每年12月,Composites World雜志均會撰寫系列文章介紹當年復合材料在不同應用領域如航空航天、體育休閑、壓力容器、可再生能源等的應用最新進展情況,并對新一年的發展進行展望。本文概述了2022年復合材料在電子產品領域的市場分析。
彭博新能源財經在2022 年 6 月的一篇文章中稱,內燃機 (ICE) 汽車銷量在 2017 年達到頂峰,隨著政府和原始設備制造商加速宣布淘汰化石燃料汽車,化石燃料汽車越來越多地被電池電動汽車 (BEV) 和燃料電池電動汽車 (FCEV) 所取代。電動汽車 (EV) 的增長為電池外殼和燃料電池組件中的復合材料提供了機會。
根據ev-volumes.com 發布的 Global EV Sales for 2022 H1報告,2022 年電動汽車總銷量預計將超過 1060 萬輛,比 2021 年增長 57%。年中分析表明,到 2025 年電動汽車可能占全球汽車銷量的 20% 以上,并且到 2035 年將接近 60%。
但這已經足夠了,能源創新政策和技術執行董事(美國加利福尼亞州舊金山)Arnand R. Gopal 在 2022 年 12 月的福布斯文章中說。為了到 2050 年實現凈零排放,到 2030 年新乘用車銷量的 60% 必須是零排放汽車 (ZEV),到 2035 年達到 100%。
到 2022 年,全球每月電動汽車銷量將增長 57%。
圖片來源:https ://www.ev-volumes.com/
隨著原始設備制造商試圖增加 BEV 的行駛里程,復合材料有助于抵消電池重量,同時通過輕型電池外殼提高安全性。
例如,帝人汽車技術(美國密歇根州奧本山)在北美、歐洲和亞洲擁有壓塑復合電動汽車電池蓋和全外殼十多年,主要使用短纖維/熱固性片狀模塑料 (SMC)。不過,該公司已開始探索使用樹脂傳遞模塑 (RTM) 和濕壓模塑工藝的連續增強材料。帝人也在研究混合材料方法,使用長纖維局部增強短切纖維材料,并致力于為其更高容量的材料創建材料卡(用于模擬軟件)以幫助其客戶開發新產品。
麥格納國際公司(加拿大安大略省奧羅拉)最近通過其 麥格納外飾部門贏得了于 2024 年開始生產的第一個復合電池蓋項目。自 2019 年以來,該部門與 OEM 一起參與復合電池外殼的開發活動,專注于使用阻燃 (FR) 不飽和聚酯 (UP) 或乙烯基酯 (VE) 樹脂的模壓 SMC。然而,隨著電池能量密度的不斷提高,麥格納正在滿足更多對復合材料的需求,這些復合材料具有更高的耐火性和更高的溫度,以及能夠承受長達五分鐘的熱失控事件的內部壓力,從而滿足不斷發展的全球標準。這推動了人們對具有更高耐溫性的酚醛樹脂的興趣。麥格納和帝人都提到了這種對酚醛樹脂的興趣。麥格納還開發了正在申請專利的多材料外殼解決方案,采用 FR 復合材料蓋和結合了鋁和復合材料的混合托盤。
STS Group AG(德國哈根)自 2019 年以來已為中國的多個項目供應 SMC 電池蓋,并且計劃于 2023 年在西歐推出的項目即將投產。該公司于 2022 年開始在弗吉尼亞州建設新的 SMC 模塑工廠。STS Group 也看到了提高性能的需求,因此花了三年時間驗證酚醛和環氧樹脂基體與連續玻璃纖維或碳纖維,這些基體在長時間暴露于高溫后仍能提供殘余的機械性能。
復合材料風力葉片生產商TPI Composites Inc.(美國亞利桑那州斯科茨代爾)也在生產復合材料電池外殼組件,包括用于多個地區的大型項目,以及為預計將于 2023 年至 2024 年推出的 4-8 級電動卡車開發電池外殼。該公司花了六年時間開發和驗證各種材料/工藝選項,以滿足一系列質量、成本和其他性能要求。這些主要基于浸漬酚醛或高溫阻燃環氧樹脂的連續纖維(玻璃、碳或混合物),用于高壓 RTM、濕復合成型和其他技術。
Tier 供應商Kautex Textron?GmbH & Co. KG?考泰斯(德國波恩)與材料供應商Lanxess AG(德國科隆)合作探索使用熱塑性復合材料替代大型 EV 電池外殼上的鋼和鋁。對于 C 級(中型)轎車,合作伙伴展示了一個 1,400 × 1,400 毫米的電池外殼,包括一個連接到整體碰撞結構的托盤和底部保護裝置以及頂蓋。組件是使用 Durethan B24CHM2.0 玻璃纖維增強 PA6 和壓縮 D-LFT(長纖維熱塑性塑料)制成的,這是一種非常適合快速且經濟地生產大型零件的一步法。托盤的防撞結構采用 Tepex dynalite 連續玻璃纖維增強 PA6 局部增強,以滿足高結構要求。金屬外殼不僅笨重,而且由于尺寸、組件數量以及許多制造和組裝步驟(包括焊接、沖孔和鉚接)而價格昂貴,它們還必須通過陰極浸漬涂層進行防腐蝕保護。而復合材料則具有耐腐蝕和電絕緣性,可降低短路風險,還可以集成緊固件和熱管理組件,從而減少組件數量并簡化組裝和物流,從而降低成本和重量。
Kautex Textron 和 Lanxess 合作開發了全熱塑性復合材料 EV 電池外殼(上圖),而 Ballard Power 繼續使用復合材料并隨著全球需求的增長而提高其燃料電池制造能力(下圖)。
圖片來源:Kautex Textron GmbH & Co. KG 和 Ballard Power
LyondellBasell Industries(美國德克薩斯州休斯頓)自 2016 年以來一直為商用 EV 電池外殼項目提供 SMC。營銷經理 Justin McClure 指出,外殼正在成為車輛結構的一部分,對熱事件管理的要求也變得更加嚴格,推動公司向更先進的材料發展。LyondellBasell 已將其 Forged Preg 連續單軸、雙軸和三軸碳纖維增強混合 SMC 與其高強度 Premi-SMC 和高溫 Quantum-ESC SMC 等級共同成型,以優化質量和性能。他指出,盡管 SMC 的初始材料成本較高,但與必須進行機加工、涂層和組裝的多件金屬沖壓件、鑄件和擠壓件相比,壓縮工具對于 <50,000 件/年的項目來說成本更低。例如,與鋼沖壓件相比,30,000 個零件/年的加工成本通常可節省 35%,40,000 個零件/年可節省 20%。
三菱化學集團公司(MCG,日本東京)已在全球范圍內為復合電動汽車電池外殼供應材料,包括其 GMT 和 GMTex 材料。該公司正在開發創新的多功能材料以承受熱失控事件,例如用于電池外殼的新型 FR 熱塑性復合材料已通過在 1,000°C 火焰中暴露超過五分鐘的測試。它還在探索將生物基熱固性樹脂系統用于其玻璃和碳纖維增強預浸料。
電池外殼中的熱塑性復合材料。在 GMT 和 GMTex 有機片材復合材料中模壓成型的生產電動汽車電池蓋的 A 面和 B 面。圖片來源:三菱化學先進材料
SABIC(沙特阿拉伯利雅得)為本田汽車在中國市場推出的電動汽車電池組蓋提供了阻燃短玻璃纖維增強聚丙烯 (PP) 樹脂。該化合物遇火形成膨脹炭,具有自熄性,率先通過新國標GB 18384-2020。
與需要隔熱毯,會顯著增加重量、成本和環境問題的金屬電池外殼相比,SABIC 的注塑熱塑性塑料可減輕 40% 的重量,有助于延長行駛里程,同時功能集成,可簡化組裝,并降低成本。該部件還可以在使用壽命結束 (EOL) 時完全回收利用,并且二氧化碳排放量更小。SABIC 認為 FR 熱塑性塑料有可能在電池外殼中占據更大份額,因為它們具有固有的熱絕緣和電絕緣、膨脹特性、輕量化、部件集成和潛在的部件消除,這有助于降低成本。例如,已經探索了電池托盤,其中模制冷卻通道可以減輕 60 千克的重量并節省 50% 的成本。
2021 年 12 月,AZL Aachen(德國)領導了一個由 46 個工業合作伙伴組成的聯盟,完成了為期一年的多材料電池外殼設計項目。定義了電池外殼的五個子組件:外殼托盤、底部保護板、防撞框架、橫梁和外殼蓋。合作伙伴對總共 44 個與市場相關的現有系列組件和概念進行了更詳細的分析,并編制了國家、國際和 OEM 級別的標準和要求的綜合概述,目標是實現與傳統解決方案相同或更好的機械性能。AZL 開發了 20 種不同材料組合的設計概念,包括熱塑性塑料和熱固性材料、SMC、拉擠型材、織物、單向 (UD) 材料、三明治(泡沫、蜂窩和 D-LFT 芯),以及 LFT 和混合包覆成型(膠帶 +注塑成型)。通過創建 500 多個有限元模型并執行 1,500 多個 CAE 仿真來分析這些設計。結果表明,與傳統解決方案相比,多材料復合材料最多可減輕 36% 的重量,最多可節省 20% 的成本。該項目設立了將于 2022 年完成的后續項目,包括示范原型的制造以及底部沖擊保護和防火研究。
根據國際能源署 (IEA) 在其報告“ 2021 年全球氫評論”第 83 頁的分析,到 2021 年底,燃料電池產能預計將超過 200,000 個系統/年,由 40 多家制造商提供。然而,IEA 的這一單位數量遠高于能源和可持續發展咨詢公司 E4tech(英國倫敦)在其 2022 年 7 月發布的“2021 年燃料電池行業評論”中報告的約 86,000 燃料電池出貨量。
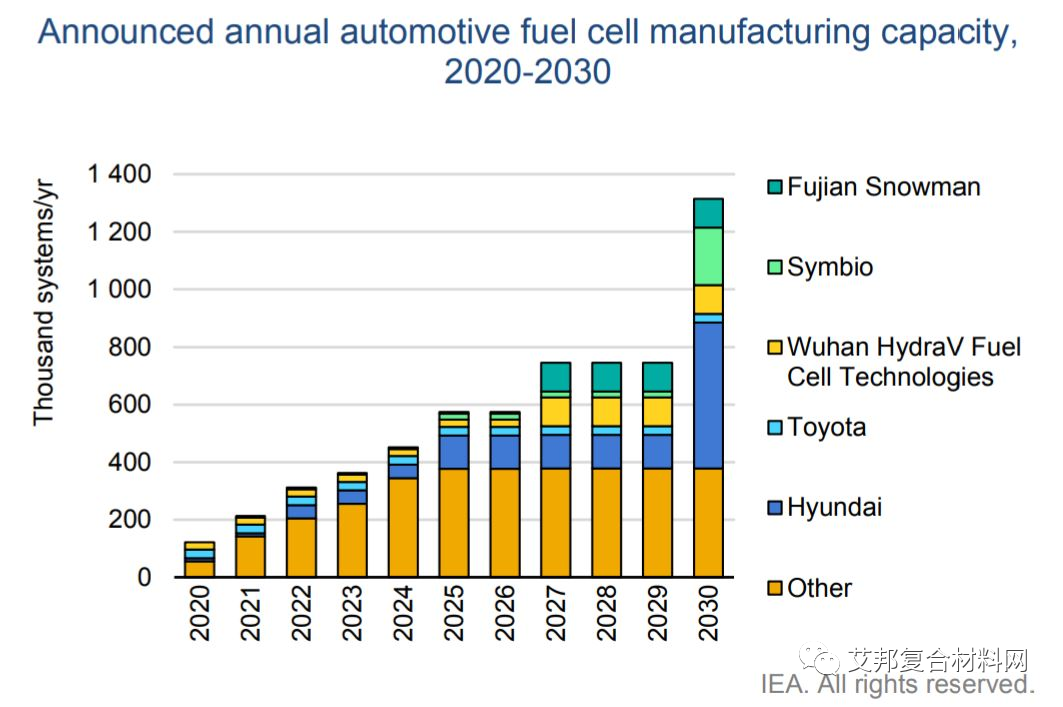
預計燃料電池的增長。圖片來源:國際能源署 (IEA)??《2021 年全球氫評論》第 83 頁, E4tech
盡管市場估計各不相同,但它們都預示著增長。IEA 在 2021 年的預測報告稱,到 2030 年,燃料電池制造商宣布的產能總計為每年 130 萬個系統。美通社于2022 年 11 月發布并由多個在線市場研究網站出售的通用“汽車燃料電池市場”報告指出,2022 年將有 25,000 臺,到 2030 年將增長到724,000 臺。
增長亮點:據報道, Plug Power (美國紐約州萊瑟姆)目前被列為最大的燃料電池生產商,?其紐約超級工廠的生產能力為每年 700 萬個膜電極組件 (MEA)和 600,000 個燃料電池堆/年。豐田(Toyota, Japan)目前在日本擁有 30,000 個燃料電池/年的生產能力,并且正在增加其位于肯塔基州喬治敦的美國氫動力重型卡車工廠的產能。現代汽車(韓國首爾)將在韓國的兩家工廠增加其目前每年 23,000 個燃料電池的產能——每家工廠的產能為 50,000 個燃料電池/年——將于 2023 年下半年開始生產,目標是到 2030 年達到 700,000 個系統/年。現代還在中國廣州每年生產 6,500 個燃料電池。米其林/雷諾合資企業Symbio(法國韋尼雪)宣布到 2026 年燃料電池年產能為 50,000,到 2028 年為 100,000,到 2030 年為 200,000。Ballard Power Systems(加拿大不列顛哥倫比亞省本那比市)投資 1.3 億美元在中國上海新建一家膜電極組件 (MEA) 工廠,目標是到 2025 年每年為 20,000 臺燃料電池發動機生產 1300 萬個 MEA。從 2023 年第二季度開始,Proton Motor Fuel Cell(德國普赫海姆)的產能將增加到每年 30,000 個電堆和每年 5,000 個 FC 發動機。
根據 E4tech,燃料電池市場包括按應用類型分類的三個主要子部分:
-
便攜式——用于個人電器和電子產品的小型輔助動力裝置 (APU)。
-
固定式——用于大型主電源應用以及熱電聯產 (CHP) 裝置和更大的永久性 APU。
-
運輸——其中汽車占大部分單位,但也包括卡車/公共汽車、鐵路、海運、航空、物料搬運和物流車輛。
E4tech 報告稱,運輸應用在兆瓦 (MW) 方面領先整個市場,而固定應用在燃料電池單元出貨量方面領先。
燃料電池出貨量增長。圖片來源:E4tech“2022 年燃料電池行業回顧” ,第 77 頁(上)和第 78頁(下)?
這三個主要細分市場包括基于所用六種主要電解質的多種燃料電池類型:質子交換膜燃料電池 (PEMFC)、直接甲醇燃料電池 (DMFC)、磷酸燃料電池 (PAFC)、熔融碳酸鹽燃料電池 (MCFC)、 固體氧化物燃料電池(SOFC)和堿性燃料電池(AFC)。PEMFC(主要用于運輸)和 SOFC(用于便攜式和固定式)主導著 MW 和單位出貨量。
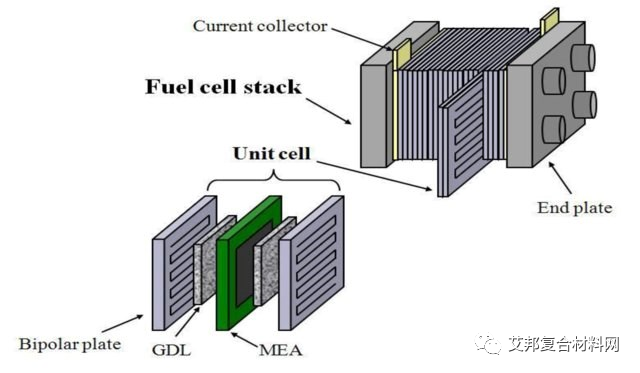
按技術類型/電解質化學分類的燃料電池。圖片來源:E4tech “2022 年燃料電池行業回顧” ,第 57 頁(上)和第 7 頁(下)?
碳纖維復合材料可用于各種燃料電池組件,包括雙極板、氣體擴散層 (GDL) 和端板。與 MEA、雙極板和 GDL 一起構成單元電池,然后重復多次以形成電池堆,由兩個端板固定。電池堆中的電池數量根據產生的功率、應用和使用的技術而變化。例如,Nedstack(荷蘭阿納姆)在其 FCS 7-XXL PEM 燃料電池中使用 48 個電池來提供 6.8 千瓦的電力,而 Bosch SOFC(德國斯圖加特)在其 120 千瓦固體氧化物燃料電池中使用 400 個電池。請注意,這就是為什么制造數百萬個 MEA 的不同工廠可能等同于非常不同數量的燃料電池堆和動力裝置/發動機。
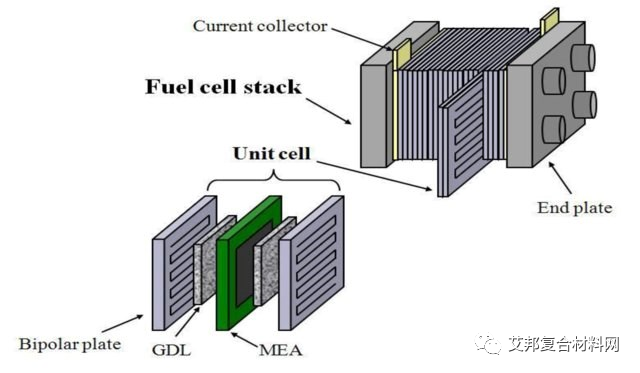
燃料電池和堆的組件
作為單元電池中的組件,每個燃料電池堆需要多組 GDL 和雙極板。正如CW在 2022 年參觀 AvCarb(美國馬薩諸塞州洛厄爾)工廠時所解釋的那樣,GDL 是薄的、高度工程化的碳纖維紙復合材料,層壓有聚四氟乙烯 (PTFE) 和其他涂層。AvCarb 的產品專門針對 PEM 燃料電池,使用其專有的碳纖維石墨化工藝生產 GDL,幫助管理燃料電池電化學反應中的反應物,從而最大限度地提高發電能力。
AvCarb GDL 產品從氧化聚丙烯腈 (PAN) 纖維開始,這些纖維在兩步過程中被拉伸斷裂,以生產稱為棉條(發音為“sly-vers”)的粗束。這些纖維被加捻成直徑較小的絲束或紗線,纏繞在筒管上,織成織物,然后經過多步碳化和處理,生產出含 99.99% 純碳的非織造布。然后應用專有涂層,幫助 GDL 滿足一長串關鍵要求。它必須是化學惰性的、導電的、抗物理降解的,并且能夠壓縮適量,但不能太多。由于燃料電池從氫氣和氧氣中產生水,因此 GDL 必須能夠在不干燥 MEA 的情況下驅散水分,MEA 必須保持濕潤,但不能太濕。“總而言之,這是一種非常復雜的高性能復合結構,完全石墨化,在業內獨一無二,”AvCarb 首席執行官 Roger Masse 說。
AvCarb 在 2022 年將其 Lowell 產能翻了一番,并計劃在全球范圍內進一步擴張。它還正在加速研發以滿足未來的需求。Masse 指出,燃料電池技術發展迅速,各種不同的形狀、尺寸和操作原理的越來越復雜的設計進入市場,需要不同的 GDL 特性和性能屬性。
SGL Carbon(德國威斯巴登)的 SIGRACET 氣體擴散層展示了另一種制造方法,現代汽車集團(韓國首爾)在其 NEXO 燃料電池乘用車的 PEMFC 中使用了這種氣體擴散層。微孔背紙由濕法鋪設短切 PAN 基碳纖維制成,并通過施加碳基微孔層 (MPL) 轉化為 GDL。整個過程在 SGL 網站上都有說明,該公司已經提高了其德國邁廷根工廠的產量,以支持現代汽車和其他公司在不斷增長的燃料電池市場上的表現。
復合材料領域的另一家知名公司 Technical Fiber Products(TFP,伯恩賽德米爾斯,英國坎布里亞)也生產 GDL 數十年。TFP Hydrogen 共享同一個公司總部,最初是 PV3 Technologies,成立于 2011 年,并于 2021 年加入 TFP 集團。它生產一系列碳紙,可以根據固定式和便攜式燃料電池系統的要求進行定制,使用無紡布作為 PEMFC、PAFC 和 DMFC 的 GDL 底物。?
短切碳纖維和石墨填充/乙烯基酯塊狀模塑料 (BMC) 廣泛用于 PEMFC 的雙極板。雙極板作為多功能部件,均勻分布燃料、氣體和空氣;將電流從一個電池單元傳導到另一個電池單元;從活動區域帶走熱量并防止氣體和冷卻劑泄漏。雙極板也是電解槽中的關鍵部件,用于從水中生產氫氣,以及氧化還原(還原氧化)液流電池,用于儲存可再生能源以供日后使用。所有這些應用程序都以高增長為目標。
過去,熱固性材料被認為僅限于小體積和固定式燃料電池應用,因為它們的模具循環時間更長、報廢率更高,并且無法生產與沖壓金屬板一樣薄的模壓復合板。然而,隨著體積的增加和配方改進將成型周期從幾分鐘縮短到幾秒,BMC 成本已顯著下降。根據 LyondellBasell 在 2021 年舉辦的CW網絡研討會上說,導電 BMC 正在成為雙極板中金屬的替代品,由于材料固有的耐腐蝕性能和可模塑成復雜幾何形狀的能力,從而減少了機加工、涂層和其他二次操作,因此有助于降低板和組裝成本。
Hycco(法國圖盧茲)成立于2019年,開發了使用碳纖維熱塑性復合材料的雙極板。它聲稱這是第一批商業化的柔性碳纖維雙極板,與傳統的復合雙極板相比,0.38 毫米厚的腹板可實現 1 毫米厚的板,重量減輕 30-50%。該公司聲稱雙極板占燃料電池堆重量的 75% 和成本的 30%,用于中型/重型卡車的 120 千瓦燃料電池需要多達 600 個板。2022年,Hycco建立了一條能夠生產10,000片/年雙極板的原型線,并正在向2025年250,000片/年的中試線邁進,目標是到2030年擴大到> 100萬片雙極板。它還追求更薄板,目標是到 2024 年實現 0.2 毫米厚的腹板,而目前用于金屬雙極板的標準腹板為 0.1 毫米厚。
超薄碳纖維復合雙極板。Hycco 使用厚度為 0.38 毫米的碳纖維/熱塑性復合材料網開發了雙極板。圖片來源:Hycco 版權所有 2022
Boston Materials(美國馬薩諸塞州波士頓)于 2022 年 5 月宣布與特種材料公司阿科瑪合作,使用其ZRT 復合薄膜制造輕型 ZRT 雙極板。ZRT 復合薄膜采用 100% 回收碳纖維和公司的專利 Z 軸纖維技術制成,可在制造過程中實現更高效、更輕的雙極板和更低的碳足跡。該公司報告稱,雙極板占燃料電池堆總重量的 80%,據稱使用 Boston Materials 的 ZRT 制成的板比現有的不銹鋼板輕 50% 以上,這種重量減輕使燃料電池的容量增加了 30%。
Ensinger Plastics(德國紐弗林根)開發了另一種方法,將其熱塑性化合物與石墨和/或炭黑結合用于雙極板,將玻璃纖維增強聚苯硫醚 (PPS) 用于注塑燃料電池端板。
來源:CompositesWorld、碳纖維及其復合材料技術
原文鏈接:https://www.compositesworld.com/articles/plant-tour-avcarb-lowell-mass-us
原文始發于微信公眾號(艾邦復合材料網):復合材料終端市場:電池和燃料電池 (2023)