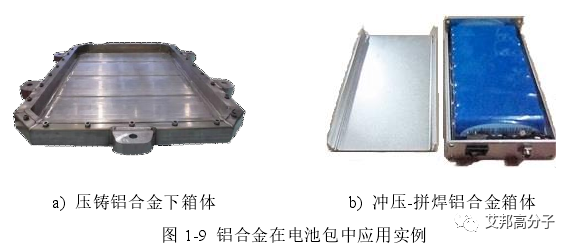
復(fù)合材料顯著特征是重量輕、絕緣性好及成型加工簡(jiǎn)便,各種復(fù)合材料制成的汽車(chē)零部件正在替代部分金屬零部件,如發(fā)動(dòng)機(jī)罩、油底殼、電池包上箱蓋等。復(fù)合材料在電池包中應(yīng)用實(shí)例如圖所示。
? ? ? ?
? ? ? ? ?
復(fù)合材料受制于原材料、生產(chǎn)成本等因素,目前電池包中應(yīng)用較多的復(fù)合材料有玻璃纖維增強(qiáng)塑料(SMC)、改性樹(shù)脂等,SMC制成的電池包上箱蓋比傳統(tǒng)金屬材料上蓋減重約為38%,碳纖維復(fù)合材料(CFRP)應(yīng)用也在逐漸增多,復(fù)合材料減重效果明顯。
部分企業(yè)嘗試將復(fù)合材料應(yīng)用在電動(dòng)汽車(chē)下底板,但復(fù)合材料剛度特性較差,需要加厚尺寸或者采用夾層結(jié)構(gòu)來(lái)提升結(jié)構(gòu)的抗彎特性,電池包下箱體設(shè)計(jì)成夾層結(jié)構(gòu)并在中間層增加金屬或者蜂窩鋁結(jié)構(gòu),具有輕質(zhì)高強(qiáng)、耐撞性好等諸多優(yōu)點(diǎn)。
極限設(shè)計(jì)是指在產(chǎn)品詳細(xì)設(shè)計(jì)階段進(jìn)行性能優(yōu)化或后期對(duì)產(chǎn)品進(jìn)行設(shè)計(jì)改良,極限設(shè)計(jì)需清楚設(shè)計(jì)的臨界值,不僅要滿足各項(xiàng)性能要求,還需滿足零部件加工、產(chǎn)品裝配工藝要求。
極限設(shè)計(jì)通常借助計(jì)算機(jī)輔助設(shè)計(jì)(CAE)對(duì)產(chǎn)品各項(xiàng)性能臨界值和生產(chǎn)工藝參數(shù)探索,通過(guò)CAE仿真分析技術(shù)精準(zhǔn)定位,例如將電池包箱體承載部位加強(qiáng)設(shè)計(jì),而非承重部位使用薄壁材料,箱體不同位置變厚度實(shí)現(xiàn)結(jié)構(gòu)性能滿足設(shè)計(jì)要求又盡可能減重。
? ? ? ?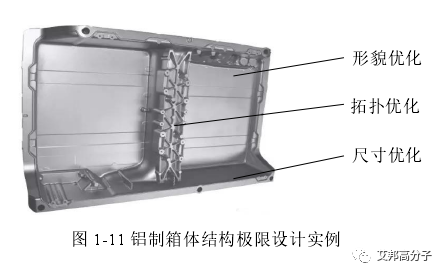
多材料電池包結(jié)構(gòu)優(yōu)化現(xiàn)狀
輕質(zhì)材料應(yīng)用在電池包結(jié)構(gòu)輕量化中具有較為明顯的減重效果,目前動(dòng)力電池包設(shè)計(jì)中常用的輕質(zhì)材料有鎂鋁合金、復(fù)合材料和工程塑料等,下表為常用輕質(zhì)材料性能參數(shù)及特點(diǎn)。
? ? ? ?
? ? ? ? ?
鎂鋁合金、復(fù)合材料等輕質(zhì)材料在電池包結(jié)構(gòu)輕量化設(shè)計(jì)中減重效果顯著,但目前輕質(zhì)材料應(yīng)用在電池包結(jié)構(gòu)設(shè)計(jì)中存在以下不足:1) ?結(jié)合電池包關(guān)鍵性能開(kāi)發(fā)出性能和輕量化效果均優(yōu)的電池包結(jié)構(gòu)欠缺,可借鑒的研究成果、設(shè)計(jì)方法不多;2) 合適的材料用在合適的位置在電池包結(jié)構(gòu)設(shè)計(jì)中已有初步應(yīng)用,但對(duì)電池包多材料選型方法,結(jié)合性能約束的多材料設(shè)計(jì)方法研究不足。
參考素材:車(chē)用動(dòng)力電池包多材料結(jié)構(gòu)優(yōu)化與輕量化設(shè)計(jì),陳元
原文始發(fā)于微信公眾號(hào)(艾邦高分子):電池包結(jié)構(gòu)輕量化的5種關(guān)鍵方法